Catalysts play a crucial role in the synthesis of carbon nanotubes (CNTs), as they determine the efficiency, quality, and growth rate of the nanotubes. The choice of catalyst, along with the optimization of synthesis conditions such as carbon source concentration and hydrogen presence, significantly impacts the overall process. High concentrations of carbon sources and hydrogen can lead to increased energy consumption but may also enhance growth rates due to the availability of more direct carbon precursors. Balancing these factors is essential for achieving optimal CNT synthesis.
Key Points Explained:
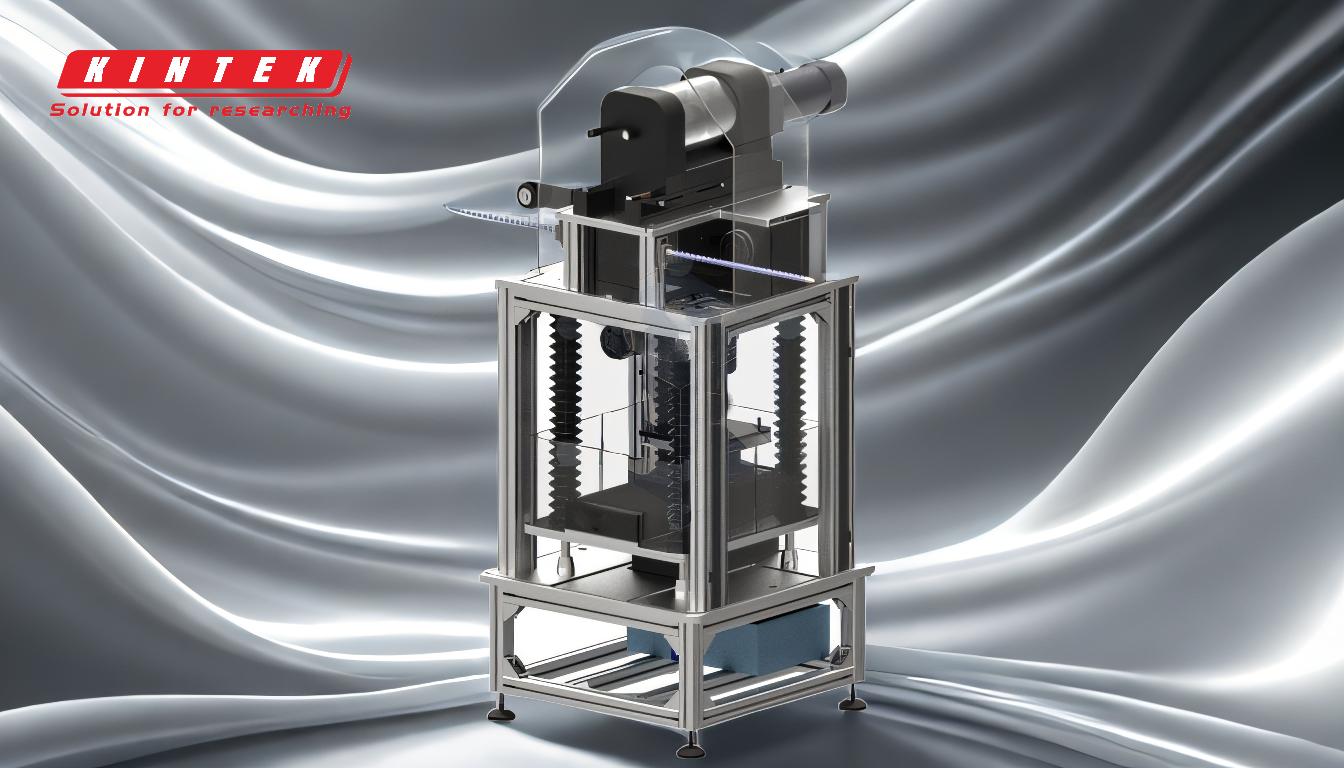
-
Role of Catalysts in CNT Synthesis:
- Catalysts are essential for initiating and sustaining the growth of carbon nanotubes. They provide active sites where carbon atoms can assemble into the tubular structure.
- Common catalysts include transition metals such as iron (Fe), cobalt (Co), nickel (Ni), and their alloys. These metals are chosen for their ability to decompose carbon-containing gases and facilitate the formation of CNTs.
-
Types of Catalysts:
- Metal Catalysts: Transition metals like Fe, Co, and Ni are widely used due to their high catalytic activity and ability to form nanoparticles, which are critical for CNT growth.
- Bimetallic Catalysts: Combinations of metals, such as Fe-Co or Ni-Co, are often used to enhance catalytic performance and control the diameter and structure of the nanotubes.
- Supported Catalysts: Catalysts are often supported on substrates like alumina (Al₂O₃), silica (SiO₂), or magnesium oxide (MgO) to improve dispersion and stability during the synthesis process.
-
Influence of Carbon Source and Hydrogen:
- The concentration of the carbon source (e.g., methane, ethylene, acetylene) directly affects the growth rate of CNTs. Higher concentrations can lead to faster growth but may also result in defects or amorphous carbon deposition.
- Hydrogen plays a dual role: it can act as a reducing agent to maintain the catalytic activity of the metal nanoparticles and also help in etching away amorphous carbon, leading to purer CNTs.
-
Optimization of Synthesis Conditions:
- Temperature: The synthesis temperature must be carefully controlled to ensure the catalyst remains active and the carbon source decomposes efficiently. Typical temperatures range from 600°C to 1000°C.
- Pressure: The pressure of the reaction environment can influence the growth rate and quality of CNTs. Lower pressures are often preferred to minimize unwanted side reactions.
- Gas Flow Rates: The flow rates of the carbon source and hydrogen must be balanced to ensure a steady supply of reactants without overwhelming the catalyst.
-
Trade-offs in Synthesis:
- High concentrations of carbon sources and hydrogen can lead to increased energy consumption due to the need for higher temperatures and longer reaction times.
- However, these conditions can also result in higher growth rates and better-quality CNTs, as they provide more direct carbon precursors and help maintain the catalytic activity of the metal nanoparticles.
-
Challenges and Future Directions:
- One of the main challenges in CNT synthesis is achieving uniform catalyst dispersion, which is crucial for producing CNTs with consistent diameters and lengths.
- Future research is focused on developing more efficient catalysts, such as single-atom catalysts or those with tailored surface properties, to further optimize the synthesis process.
In conclusion, the choice of catalyst and the optimization of synthesis conditions are critical for the efficient production of high-quality carbon nanotubes. Understanding the interplay between catalysts, carbon sources, and hydrogen is essential for achieving the desired balance between growth rate, energy consumption, and CNT quality.
Summary Table:
Aspect | Details |
---|---|
Role of Catalysts | Essential for initiating and sustaining CNT growth by providing active sites. |
Common Catalysts | Transition metals (Fe, Co, Ni) and their alloys. |
Types of Catalysts | - Metal Catalysts (Fe, Co, Ni) |
- Bimetallic Catalysts (Fe-Co, Ni-Co)
- Supported Catalysts (Al₂O₃, SiO₂, MgO) | | Influence of Carbon Source | Higher concentrations increase growth rate but may cause defects. | | Role of Hydrogen | Acts as a reducing agent and etches amorphous carbon for purer CNTs. | | Optimization Factors | Temperature (600°C–1000°C), pressure, and gas flow rates. | | Trade-offs | High carbon/hydrogen levels increase energy use but improve growth rates. | | Challenges | Achieving uniform catalyst dispersion for consistent CNT quality. | | Future Directions | Development of single-atom catalysts and tailored surface properties. |
Ready to optimize your CNT synthesis process? Contact our experts today for tailored solutions!