Heat treatment is a critical process in metallurgy and manufacturing, offering numerous advantages such as enhancing material properties, improving machinability, and increasing durability. However, it also has limitations, including potential material distortion, high energy consumption, and the need for precise control. Below is a detailed exploration of the advantages and limitations of heat treatment processes.
Key Points Explained:
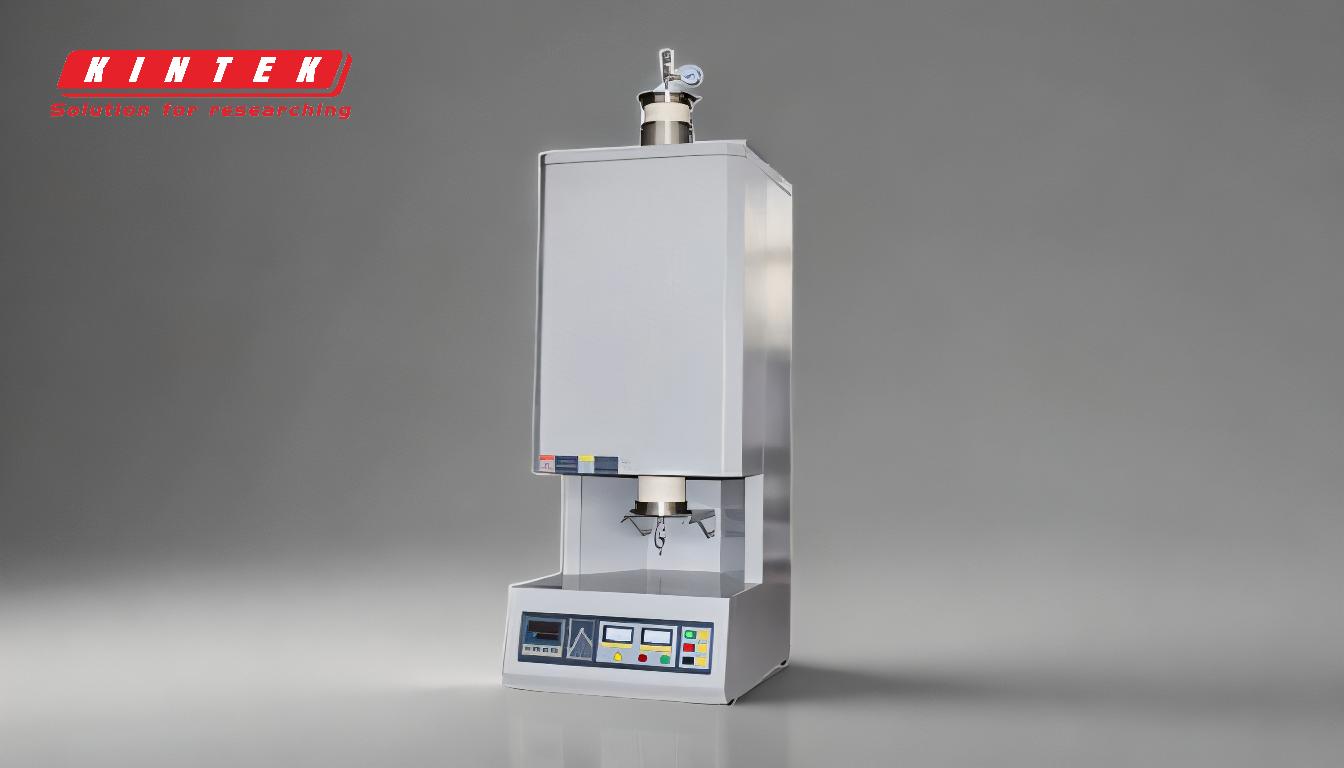
-
Advantages of Heat Treatment:
-
Improved Mechanical Properties:
- Heat treatment can significantly enhance the mechanical properties of metals, such as hardness, strength, toughness, ductility, and elasticity. For example, quenching increases hardness, while annealing improves ductility.
- This makes materials more suitable for specific applications, such as load-bearing components or tools requiring wear resistance.
-
Stress Relief:
- Heat treatment relieves internal stresses in materials, making them easier to machine, weld, or form. This is particularly useful after processes like welding or cold working, which can introduce residual stresses.
-
Enhanced Wear and Corrosion Resistance:
- Processes like case hardening or nitriding introduce wear-resistant characteristics to the surface of metals, extending their lifespan in abrasive environments.
- Certain heat treatments can also improve corrosion resistance, making materials more durable in harsh conditions.
-
Improved Brittleness and Flexibility:
- Heat treatment can reduce brittleness in materials, making them less prone to cracking or failure under stress. For example, tempering after quenching reduces brittleness while maintaining hardness.
-
Tailored Electrical and Magnetic Properties:
- Heat treatment can modify the electrical conductivity and magnetic properties of metals, which is essential for applications in electronics and electrical engineering.
-
Versatility Across Materials:
- Heat treatment is applicable to a wide range of metals and alloys, including steel, aluminum, and titanium, making it a versatile process in manufacturing.
-
Improved Mechanical Properties:
-
Limitations of Heat Treatment:
-
Material Distortion:
- Rapid heating or cooling during heat treatment can cause warping, cracking, or distortion in the material. This is particularly problematic for complex or thin-walled components.
-
Energy Consumption:
- Heat treatment processes often require high temperatures and prolonged heating cycles, leading to significant energy consumption and increased operational costs.
-
Precision and Control Requirements:
- Achieving the desired material properties requires precise control of temperature, cooling rates, and time. Any deviation can result in suboptimal outcomes or material failure.
-
Limited Applicability to Non-Metallic Materials:
- Heat treatment is primarily effective for metals and alloys. Non-metallic materials, such as plastics or ceramics, generally do not respond to heat treatment in the same way.
-
Surface Oxidation and Decarburization:
- Exposure to high temperatures can cause surface oxidation or decarburization, which may degrade the material's surface properties and require additional finishing processes.
-
Cost and Complexity:
- The equipment and expertise required for heat treatment can be expensive, especially for specialized processes like vacuum or controlled atmosphere heat treatment.
-
Environmental Impact:
- Some heat treatment processes involve the use of hazardous chemicals or produce emissions, raising environmental and safety concerns.
-
Material Distortion:
-
Balancing Advantages and Limitations:
- While heat treatment offers significant benefits, its limitations must be carefully managed. For example, distortion can be minimized by using controlled cooling rates or preheating, and energy consumption can be reduced through process optimization.
- The choice of heat treatment process should align with the material's properties, the desired outcomes, and the specific application requirements.
In summary, heat treatment is a powerful tool for enhancing material properties and performance, but it requires careful consideration of its limitations to achieve optimal results. By understanding both the advantages and constraints, manufacturers can make informed decisions to improve product quality and durability.
Summary Table:
Aspect | Advantages | Limitations |
---|---|---|
Mechanical Properties | Enhances hardness, strength, toughness, ductility, and elasticity. | Rapid heating/cooling can cause distortion or cracking. |
Stress Relief | Reduces internal stresses, improving machinability and weldability. | Requires precise control to avoid suboptimal outcomes. |
Wear/Corrosion Resistance | Increases surface durability and resistance to harsh environments. | High energy consumption and operational costs. |
Brittleness/Flexibility | Reduces brittleness, improving material flexibility. | Limited applicability to non-metallic materials. |
Electrical/Magnetic Properties | Modifies conductivity and magnetic properties for specialized applications. | Surface oxidation or decarburization may occur. |
Versatility | Applicable to a wide range of metals and alloys. | Equipment and expertise can be costly and complex. |
Optimize your heat treatment process—contact our experts today for tailored solutions!