Refractory materials are essential in high-temperature industrial processes due to their unique properties. They offer several advantages, including high thermal resistance, chemical stability, mechanical strength, and durability under extreme conditions. These materials are designed to withstand temperatures exceeding 1,000°C without significant degradation, making them ideal for applications in furnaces, kilns, and reactors. Additionally, refractory materials are resistant to chemical corrosion, thermal shock, and abrasion, ensuring long-term performance and cost-effectiveness. Their ability to maintain structural integrity under stress and harsh environments reduces downtime and maintenance costs, making them indispensable in industries like steelmaking, cement production, and glass manufacturing.
Key Points Explained:
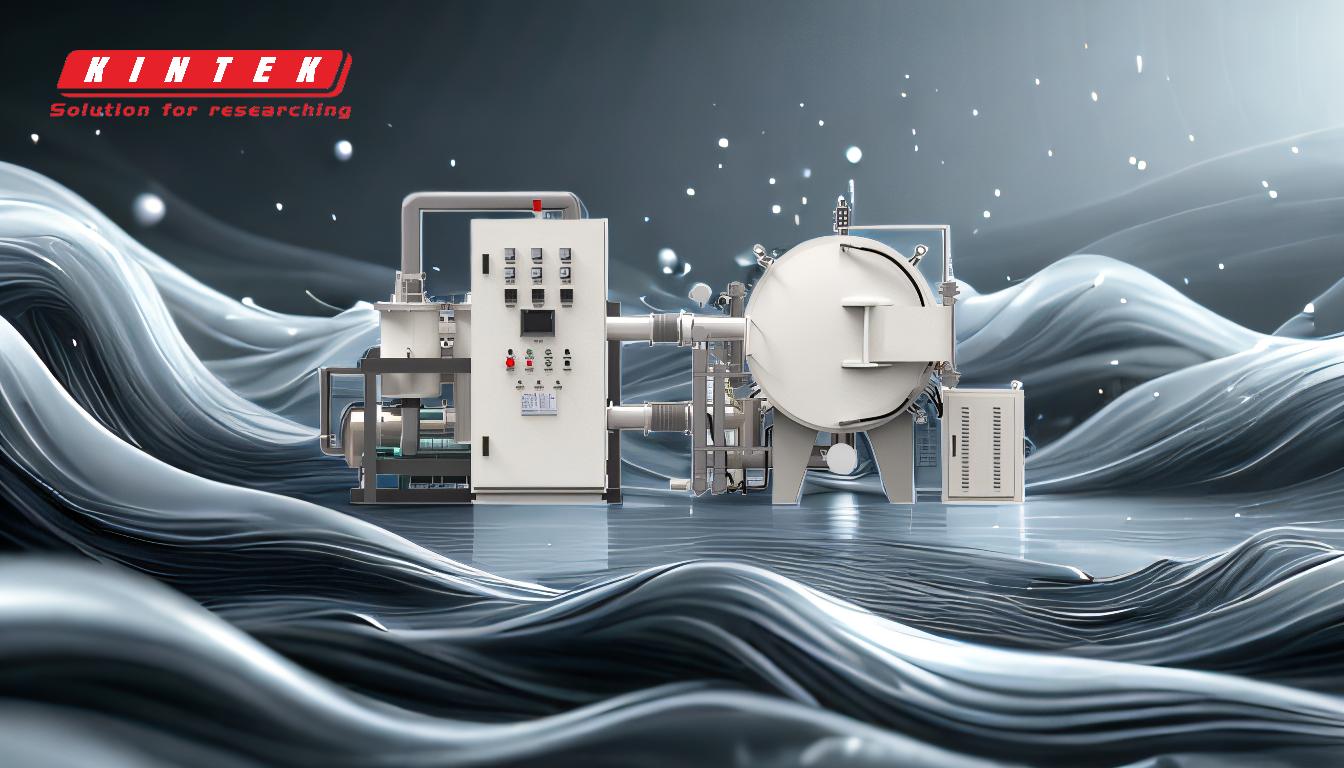
-
High Thermal Resistance:
- Refractory materials are engineered to withstand extremely high temperatures, often exceeding 1,000°C, without melting or degrading.
- This property is critical in industries like steelmaking, glass production, and cement manufacturing, where materials are exposed to intense heat.
- Example: In steelmaking, refractory linings in blast furnaces must endure temperatures up to 1,600°C while maintaining structural integrity.
-
Chemical Stability:
- These materials are resistant to chemical reactions with molten metals, slags, and other corrosive substances.
- This ensures that the refractory lining or structure does not degrade or contaminate the product being processed.
- Example: In glass manufacturing, refractory materials must resist the corrosive effects of molten glass and its additives.
-
Mechanical Strength:
- Refractory materials possess high compressive strength, enabling them to withstand mechanical stress and load-bearing requirements.
- This is particularly important in applications like kilns and reactors, where materials are subjected to pressure and weight.
- Example: In cement kilns, refractory bricks must support the weight of the rotating kiln and the materials inside.
-
Thermal Shock Resistance:
- Refractory materials can endure rapid temperature changes without cracking or breaking.
- This property is crucial in processes where materials are cycled between high and low temperatures.
- Example: In glass furnaces, refractory materials must handle sudden temperature fluctuations during heating and cooling cycles.
-
Abrasion Resistance:
- These materials are designed to resist wear and tear caused by friction or mechanical impact.
- This ensures longevity and reduces the need for frequent replacements.
- Example: In steel ladles, refractory linings must withstand the abrasive action of molten metal and slag.
-
Cost-Effectiveness:
- While refractory materials may have a higher upfront cost, their durability and long service life result in lower maintenance and replacement costs over time.
- This makes them a cost-effective solution for high-temperature industrial applications.
- Example: In aluminum smelting, refractory materials reduce downtime and operational costs by minimizing the need for frequent repairs.
-
Versatility:
- Refractory materials are available in various forms, including bricks, castables, and coatings, making them suitable for diverse applications.
- This adaptability allows for tailored solutions based on specific process requirements.
- Example: In petrochemical plants, refractory materials are used in reactors, boilers, and pipelines, each requiring different forms and compositions.
-
Energy Efficiency:
- Refractory materials often have low thermal conductivity, which helps in retaining heat within the system and improving energy efficiency.
- This reduces energy consumption and operational costs in high-temperature processes.
- Example: In ceramic kilns, refractory linings help maintain consistent temperatures, reducing the need for additional heating.
-
Environmental Benefits:
- By reducing the need for frequent replacements and repairs, refractory materials contribute to lower waste generation and resource consumption.
- Some refractory materials are also recyclable, further enhancing their environmental sustainability.
- Example: Used refractory bricks in steel plants can be recycled or repurposed, minimizing environmental impact.
-
Customizability:
- Refractory materials can be tailored to meet specific application requirements, such as temperature range, chemical exposure, and mechanical stress.
- This ensures optimal performance and longevity in diverse industrial settings.
- Example: In the aerospace industry, refractory materials are customized to withstand the extreme conditions of rocket engines and turbines.
In conclusion, refractory materials offer a combination of thermal, chemical, and mechanical properties that make them indispensable in high-temperature industrial processes. Their advantages, including durability, cost-effectiveness, and versatility, ensure their continued use in industries ranging from metallurgy to energy production.
Summary Table:
Advantage | Description | Example Application |
---|---|---|
High Thermal Resistance | Withstands temperatures >1,000°C without degradation. | Steelmaking blast furnaces (up to 1,600°C). |
Chemical Stability | Resists corrosion from molten metals, slags, and chemicals. | Glass manufacturing (resists molten glass). |
Mechanical Strength | High compressive strength for load-bearing applications. | Cement kilns (supports rotating kiln weight). |
Thermal Shock Resistance | Endures rapid temperature changes without cracking. | Glass furnaces (handles heating/cooling cycles). |
Abrasion Resistance | Resists wear from friction or mechanical impact. | Steel ladles (withstands molten metal and slag). |
Cost-Effectiveness | Durable with lower maintenance and replacement costs over time. | Aluminum smelting (reduces downtime). |
Versatility | Available in bricks, castables, and coatings for diverse applications. | Petrochemical plants (reactors, boilers, pipelines). |
Energy Efficiency | Low thermal conductivity retains heat, reducing energy consumption. | Ceramic kilns (maintains consistent temperatures). |
Environmental Benefits | Reduces waste and resource consumption; some materials are recyclable. | Steel plants (recycled refractory bricks). |
Customizability | Tailored for specific temperature, chemical, and mechanical requirements. | Aerospace (rocket engines and turbines). |
Looking for high-performance refractory materials for your industrial needs? Contact us today to explore tailored solutions!