Electric Arc Furnaces (EAFs) offer numerous advantages over traditional blast furnaces, making them a preferred choice in modern steel production. Their key benefits include improved energy efficiency, flexibility in raw material usage, lower capital investment, and the ability to produce a wide range of steel grades. EAFs are self-contained systems that can operate on a smaller footprint, making them suitable for mini-mills and locations where blast furnaces are impractical. Additionally, they support 100% scrap metal recycling, reduce reliance on fossil fuels, and feature programmable and automated processes, enhancing productivity and operational control.
Key Points Explained:
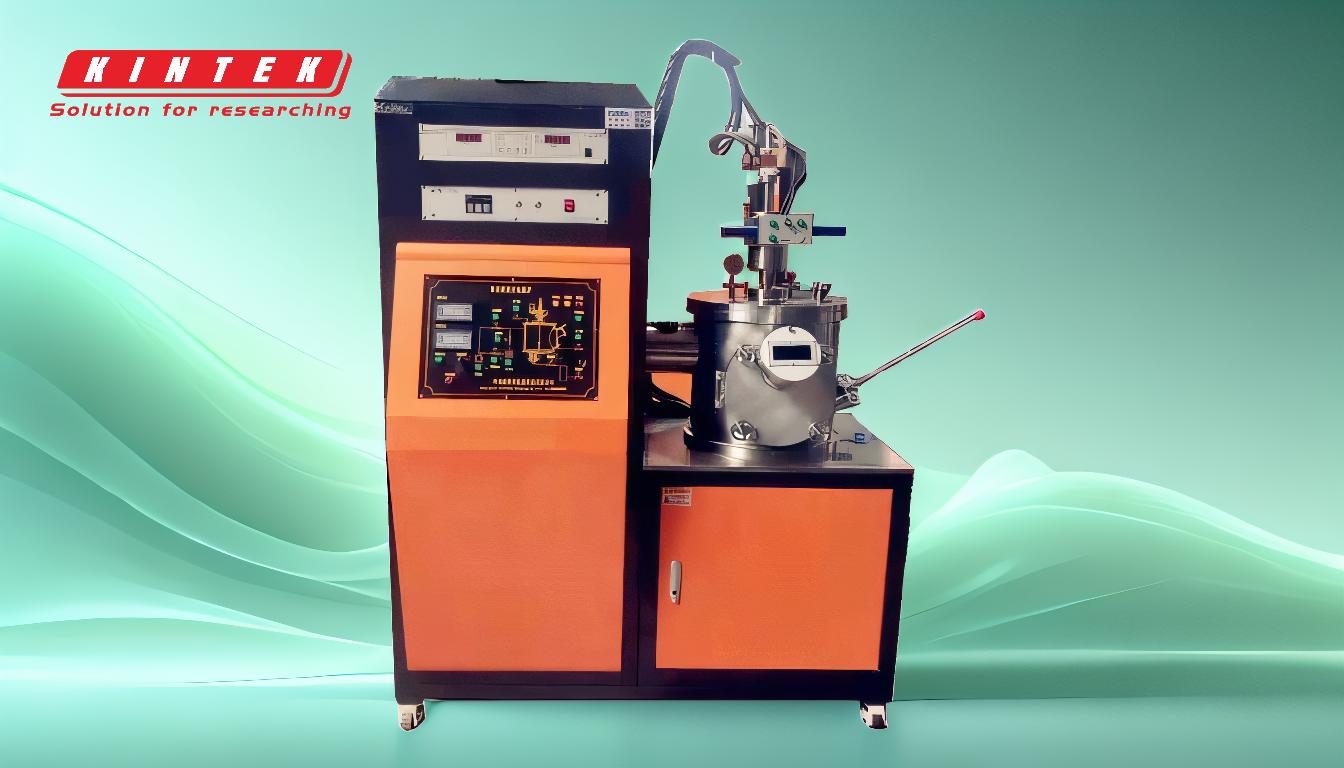
-
Energy Efficiency and Reduced Fuel Dependency
- EAFs do not require large amounts of fuel for combustion or continuous coke addition, unlike blast furnaces.
- This reduces energy consumption and operational costs, making the process more environmentally friendly.
- The ability to use 100% scrap material further lowers energy intensity compared to producing steel from virgin ores.
-
Flexibility in Raw Material Usage
- EAFs can process a variety of charge materials, including scrap metal, sponge iron, pig iron, and hot metal.
- This flexibility allows manufacturers to adapt to market conditions and raw material availability.
- The ability to recycle scrap metal supports sustainability and reduces waste.
-
Lower Capital Investment
- EAFs require less initial capital outlay compared to blast furnaces.
- Their compact design and smaller footprint make them suitable for mini-mills and smaller-scale operations.
- This lowers barriers to entry for new manufacturers and reduces infrastructure costs.
-
Scalability and Compact Design
- EAFs can be scaled down to operate as mini-mills, making them feasible in locations where blast furnaces are impractical.
- Their self-contained nature allows for easier integration into existing facilities.
-
Wide Range of Steel Grades
- EAFs can produce a full spectrum of steel grades, meeting diverse industrial requirements.
- This versatility makes them suitable for various applications, from construction to automotive manufacturing.
-
Programmable and Automated Processes
- EAFs feature advanced automation and programmable controls, enhancing precision and consistency in steel production.
- Automation reduces labor costs and minimizes human error, improving overall efficiency.
- The ability to start and stop the melting process as needed adds operational flexibility.
-
High Productivity
- EAFs can generate twice as much steel as traditional methods in the same timeframe.
- Controlled processes and optimized energy use contribute to higher output and faster production cycles.
-
Environmental Benefits
- EAFs support 100% scrap metal recycling, reducing the need for mining and conserving natural resources.
- Lower emissions and reduced reliance on fossil fuels contribute to a smaller carbon footprint.
- These features align with global sustainability goals and regulatory requirements.
-
Operational Flexibility
- EAFs can be quickly started and stopped, allowing manufacturers to respond to demand fluctuations.
- This adaptability reduces idle time and optimizes resource utilization.
In summary, Electric Arc Furnaces offer a combination of energy efficiency, flexibility, cost-effectiveness, and environmental benefits, making them a superior choice for modern steel production. Their ability to adapt to various raw materials, produce high-quality steel grades, and operate on a smaller scale ensures their relevance in both large and small manufacturing setups.
Summary Table:
Advantages | Key Benefits |
---|---|
Energy Efficiency | Reduces fuel dependency and operational costs; uses 100% scrap material. |
Raw Material Flexibility | Processes scrap metal, sponge iron, pig iron, and hot metal for adaptability. |
Lower Capital Investment | Compact design and smaller footprint reduce infrastructure costs. |
Scalability | Suitable for mini-mills and locations where blast furnaces are impractical. |
Wide Steel Grade Range | Produces diverse steel grades for various industrial applications. |
Automation & Control | Programmable processes enhance precision, consistency, and labor efficiency. |
High Productivity | Generates twice as much steel as traditional methods in the same timeframe. |
Environmental Benefits | Supports 100% scrap recycling, reduces emissions, and conserves natural resources. |
Operational Flexibility | Quick start/stop capability adapts to demand fluctuations, reducing idle time. |
Ready to upgrade your steel production with an Electric Arc Furnace? Contact our experts today to learn more!