Cold isostatic pressing (CIP) is a versatile manufacturing process used to produce a wide range of materials and components with uniform density and structural integrity. It involves applying uniform pressure to powders or preforms using a liquid medium, typically at room temperature or slightly elevated temperatures. This method is particularly useful for materials that are difficult to press using conventional techniques, such as hard metals, ceramics, and refractory materials. CIP is widely applied in industries like aerospace, automotive, electronics, and chemical processing, enabling the production of complex shapes, high-density components, and advanced materials like solid-state batteries. Its ability to enhance mechanical properties, such as hardness and wear resistance, makes it a preferred choice for manufacturing high-performance materials.
Key Points Explained:
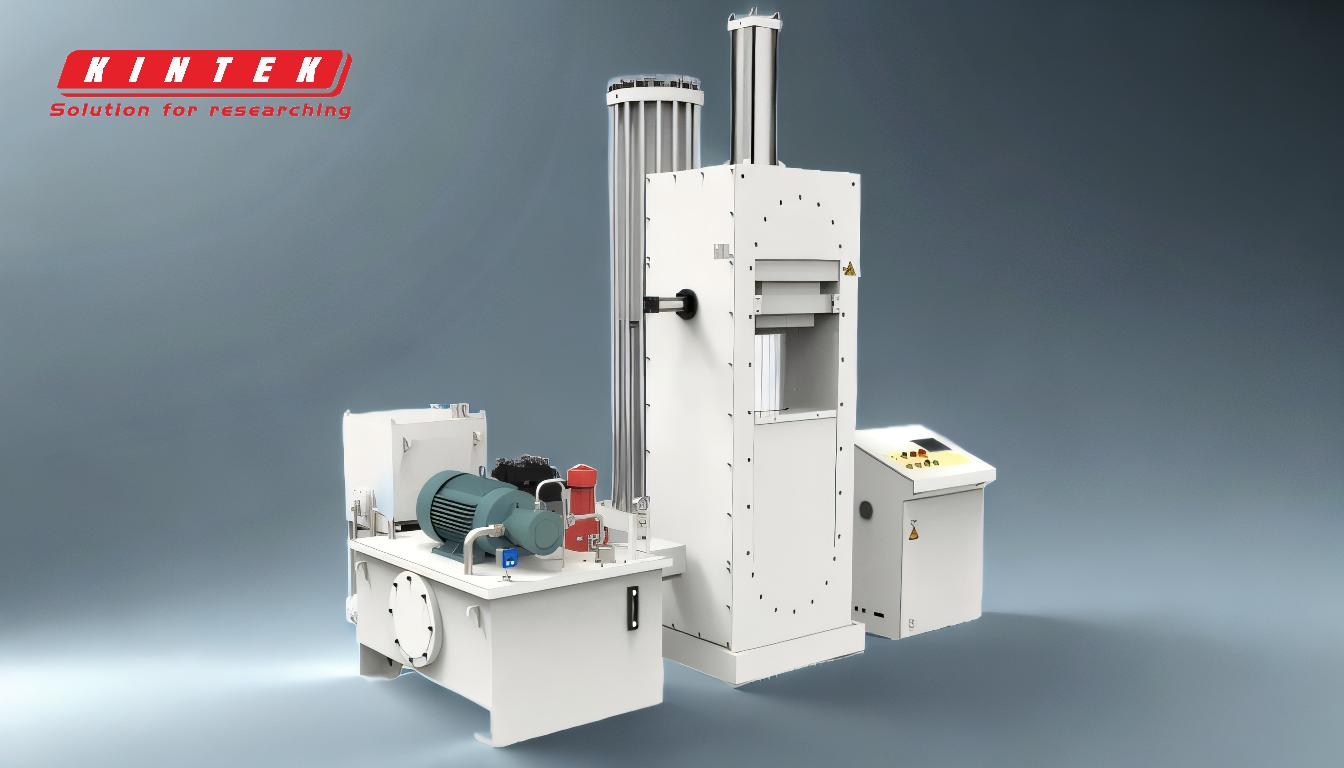
-
Uniform Density and Structural Integrity:
- Cold isostatic pressing applies uniform pressure in all directions, ensuring consistent density throughout the material. This is particularly beneficial for materials like isotropic graphite and ceramics, where uniformity is critical for performance.
- The process minimizes defects such as voids or cracks, which are common in traditional pressing methods, resulting in superior structural integrity.
-
Versatility in Material Processing:
- CIP is suitable for a wide range of materials, including hard metals, ceramics, refractory materials, and cemented carbides. This makes it ideal for producing components like refractory nozzles, crucibles, and ceramic insulators.
- It is also used for creating metal filters, preforms, and plastic tubes, demonstrating its adaptability across industries.
-
Complex and Intricate Shapes:
- Unlike conventional pressing methods, CIP can produce complex and intricate shapes with high precision. This is particularly useful for manufacturing components like tubes for chemical applications or ferrites used in electronics.
- The process enables the creation of thin, dense layers, such as solid electrolyte layers in solid-state batteries, which are difficult to achieve with other techniques.
-
Enhanced Mechanical Properties:
- Components produced through CIP exhibit improved mechanical properties, including hardness, wear resistance, and thermal stability. This is essential for applications in high-stress environments, such as aerospace and automotive industries.
- The process also allows for the integration of multiple layers, such as cathode, solid electrolyte, and anode layers, into dense, tri-layer systems for advanced applications.
-
Room Temperature Processing:
- CIP operates at room temperature or slightly elevated temperatures (<93°C), making it energy-efficient compared to hot isostatic pressing (HIP). This is advantageous for materials that are sensitive to high temperatures.
- The use of a liquid medium, such as water with a corrosion inhibitor, ensures uniform pressure distribution and minimizes contamination.
-
Applications in Advanced Technologies:
- CIP plays a crucial role in the development of solid-state batteries (SSBs) by enabling the production of dense, thin electrolyte layers and integrated multi-layer systems.
- It is also used in the manufacturing of isotropic graphite, which is essential for applications in high-temperature environments, such as muffle furnaces.
-
Economic and Environmental Benefits:
- The ability to produce high-density, high-performance materials with minimal waste makes CIP an environmentally friendly manufacturing process.
- Its efficiency in handling difficult-to-press powders reduces material costs and improves production yields, making it economically viable for large-scale manufacturing.
In summary, cold isostatic pressing is a highly effective and versatile manufacturing process that offers numerous advantages, including uniform density, enhanced mechanical properties, and the ability to produce complex shapes. Its applications span across various industries, from aerospace and electronics to chemical processing and advanced energy storage, making it an indispensable tool in modern manufacturing.
Summary Table:
Key Application Areas | Benefits |
---|---|
Aerospace & Automotive | Enhanced mechanical properties, high-density components |
Electronics | Production of ferrites and solid-state batteries |
Chemical Processing | Complex shapes like tubes and nozzles |
Advanced Energy Storage | Dense electrolyte layers for solid-state batteries |
High-Temperature Environments | Manufacturing of isotropic graphite |
Environmental & Economic | Minimal waste, cost-efficient production |
Discover how cold isostatic pressing can transform your manufacturing process—contact us today for expert guidance!