Brazing, while a versatile and effective joining method, comes with several disadvantages and limitations that must be considered, particularly for equipment and consumable purchasers. These include the need for high base-metal cleanliness, careful design and manufacturing considerations, the necessity for close fits to facilitate capillary action, and the potential annealing of component parts during the process. These factors can increase production complexity, cost, and time, making it essential to evaluate whether brazing is the most suitable method for a given application.
Key Points Explained:
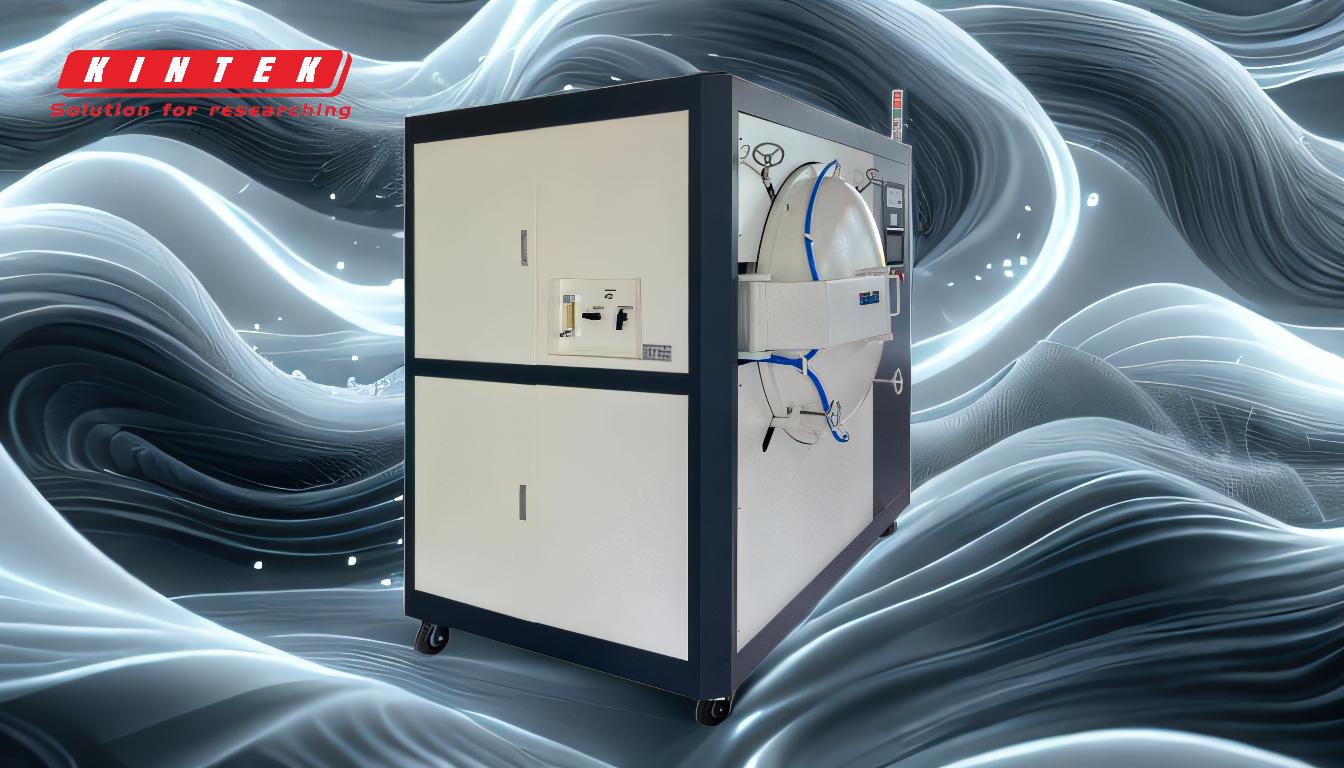
-
High Degree of Base-Metal Cleanliness:
- Brazing requires the base metals to be exceptionally clean to ensure proper adhesion and flow of the filler material. Contaminants such as oils, oxides, or dirt can significantly impair the brazing process, leading to weak joints or defects.
- This necessitates additional pre-cleaning steps, such as chemical cleaning or abrasive processes, which can increase production time and costs. For purchasers, this means investing in cleaning equipment or consumables, adding to the overall expense.
-
Design and Manufacturing Considerations:
- Brazing demands meticulous design and manufacturing planning. Components must be designed to accommodate the brazing process, including the placement of filler material and the creation of joints that facilitate capillary action.
- This often requires close collaboration between design engineers and manufacturing teams, potentially slowing down the production timeline. Purchasers need to account for these design constraints when selecting brazing as a joining method.
-
Close Fits for Capillary Action:
- Brazing relies on capillary action to draw the filler material into the joint. This requires extremely tight tolerances between the parts being joined, which can be challenging to achieve consistently.
- Achieving these close fits may necessitate precision machining or specialized tooling, further increasing costs and complexity. For purchasers, this means ensuring that their suppliers can meet these tight tolerances, which may limit the pool of available vendors.
-
Annealing of Component Parts:
- The high temperatures used in brazing can cause the annealing of component parts, particularly if they are made from materials that are sensitive to heat. Annealing can alter the mechanical properties of the base metal, such as reducing its hardness or strength.
- This may require post-brazing heat treatments to restore the desired properties, adding another step to the manufacturing process. Purchasers must consider whether the base materials can withstand the brazing process without compromising their performance.
-
Material Limitations:
- Not all materials are suitable for brazing. Some metals, such as certain high-temperature alloys or those with high thermal conductivity, may not form strong bonds with conventional brazing filler materials.
- This limits the applicability of brazing in certain industries or for specific components. Purchasers need to carefully evaluate the compatibility of their materials with the brazing process.
-
Cost and Time Implications:
- The additional steps required for cleaning, precision machining, and potential post-brazing treatments can significantly increase both the cost and time required for production.
- For purchasers, this means higher upfront costs and potentially longer lead times, which must be balanced against the benefits of brazing, such as strong, leak-proof joints.
-
Joint Accessibility:
- Brazing requires access to the joint area for the application of heat and filler material. In complex assemblies or components with limited accessibility, this can be a significant challenge.
- This may necessitate the use of specialized equipment or techniques, such as induction brazing or vacuum brazing, which can further increase costs and complexity.
-
Environmental and Safety Considerations:
- The brazing process often involves the use of fluxes or other chemicals to promote wetting and flow of the filler material. These substances can pose environmental and safety hazards, requiring proper handling, storage, and disposal.
- Purchasers must ensure that their facilities are equipped to handle these materials safely, potentially requiring additional investments in safety equipment or training.
In conclusion, while brazing offers several advantages, such as the ability to join dissimilar metals and create strong, durable joints, it also comes with significant disadvantages and limitations. These include the need for high base-metal cleanliness, careful design and manufacturing considerations, close fits for capillary action, potential annealing of component parts, material limitations, cost and time implications, joint accessibility challenges, and environmental and safety considerations. Purchasers must carefully weigh these factors against the benefits of brazing to determine whether it is the most suitable joining method for their specific application.
Summary Table:
Disadvantage | Description |
---|---|
High Base-Metal Cleanliness | Requires exceptional cleanliness to ensure proper adhesion and flow of filler. |
Design and Manufacturing | Demands meticulous planning and collaboration, potentially slowing production. |
Close Fits for Capillary Action | Requires tight tolerances, increasing machining costs and complexity. |
Annealing of Component Parts | High temperatures may alter mechanical properties, requiring post-treatment. |
Material Limitations | Not all materials are suitable for brazing, limiting its applicability. |
Cost and Time Implications | Additional steps increase production time and costs. |
Joint Accessibility | Limited access to joints can complicate the process. |
Environmental and Safety Concerns | Use of fluxes and chemicals requires proper handling and safety measures. |
Need help deciding if brazing is right for your application? Contact our experts today!