Brazing offers several advantages over welding, making it a preferred choice in many industrial and manufacturing applications. Unlike welding, brazing does not melt the base metals, allowing for precise control of tolerances and minimizing the risk of warping or distortion. It is particularly effective for joining dissimilar metals and complex parts, including nonmetals, and is well-suited for high-volume production due to its cost-effectiveness and efficiency. Additionally, brazed joints are strong, reliable, and capable of withstanding various environmental conditions, making them ideal for industries such as automotive, HVAC, and cookware.
Key Points Explained:
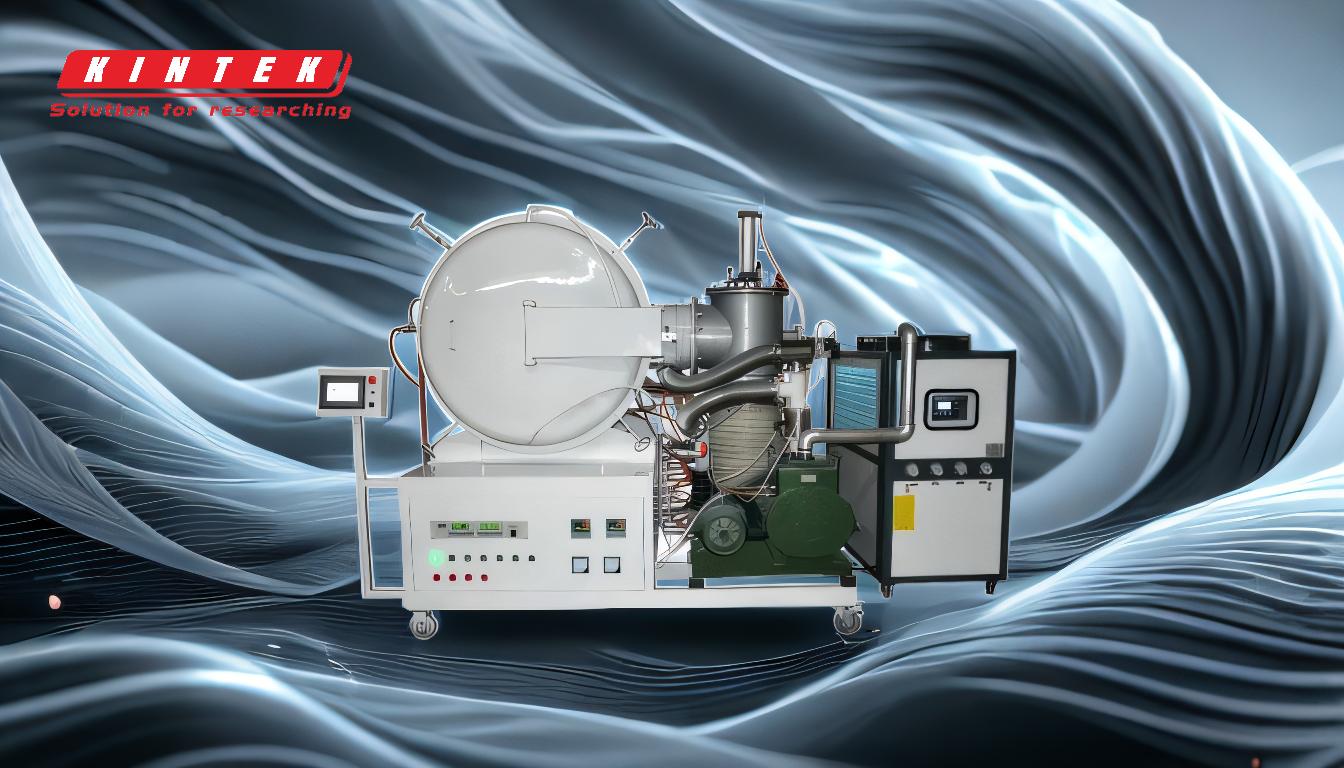
-
No Melting of Base Metals
- Brazing does not melt the parent metals, which allows for tighter control over tolerances and reduces the risk of warping or distortion.
- This is particularly advantageous in applications requiring high precision, such as aerospace or electronics manufacturing.
- Welding, on the other hand, melts both the filler and base metals, which can lead to thermal distortion and challenges in maintaining precise dimensions.
-
Ability to Join Dissimilar Metals
- Brazing excels at joining dissimilar metals, such as copper to steel or aluminum to stainless steel, which is often difficult or impossible with welding.
- This capability is critical in industries like HVAC and automotive, where different materials are frequently combined for optimal performance.
- Welding typically requires similar metals to achieve a strong bond, limiting its versatility in certain applications.
-
Suitability for Complex and High-Volume Production
- Brazing is highly efficient for joining complex parts, including those with intricate geometries or nonmetallic components.
- It is well-suited for high-volume manufacturing due to its repeatability and cost-effectiveness.
- Welding, while strong, can be more labor-intensive and less efficient for mass production, especially when dealing with complex designs.
-
Reduced Thermal Distortion
- Brazing generates lower heat compared to welding, which minimizes thermal distortion and stress in the joined materials.
- This makes brazing ideal for thin or delicate materials that could be damaged by the high heat of welding.
- Welding's high heat input can cause significant distortion, particularly in thin sheets or heat-sensitive materials.
-
Strong and Reliable Joints
- Brazed joints are as strong as the base metals being joined, providing reliable and durable connections.
- These joints are capable of withstanding mechanical stress, vibration, and environmental factors, making them suitable for demanding applications.
- While welding also produces strong joints, brazing offers comparable strength without the need for melting the base metals.
-
Cost-Effectiveness
- Brazing is often more cost-effective than welding, especially for high-volume projects, due to lower energy consumption and reduced need for post-processing.
- The process is less labor-intensive and can be easily automated, further reducing costs.
- Welding may require additional steps, such as grinding or heat treatment, which can increase production time and expenses.
-
Versatility Across Industries
- Brazing is widely used in industries such as cookware, automotive, HVAC, and electronics due to its flexibility and reliability.
- It can be applied to a wide range of materials and thicknesses, making it a versatile joining solution.
- While welding is also versatile, it is often limited to specific materials and applications where high heat resistance is required.
In summary, brazing offers significant advantages over welding, including precision, versatility, cost-effectiveness, and reduced thermal distortion. These benefits make it a preferred choice for many industrial applications, particularly when joining dissimilar metals, complex parts, or high-volume production runs. While welding remains superior for high-strength and high-temperature applications, brazing provides a reliable and efficient alternative for a wide range of joining needs.
Summary Table:
Advantage | Brazing | Welding |
---|---|---|
Base Metal Melting | Does not melt base metals, reducing warping and distortion. | Melts base metals, often causing thermal distortion. |
Joining Dissimilar Metals | Effective for joining dissimilar metals like copper to steel. | Limited to similar metals for strong bonds. |
Complex & High-Volume | Ideal for complex parts and high-volume production due to efficiency. | Less efficient for mass production and complex designs. |
Thermal Distortion | Lower heat reduces distortion, ideal for thin or delicate materials. | High heat can cause significant distortion in thin or heat-sensitive materials. |
Joint Strength | Strong, reliable joints that withstand stress, vibration, and environments. | Strong joints, but may require additional post-processing. |
Cost-Effectiveness | More cost-effective for high-volume projects with lower energy use. | Higher costs due to labor, energy, and post-processing. |
Industry Versatility | Widely used in automotive, HVAC, cookware, and electronics. | Versatile but limited to specific materials and high-heat applications. |
Ready to explore how brazing can enhance your manufacturing process? Contact us today for expert advice!