Electro-deposition, also known as electroplating, is a widely used process in various industries due to its numerous advantages. This technique involves the deposition of a metal or alloy onto a conductive surface using an electric current. The process offers several benefits, including improved corrosion resistance, enhanced appearance, increased wear resistance, and the ability to create uniform coatings on complex geometries. Additionally, electro-deposition is cost-effective, environmentally friendly when managed properly, and allows for precise control over coating thickness and composition. These advantages make it a preferred method for applications ranging from automotive and aerospace industries to electronics and decorative finishes.
Key Points Explained:
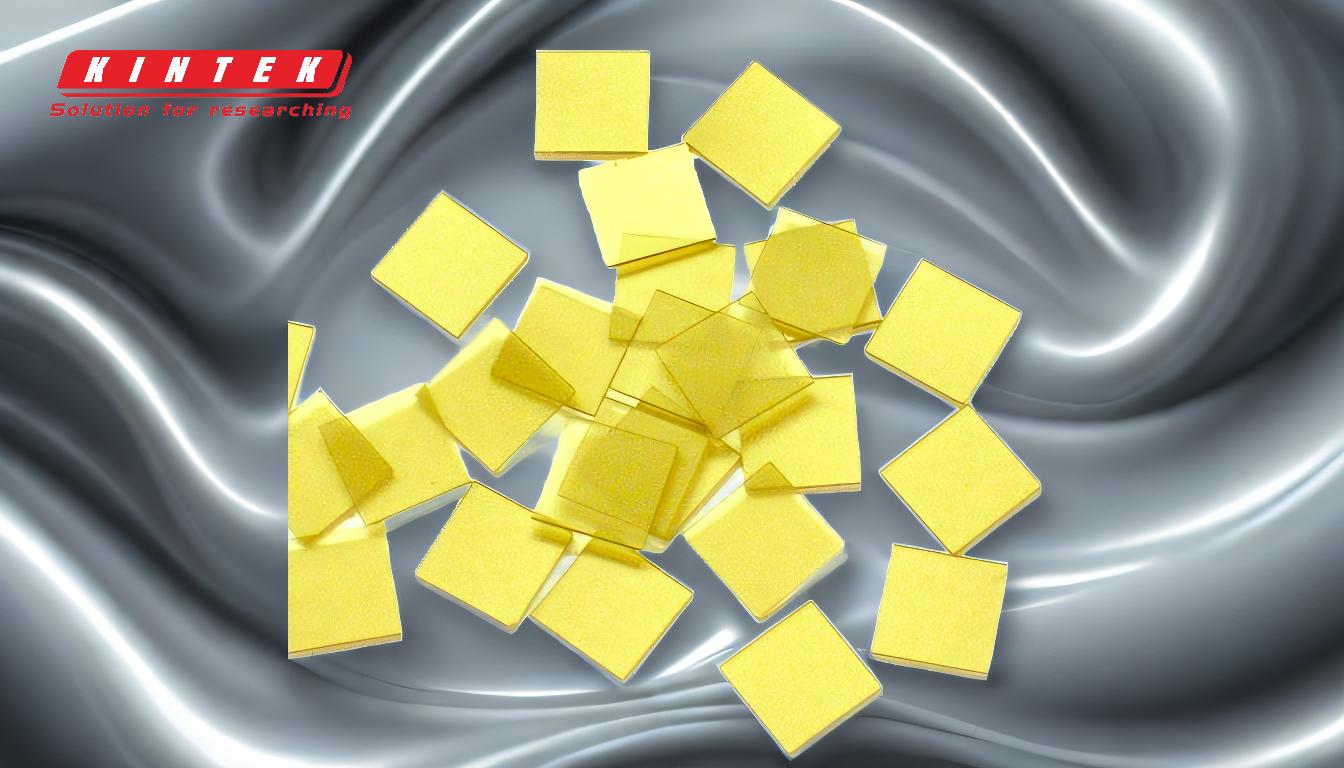
-
Improved Corrosion Resistance:
- Electro-deposition provides a protective layer that significantly enhances the corrosion resistance of the base material. This is particularly important for metals like steel, which are prone to rust and degradation when exposed to moisture and corrosive environments.
- The protective layer acts as a barrier, preventing direct contact between the base material and corrosive agents, thereby extending the lifespan of the component.
-
Enhanced Appearance:
- Electro-deposition can be used to apply decorative finishes, such as chrome or gold plating, which improve the aesthetic appeal of products. This is especially valuable in industries like jewelry, automotive, and consumer electronics.
- The process allows for a wide range of colors and finishes, enabling manufacturers to meet specific design requirements and consumer preferences.
-
Increased Wear Resistance:
- The deposited metal layer increases the hardness and wear resistance of the surface, making it more durable and capable of withstanding mechanical stress and abrasion.
- This is particularly beneficial for components that are subject to friction and wear, such as gears, bearings, and cutting tools.
-
Uniform Coatings on Complex Geometries:
- Electro-deposition is capable of producing uniform coatings even on complex shapes and intricate designs. This is due to the nature of the process, which allows the electric current to evenly distribute the deposited material across the entire surface.
- This uniformity is crucial for ensuring consistent performance and protection, especially in components with detailed or irregular shapes.
-
Cost-Effectiveness:
- Compared to other coating methods, electro-deposition is relatively cost-effective. The process requires less material waste and can be easily scaled for large production runs.
- Additionally, the ability to reuse the electrolyte solution in some systems further reduces costs and minimizes environmental impact.
-
Environmental Friendliness:
- When managed properly, electro-deposition can be an environmentally friendly process. Modern electroplating systems often include waste treatment and recycling mechanisms to minimize the release of harmful chemicals into the environment.
- The use of non-toxic or less toxic materials in the plating process also contributes to its eco-friendliness.
-
Precise Control Over Coating Thickness and Composition:
- Electro-deposition allows for precise control over the thickness and composition of the deposited layer. This is achieved by adjusting parameters such as current density, temperature, and plating time.
- This level of control is essential for applications where specific performance characteristics, such as electrical conductivity or thermal resistance, are required.
-
Versatility in Material Selection:
- Electro-deposition can be used with a wide range of metals and alloys, including nickel, copper, zinc, gold, silver, and more. This versatility allows manufacturers to select the most appropriate material for their specific application.
- The ability to deposit multiple layers of different materials further enhances the functionality and performance of the coated product.
-
Improved Adhesion and Bonding:
- The electro-deposition process promotes strong adhesion between the deposited layer and the base material. This is due to the electrochemical bonding that occurs during the plating process.
- Strong adhesion is critical for ensuring the durability and longevity of the coating, especially in high-stress applications.
-
Compatibility with Various Substrates:
- Electro-deposition is compatible with a wide range of substrates, including metals, plastics, and ceramics. This makes it a versatile solution for coating different types of materials.
- The ability to coat non-conductive materials, such as plastics, with a conductive layer further expands the potential applications of electro-deposition.
In summary, electro-deposition offers a multitude of advantages that make it a valuable process across various industries. Its ability to enhance corrosion resistance, improve appearance, increase wear resistance, and provide uniform coatings on complex geometries, combined with its cost-effectiveness and environmental friendliness, makes it a preferred choice for many applications. The precise control over coating thickness and composition, along with the versatility in material selection and compatibility with various substrates, further underscores the importance of electro-deposition in modern manufacturing and engineering.
Summary Table:
Advantage | Key Benefit |
---|---|
Improved Corrosion Resistance | Protects base material from rust and degradation, extending component lifespan. |
Enhanced Appearance | Enables decorative finishes like chrome or gold plating for aesthetic appeal. |
Increased Wear Resistance | Enhances surface hardness, making components more durable. |
Uniform Coatings on Complex Shapes | Ensures even coating distribution on intricate geometries. |
Cost-Effectiveness | Reduces material waste and allows scalable production. |
Environmental Friendliness | Minimizes harmful chemical release with proper waste management. |
Precise Control Over Coatings | Adjusts thickness and composition for specific performance needs. |
Versatility in Material Selection | Works with metals like nickel, copper, gold, and more. |
Improved Adhesion and Bonding | Ensures strong, durable coatings for high-stress applications. |
Compatibility with Various Substrates | Coats metals, plastics, and ceramics for diverse applications. |
Unlock the full potential of electro-deposition for your projects—contact our experts today to learn more!