Sintering is a versatile manufacturing process with applications across various industries, including ceramics, metals, and advanced materials. It is particularly useful for metals with high melting points, as it allows bonding without reaching melting temperatures. Sintering is widely used in powder metallurgy, 3D printing, and the production of ceramics, glass, and refractory metals. It also plays a role in reducing surface porosity, enhancing material properties, and creating custom forms. Additionally, sintering is employed in additive manufacturing and the production of sintered plastic and PE filters, making it a critical process in modern manufacturing and material science.
Key Points Explained:
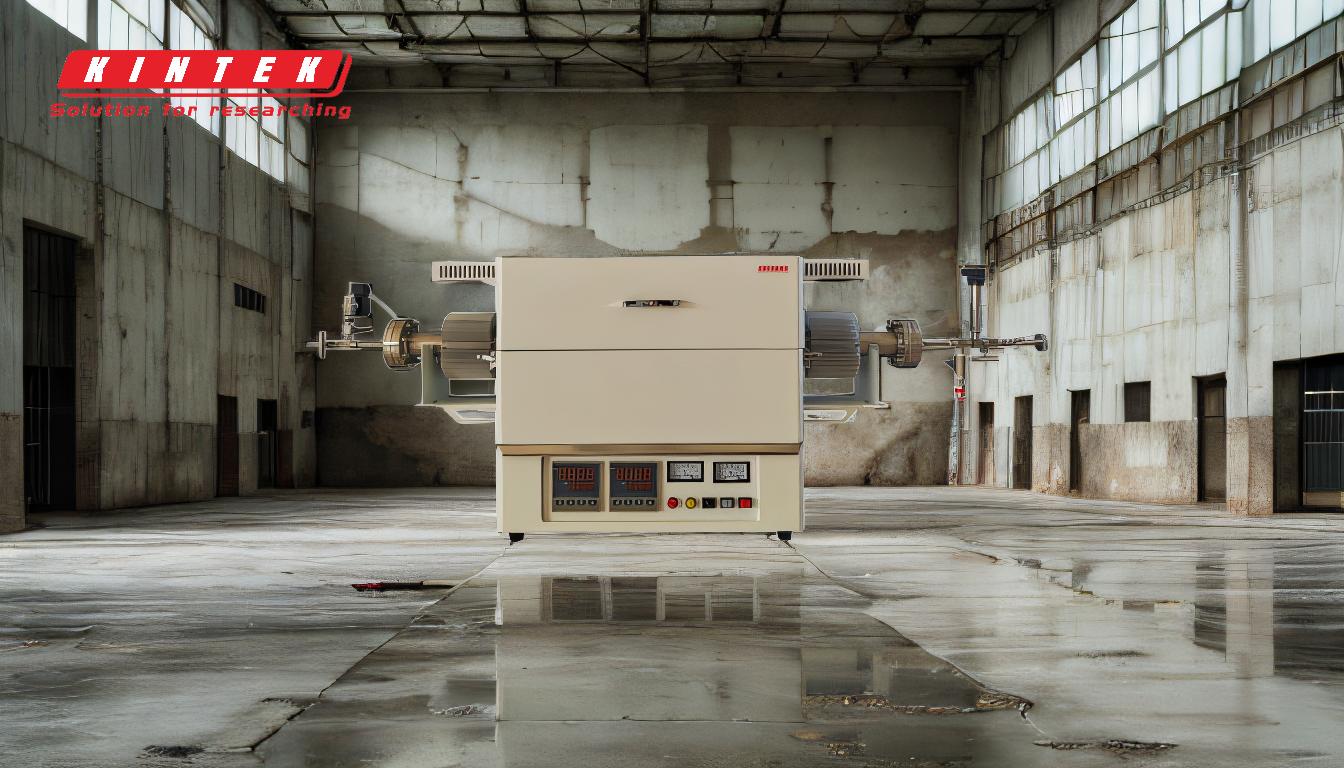
-
Traditional Applications in Ceramics and Powder Metallurgy:
- Sintering has long been used to produce ceramic objects, such as porcelain and glass, by heating powdered materials to bond them without melting.
- In powder metallurgy, sintering is essential for forming metal parts from powdered metals, especially for metals with high melting points like tungsten and molybdenum.
-
Use in 3D Printing and Additive Manufacturing:
- Sintering is a key process in 3D metal printing, where it is used to create custom metal forms layer by layer.
- This method saves energy compared to traditional melting techniques and allows for greater control and consistency in manufacturing complex shapes.
-
Handling High-Melting-Point Metals:
- Sintering is ideal for metals with high melting points, as it binds metal particles together without requiring them to reach their melting temperatures.
- Refractory metals like tungsten and molybdenum are often processed using sintering due to their extreme heat resistance.
-
Reduction of Surface Porosity:
- Sintering can decrease the porosity of a material's surface, improving its mechanical properties, such as strength and durability.
- This is particularly beneficial in applications where material integrity and performance are critical.
-
Production of Advanced Materials:
- Modern sintering techniques are used to produce advanced materials, including sintered plastics and PE filters.
- These materials are used in various industries, such as filtration, automotive, and aerospace, due to their enhanced properties and cost-effectiveness.
-
Energy Efficiency and Customization:
- Sintering is more energy-efficient than melting processes, making it a sustainable choice for manufacturing.
- It also allows for the creation of highly customized and intricate designs, which are difficult to achieve with traditional methods.
-
Applications in Refractory Metal Processing:
- Sintering is critical for forming refractory metals, which are difficult to melt due to their high melting temperatures.
- This makes sintering indispensable in industries that rely on these metals, such as electronics and aerospace.
By leveraging sintering, manufacturers can achieve precise, efficient, and cost-effective production of a wide range of materials and components, making it a cornerstone of modern industrial processes.
Summary Table:
Key Applications | Benefits |
---|---|
Ceramics & Powder Metallurgy | Bonds materials without melting; ideal for high-melting-point metals. |
3D Printing & Additive Manufacturing | Energy-efficient, precise, and customizable metal forms. |
High-Melting-Point Metals | Processes refractory metals like tungsten and molybdenum. |
Surface Porosity Reduction | Enhances strength, durability, and material integrity. |
Advanced Materials Production | Produces sintered plastics, PE filters, and cost-effective industrial materials. |
Energy Efficiency & Customization | Sustainable, intricate designs, and complex shapes. |
Refractory Metal Processing | Essential for electronics, aerospace, and other high-performance industries. |
Unlock the potential of sintering for your manufacturing needs—contact our experts today!