Heat treatment furnaces offer a wide range of benefits that make them indispensable in various industrial processes. These benefits include precise temperature control, energy efficiency, clean processing environments, and enhanced material properties. From improving mechanical properties to ensuring a pollution-free operation, heat treatment furnaces are designed to meet specific industrial needs. The ability to control the furnace atmosphere, achieve rapid temperature changes, and maintain a clean environment are some of the key advantages that make these furnaces highly effective for processes like carburizing, brazing, and vacuum heat treatment. Additionally, they contribute to longer service life, improved efficiency, and cost savings in manufacturing.
Key Points Explained:
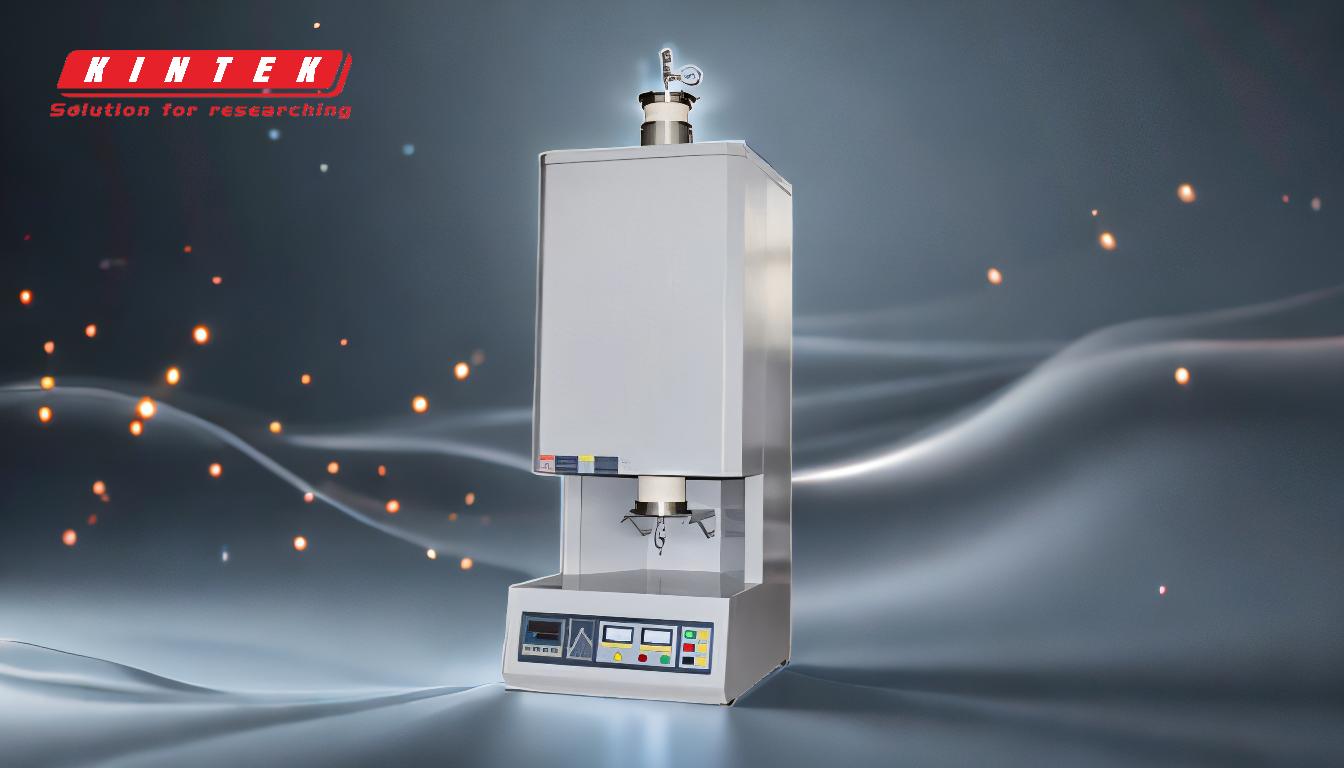
-
Precise Temperature Control and Uniform Heating:
- Heat treatment furnaces provide an equal temperature field, ensuring uniform heating of materials. This is crucial for processes like brazing, where the brazing material must melt without affecting the base material. Uniform heating also prevents defects and ensures consistent material properties.
- The ability to control the furnace atmosphere minimizes undesirable effects such as oxidation or decarburization, which can compromise material integrity.
-
Energy Efficiency and Rapid Temperature Changes:
- Heat treatment furnaces are designed for fast temperature rise and fall, which not only speeds up the process but also saves energy. This is particularly beneficial in high-volume production environments where time and energy efficiency are critical.
- Induction furnaces, for example, are more efficient than traditional melting methods, offering a cleaner and faster melting process.
-
Clean and Pollution-Free Processing:
- Heat treatment furnaces, especially vacuum furnaces, provide a clean environment free from oxidation, decarburization, and contamination. This is essential for achieving high-quality surface finishes and mechanical properties.
- Induction furnaces do not emit pollutants like dust, making them a safer and cleaner option for metal melting.
-
Enhanced Material Properties:
- Processes like carburizing, nitriding, and vacuum heat treatment improve material properties such as hardness, strength, and wear resistance. These processes are facilitated by the precise control offered by heat treatment furnaces.
- Hot Isostatic Pressing (HIP) in furnaces eliminates defects, achieves near-theoretical density, and enhances mechanical properties like strength and reliability.
-
Cost Savings and Improved Efficiency:
- The use of heat treatment furnaces reduces costs by improving product pass rates, minimizing material waste, and extending the service life of components.
- Brazing furnaces, for instance, result in more compact and uniform component combinations, leading to improved heat-exchanging efficiency and longer service life.
-
Versatility in Applications:
- Heat treatment furnaces are versatile and can be used for a wide range of processes, including brazing, carburizing, nitriding, and vacuum heat treatment. This versatility makes them suitable for industries ranging from aerospace to automotive.
- Large vacuum heat treatment furnaces can operate at higher temperatures, speeding up chemical heat treatment processes and achieving faster and better results.
-
Safe and Environmentally Friendly:
- Heat treatment furnaces provide a safe working environment by preventing pollution and eliminating harmful emissions. This is particularly important in industries where worker safety and environmental regulations are stringent.
- The prevention of hydrogen embrittlement and other harmful effects further enhances the safety and reliability of the treated materials.
In summary, heat treatment furnaces offer a combination of precision, efficiency, cleanliness, and versatility that makes them essential for modern industrial processes. Their ability to enhance material properties, reduce costs, and provide a safe working environment underscores their importance in manufacturing and material processing.
Summary Table:
Key Benefits | Details |
---|---|
Precise Temperature Control | Ensures uniform heating and prevents defects, ideal for brazing and more. |
Energy Efficiency | Rapid temperature changes save time and energy in high-volume production. |
Clean Processing Environment | Prevents oxidation, decarburization, and contamination for high-quality results. |
Enhanced Material Properties | Improves hardness, strength, and wear resistance through processes like carburizing. |
Cost Savings | Reduces waste, extends component life, and improves product pass rates. |
Versatility | Suitable for brazing, nitriding, vacuum heat treatment, and more. |
Safe and Eco-Friendly | Eliminates harmful emissions and ensures a pollution-free operation. |
Ready to enhance your industrial processes with a heat treatment furnace? Contact us today to learn more!