Brazing is a versatile metal-joining process that offers numerous advantages, such as the ability to join dissimilar materials, cost-effectiveness, and high-integrity results. It is suitable for both simple and complex designs and can be applied to various industries. However, it also has some disadvantages, including potential material hardness reduction, high energy consumption, and technical challenges. Different brazing methods, such as furnace brazing, vacuum brazing, and laser brazing, each have their own specific benefits and drawbacks, making them suitable for different applications. Understanding these pros and cons is crucial for selecting the right brazing method for specific needs.
Key Points Explained:
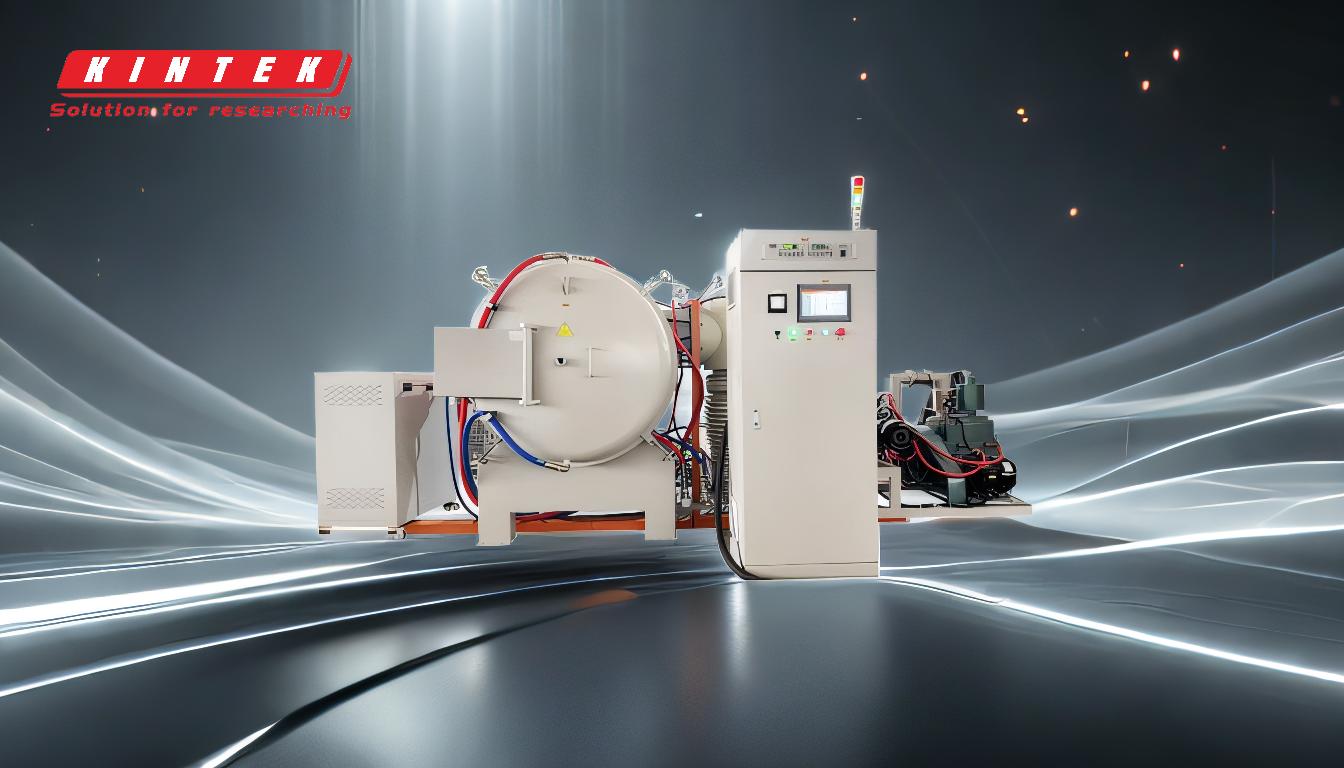
-
Advantages of Brazing:
- Cost-Effectiveness: Brazing is generally more economical compared to other joining methods like welding, especially for large-scale production.
- Material Versatility: It allows for the joining of dissimilar materials, including metals and non-metals, which might be unweldable using traditional methods.
- Design Flexibility: Engineers can use brazing to join simple or complex designs, whether it involves a single joint or multiple joints.
- High-Integrity Joints: Brazing produces strong, durable joints that are often leak-proof and resistant to corrosion.
- Controlled Process: Methods like furnace brazing and automatic brazing machines provide precise control over the process, ensuring consistent and accurate results.
-
Disadvantages of Brazing:
- Material Hardness Reduction: High-temperature brazing processes, such as vacuum brazing, can reduce the hardness of certain materials, affecting their mechanical properties.
- High Process Requirements: Brazing often requires specialized equipment and controlled environments, such as oxygen-free atmospheres, which can increase operational complexity.
- Energy Consumption: Some brazing methods, particularly those involving high temperatures, can be energy-intensive.
- Technical Difficulty: Achieving optimal results may require skilled operators and careful process control, especially in methods like vacuum brazing.
- Cleaning and Environmental Costs: Pre-welding cleaning and post-welding environmental protection measures can add to the overall cost and time of the process.
-
Specific Brazing Methods and Their Pros and Cons:
-
Furnace Brazing:
- Advantages: Provides an oxygen-free environment, ensures uniform heating, and is suitable for joining complex components like heat exchangers, leading to improved efficiency and longer service life.
- Disadvantages: Requires specialized equipment and may have longer processing times compared to other methods.
-
Vacuum Brazing:
- Advantages: Ideal for high-precision applications and materials that require an oxygen-free environment.
- Disadvantages: High energy consumption, long processing times, and potential reduction in material hardness.
-
Laser Brazing:
- Advantages: Offers high precision, shorter joining times, and the ability to join materials of different thicknesses. It is ideal for intricate shapes and sizes.
- Disadvantages: Requires advanced equipment and may have higher initial costs.
-
Automatic Brazing Machines:
- Advantages: Increases production speed, reduces labor costs, and ensures consistent results. It is suitable for joining various types of metals and components of different shapes and sizes.
- Disadvantages: Initial investment in machinery can be high, and setup may require technical expertise.
-
Furnace Brazing:
-
Applications and Suitability:
- Brazing is widely used in industries such as automotive, aerospace, electronics, and HVAC (heating, ventilation, and air conditioning). The choice of brazing method depends on the specific requirements of the application, including material compatibility, joint design, and production volume.
By carefully considering these advantages and disadvantages, manufacturers and engineers can select the most appropriate brazing method for their specific needs, ensuring optimal results in terms of strength, efficiency, and cost-effectiveness.
Summary Table:
Aspect | Advantages | Disadvantages |
---|---|---|
Cost-Effectiveness | Economical for large-scale production | High initial investment for specialized equipment |
Material Versatility | Joins dissimilar materials, including metals and non-metals | Potential reduction in material hardness |
Design Flexibility | Suitable for simple and complex designs | Requires skilled operators and precise process control |
High-Integrity Joints | Produces strong, leak-proof, and corrosion-resistant joints | High energy consumption and environmental costs |
Brazing Methods | Furnace Brazing: Uniform heating, oxygen-free environment | Longer processing times |
Vacuum Brazing: High precision, ideal for oxygen-free materials | High energy consumption, long processing times | |
Laser Brazing: High precision, shorter joining times | Requires advanced equipment, higher initial costs | |
Automatic Brazing Machines: Increased production speed, consistent results | High initial investment, technical expertise required |
Need help selecting the right brazing method for your application? Contact our experts today!