Fluidized bed systems, particularly fluidized-bed reactors (FBRs) and pyrolyzers, are widely used in industries such as chemical processing, petroleum refining, and biomass conversion. These systems offer significant advantages, including uniform temperature distribution, efficient heat transfer, and high yields of desired products like bio-oils. However, they also come with challenges, such as the need for small particle sizes, high operating costs, and the requirement for large quantities of inert gases. Understanding these pros and cons is essential for evaluating their suitability for specific applications.
Key Points Explained:
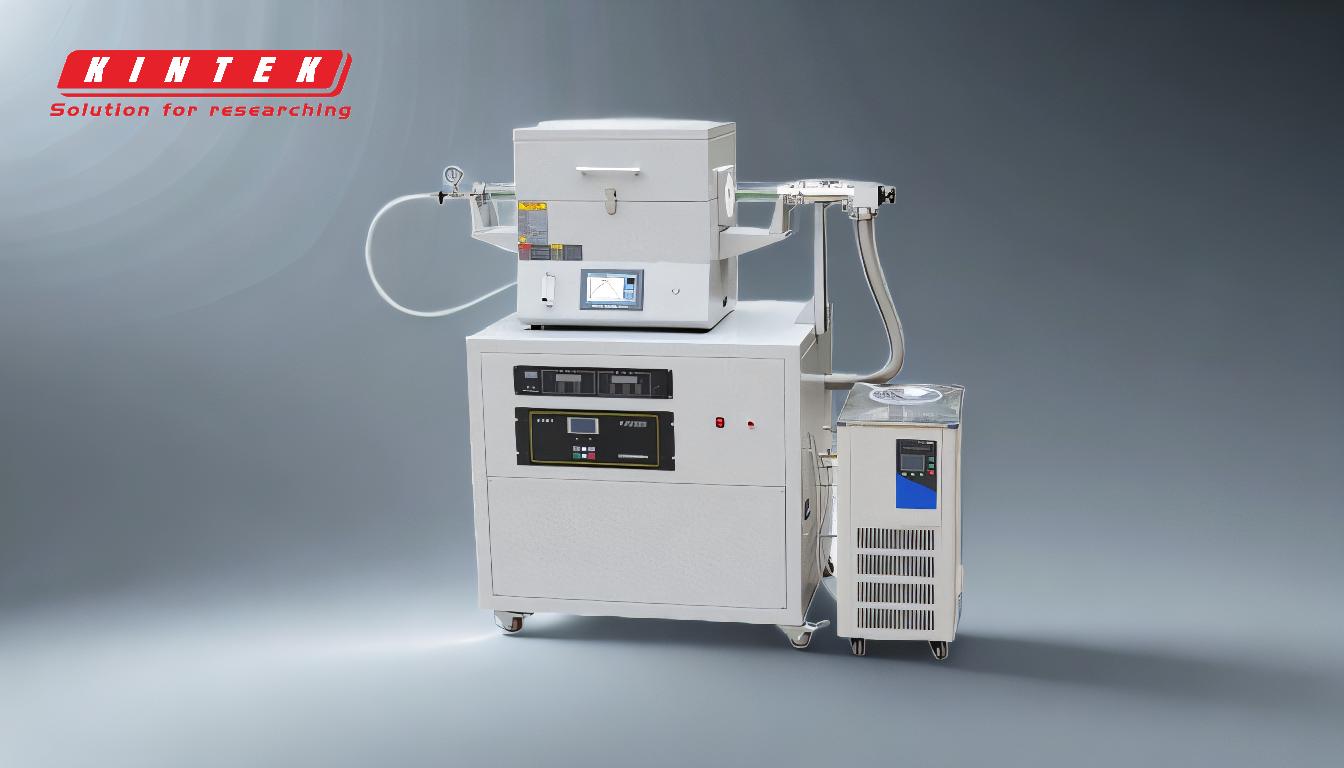
-
Advantages of Fluidized Bed Systems
-
Uniform Temperature Distribution:
Fluidized bed systems ensure uniform temperature gradients, which prevent hot or cold spots. This is particularly beneficial for exothermic reactions, as it minimizes the risk of thermal runaway and ensures consistent product quality. -
Efficient Heat Transfer:
The fluid-like behavior of solid particles in the bed enhances heat transfer between the particles and the surrounding gas. This results in faster and more efficient heating, which is crucial for processes like pyrolysis. -
High Yield of Desired Products:
Fluidized-bed pyrolyzers, for example, can achieve high bio-oil yields of up to 75%. This makes them highly effective for converting biomass into valuable byproducts like bio-oils and gases. -
Uniform Particle Mixing:
The fluidization process ensures complete mixing of particles, eliminating radial and axial concentration gradients. This improves reaction efficiency and product consistency. -
Medium Complexity in Construction and Operation:
While fluidized bed systems are more complex than some alternatives, they are generally easier to construct and operate compared to other advanced reactors. -
Ease of Scaling Up:
Fluidized bed systems are relatively easy to scale up for industrial applications, making them suitable for large-scale production. -
Continuous Operation:
Unlike batch processes, fluidized bed reactors can operate continuously, eliminating the need for frequent startups and shutdowns. This improves production efficiency and reduces downtime.
-
Uniform Temperature Distribution:
-
Disadvantages of Fluidized Bed Systems
-
Requirement for Small Particle Sizes:
Fluidized bed systems require feed materials to be finely ground into small particles to achieve proper fluidization. This preprocessing step can increase operational complexity and costs. -
High Operating Costs:
The need for large quantities of inert gases (e.g., nitrogen) to maintain the fluidized state and prevent unwanted reactions can significantly increase operating expenses. -
Large Quantity of Inert Gases:
The reliance on inert gases not only raises costs but also introduces logistical challenges, such as storage and handling. -
Erosion and Wear:
The constant movement of particles in the bed can lead to erosion and wear of reactor components, requiring frequent maintenance and replacement. -
Complexity in Handling Fine Particles:
Fine particles can be difficult to handle and may lead to issues like clogging or loss of material during processing. -
Limited Applicability for Certain Feedstocks:
While fluidized bed systems are effective for particulate substrates like woody biomass, they may not be suitable for all types of feedstocks, particularly those with irregular shapes or high moisture content.
-
Requirement for Small Particle Sizes:
-
Applications and Suitability
-
Biomass Conversion:
Fluidized bed systems are highly effective for converting biomass into bio-oils, gases, and other valuable byproducts. Their ability to handle particulate substrates makes them ideal for woody biomass and similar materials. -
Chemical and Petroleum Industries:
These systems are widely used in the chemical and petroleum industries for processes like catalytic cracking and gasification, where uniform temperature and efficient heat transfer are critical. -
Exothermic Reactions:
The uniform temperature gradients in fluidized bed reactors make them particularly suitable for exothermic reactions, where controlling heat release is essential.
-
Biomass Conversion:
-
Considerations for Purchasers
-
Cost-Benefit Analysis:
Purchasers should weigh the high initial and operating costs against the benefits of high product yields and efficient operation. -
Feedstock Compatibility:
It is important to ensure that the feedstock is compatible with the fluidized bed system, particularly in terms of particle size and moisture content. -
Maintenance Requirements:
The potential for erosion and wear should be factored into maintenance plans and budgets. -
Scalability:
For large-scale production, the ease of scaling up fluidized bed systems is a significant advantage.
-
Cost-Benefit Analysis:
In conclusion, fluidized bed systems offer numerous advantages, including uniform temperature distribution, efficient heat transfer, and high product yields. However, their disadvantages, such as high operating costs and the need for small particle sizes, must be carefully considered. By evaluating these factors, purchasers can determine whether fluidized bed systems are the right choice for their specific applications.
Summary Table:
Aspect | Advantages | Disadvantages |
---|---|---|
Temperature Control | Uniform temperature distribution, prevents hot/cold spots | Requires small particle sizes for proper fluidization |
Heat Transfer | Efficient heat transfer, faster heating for processes like pyrolysis | High operating costs due to inert gas requirements |
Product Yield | High yields of desired products (e.g., bio-oils up to 75%) | Large quantities of inert gases needed, increasing logistical challenges |
Particle Mixing | Complete mixing, eliminates concentration gradients | Erosion and wear of reactor components due to constant particle movement |
Scalability | Easy to scale up for industrial applications | Complex handling of fine particles, potential for clogging or material loss |
Operation | Continuous operation, reduces downtime and improves efficiency | Limited applicability for feedstocks with irregular shapes or high moisture content |
Ready to optimize your industrial processes with fluidized bed systems? Contact our experts today for tailored solutions!