High-frequency induction heating is a versatile and efficient method used across various industries for applications such as heat treatment, brazing, forging, and surface hardening. It is particularly valued for its precision, speed, and ability to target specific areas without affecting the surrounding material. Key applications include metallurgical processes like hardening and melting, semiconductor manufacturing, and even household uses like induction cooktops. Emerging applications, such as heating low-resistivity materials and biological tissues, highlight its potential for future advancements. This technology is also integral to specialized processes like vacuum furnace operations, plastic injection molding, and tamper-resistant cap sealing, making it indispensable in modern manufacturing and material engineering.
Key Points Explained:
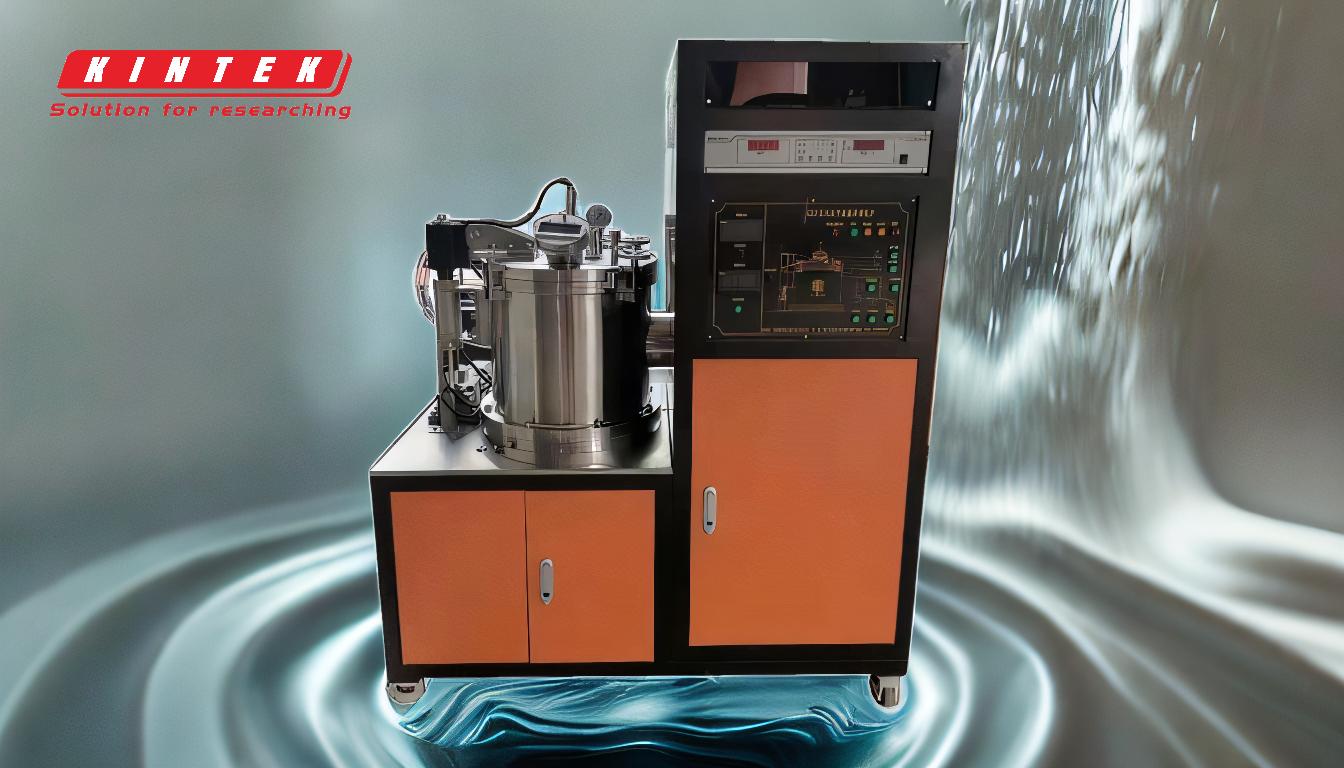
-
Heat Treatment in Metallurgy:
- Induction heating is widely used for surface hardening of steel. The process involves heating the material to a specific temperature using an alternating magnetic field, followed by immediate quenching. This results in a hardened surface layer (case hardnesses of 37/58 Rc) while the core remains unaffected. This method is ideal for components requiring wear resistance without compromising toughness.
-
Brazing and Soldering:
- High-frequency induction heating is commonly used for brazing, particularly in joining carbide tips to shafts or other metal components. The localized heating ensures precise temperature control, minimizing thermal distortion and ensuring strong, durable joints. Soldering applications also benefit from the targeted heating, which is essential in electronics and semiconductor manufacturing.
-
Hot Forging of Small Workpieces:
- Induction heating is ideal for hot forging small-sized workpieces, typically round bars below 15mm in diameter. The rapid and uniform heating reduces energy consumption and improves production efficiency. This is particularly useful in industries requiring high-precision components, such as automotive and aerospace.
-
Quenching Operations:
- Induction heating is used for quenching operations where a thin surface layer (1~2mm) is hardened. This is critical for components like gears, shafts, and bearings, which require a hard surface to resist wear while maintaining a tough core for durability.
-
Melting Refractory Metals:
- Induction heating is capable of reaching extremely high temperatures, making it suitable for melting refractory metals like tungsten, molybdenum, and titanium. These metals are essential in advanced manufacturing and aerospace applications due to their high strength and resistance to heat.
-
Semiconductor Industry Applications:
- In the semiconductor industry, induction heating is used for processes like Czochralski crystal growth and zone refining. These methods are crucial for producing high-purity silicon crystals, which are the foundation of modern electronics.
-
Induction Cooktops:
- Induction heating is employed in household induction cooktops, where it provides rapid and efficient heating. The technology heats the cookware directly through electromagnetic induction, offering precise temperature control and energy efficiency.
-
Specialized Industrial Applications:
- Induction heating is used in vacuum furnaces for producing specialized steels and alloys, welding metals (and sometimes plastics doped with ferromagnetic ceramics), and sealing tamper-resistant caps on bottles and pharmaceuticals. It is also integrated into plastic injection molding machines to improve energy efficiency.
-
Emerging Applications:
- Research is ongoing to expand the use of induction heating to low-resistivity materials and biological tissues for medical purposes. These applications could revolutionize fields like medical device manufacturing and targeted cancer therapies.
-
Future Potential:
- Induction heating is expected to play a significant role in the development of highly engineered materials, alternative energy solutions, and empowering developing countries. Its unique capabilities make it a key technology for advancing manufacturing and material science.
By leveraging its precision, efficiency, and versatility, high-frequency induction heating continues to drive innovation across a wide range of industries, with potential for even broader applications in the future.
Summary Table:
Application | Key Benefits |
---|---|
Heat Treatment in Metallurgy | Surface hardening with precise temperature control and minimal distortion. |
Brazing and Soldering | Strong, durable joints with localized heating for reduced thermal distortion. |
Hot Forging of Small Workpieces | Rapid, uniform heating for energy-efficient production of high-precision parts. |
Quenching Operations | Hardened surface layers (1~2mm) for wear-resistant components like gears. |
Melting Refractory Metals | High-temperature capability for melting tungsten, molybdenum, and titanium. |
Semiconductor Industry | Used in Czochralski crystal growth and zone refining for high-purity silicon. |
Induction Cooktops | Efficient, precise heating for household cooking with energy savings. |
Specialized Industrial Uses | Vacuum furnaces, tamper-resistant cap sealing, and plastic injection molding. |
Emerging Applications | Heating low-resistivity materials and biological tissues for medical advancements. |
Future Potential | Advancing engineered materials, alternative energy, and global manufacturing. |
Unlock the potential of high-frequency induction heating for your industry—contact our experts today!