Carburizing is a heat treatment process that introduces carbon into the surface of low-carbon steel to enhance its hardness and wear resistance. There are five primary methods of carburizing, each with its unique characteristics, advantages, and applications. These methods include pack carburizing, gas carburizing, liquid carburizing, vacuum carburizing, and plasma carburizing. Each technique varies in terms of the medium used to introduce carbon, the equipment required, and the specific outcomes achieved. Understanding these methods is crucial for selecting the most appropriate technique based on the desired properties of the steel and the specific application requirements.
Key Points Explained:
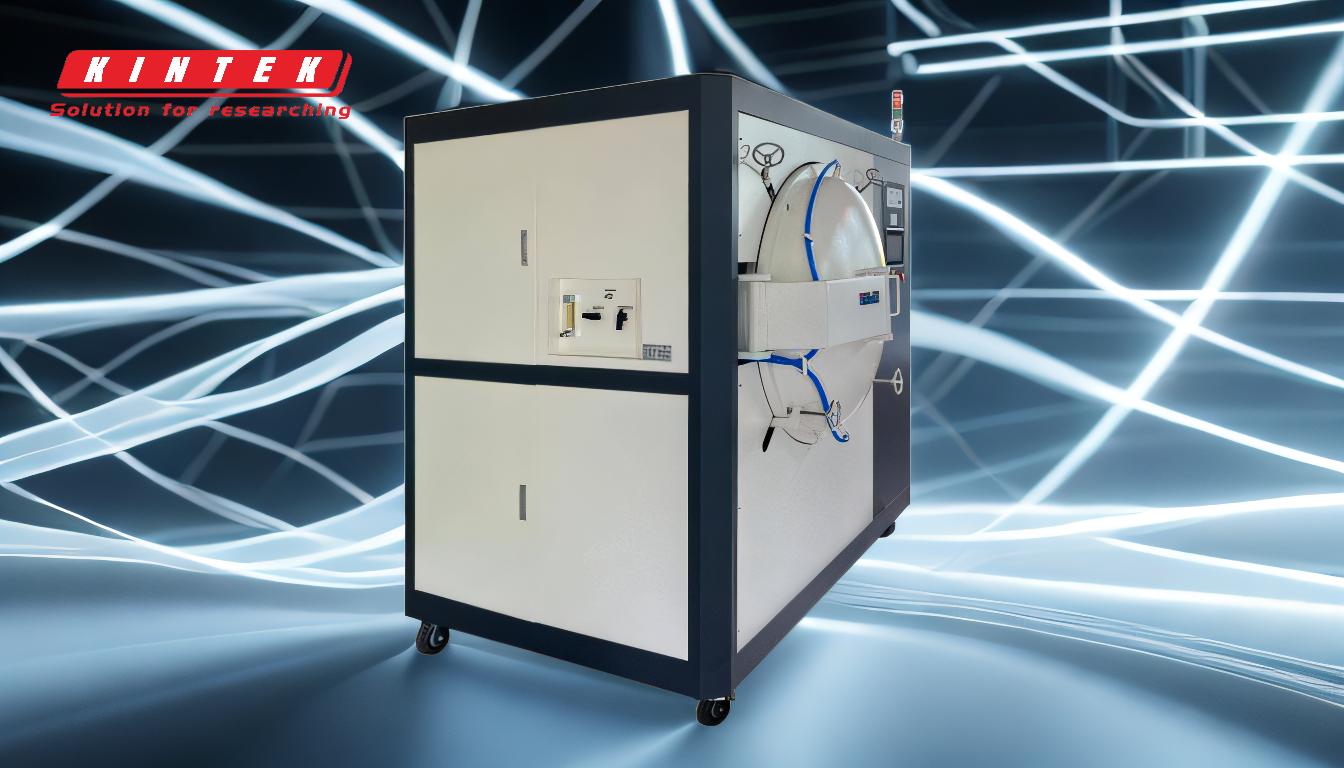
-
Pack Carburizing
- Process: In pack carburizing, the steel parts are packed in a container with a carbon-rich material, such as charcoal or coke. The container is then heated in a furnace to a temperature between 900°C and 950°C, allowing carbon to diffuse into the steel surface.
- Advantages: This method is cost-effective and suitable for large batches of parts. It provides a deep case depth, which is beneficial for components requiring significant wear resistance.
- Disadvantages: The process is time-consuming, and the carbon potential is difficult to control precisely. Additionally, the parts may require additional cleaning after the process due to the carbon-rich packing material.
-
Gas Carburizing
- Process: Gas carburizing involves heating the steel parts in a furnace with a carbon-rich gas atmosphere, typically a mixture of methane, propane, or natural gas. The temperature is maintained between 850°C and 950°C, allowing carbon to diffuse into the steel surface.
- Advantages: This method offers better control over the carbon potential and case depth compared to pack carburizing. It is also faster and more efficient, making it suitable for high-volume production.
- Disadvantages: The equipment required for gas carburizing is more complex and expensive. Additionally, the process requires careful monitoring of the gas composition to ensure consistent results.
-
Liquid Carburizing
- Process: Liquid carburizing, also known as salt bath carburizing, involves immersing the steel parts in a molten salt bath containing carbon-rich compounds, such as sodium cyanide or potassium cyanide. The temperature is typically maintained between 850°C and 950°C.
- Advantages: This method provides rapid and uniform heating, resulting in consistent case depth and carbon concentration. It is also suitable for small and complex parts.
- Disadvantages: The use of cyanide-based salts poses environmental and safety concerns. Additionally, the parts require thorough cleaning after the process to remove any residual salts.
-
Vacuum Carburizing
- Process: Vacuum carburizing is performed in a vacuum furnace, where the steel parts are heated to temperatures between 900°C and 1050°C in a low-pressure environment. A carbon-rich gas, such as methane or propane, is introduced into the furnace to facilitate carbon diffusion.
- Advantages: This method offers excellent control over the carbon potential and case depth, resulting in high-quality, consistent results. It also eliminates the risk of oxidation and decarburization, as the process occurs in a vacuum.
- Disadvantages: The equipment required for vacuum carburizing is expensive, and the process is slower compared to other methods. It is typically used for high-value components where precision and quality are critical.
-
Plasma Carburizing
- Process: Plasma carburizing, also known as ion carburizing, involves placing the steel parts in a vacuum chamber and introducing a carbon-rich gas, such as methane. A plasma is generated by applying a high-voltage electric field, which ionizes the gas and accelerates the carbon ions towards the steel surface.
- Advantages: This method provides precise control over the carbon potential and case depth, resulting in uniform and high-quality carburization. It is also faster and more energy-efficient compared to traditional methods.
- Disadvantages: The equipment required for plasma carburizing is complex and expensive. Additionally, the process is limited to small and medium-sized parts due to the size constraints of the vacuum chamber.
In conclusion, the choice of carburizing method depends on various factors, including the desired properties of the steel, the size and complexity of the parts, production volume, and cost considerations. Each method has its unique advantages and limitations, making it essential to select the most appropriate technique based on the specific requirements of the application.
Summary Table:
Method | Process Overview | Advantages | Disadvantages |
---|---|---|---|
Pack Carburizing | Steel parts packed with carbon-rich material, heated to 900-950°C. | Cost-effective, deep case depth. | Time-consuming, difficult carbon control. |
Gas Carburizing | Steel heated in carbon-rich gas atmosphere (850-950°C). | Better carbon control, faster for high volume. | Expensive equipment, requires gas monitoring. |
Liquid Carburizing | Steel immersed in molten salt bath with carbon compounds (850-950°C). | Rapid, uniform heating, ideal for small parts. | Environmental/safety concerns, post-cleaning. |
Vacuum Carburizing | Steel heated in vacuum furnace with carbon-rich gas (900-1050°C). | Precise control, no oxidation risk. | Expensive, slower process. |
Plasma Carburizing | Steel in vacuum chamber with ionized carbon-rich gas (plasma). | Energy-efficient, uniform results. | Complex equipment, limited to small/medium parts. |
Need help selecting the right carburizing method for your application? Contact our experts today!