A forging press is a critical piece of equipment in metalworking, used to shape metal through compressive forces. The components of a forging press vary depending on whether it is a mechanical or hydraulic system. Mechanical forging presses typically consist of a motor, ram, die, anvil, and bailing compartment, while hydraulic forging presses include components such as a safety door, limit switch, manual control valve, relief valve, pressure gauge, hydraulic cylinder, oil tank, and pressing plate. Understanding these components is essential for selecting, operating, and maintaining forging presses effectively.
Key Points Explained:
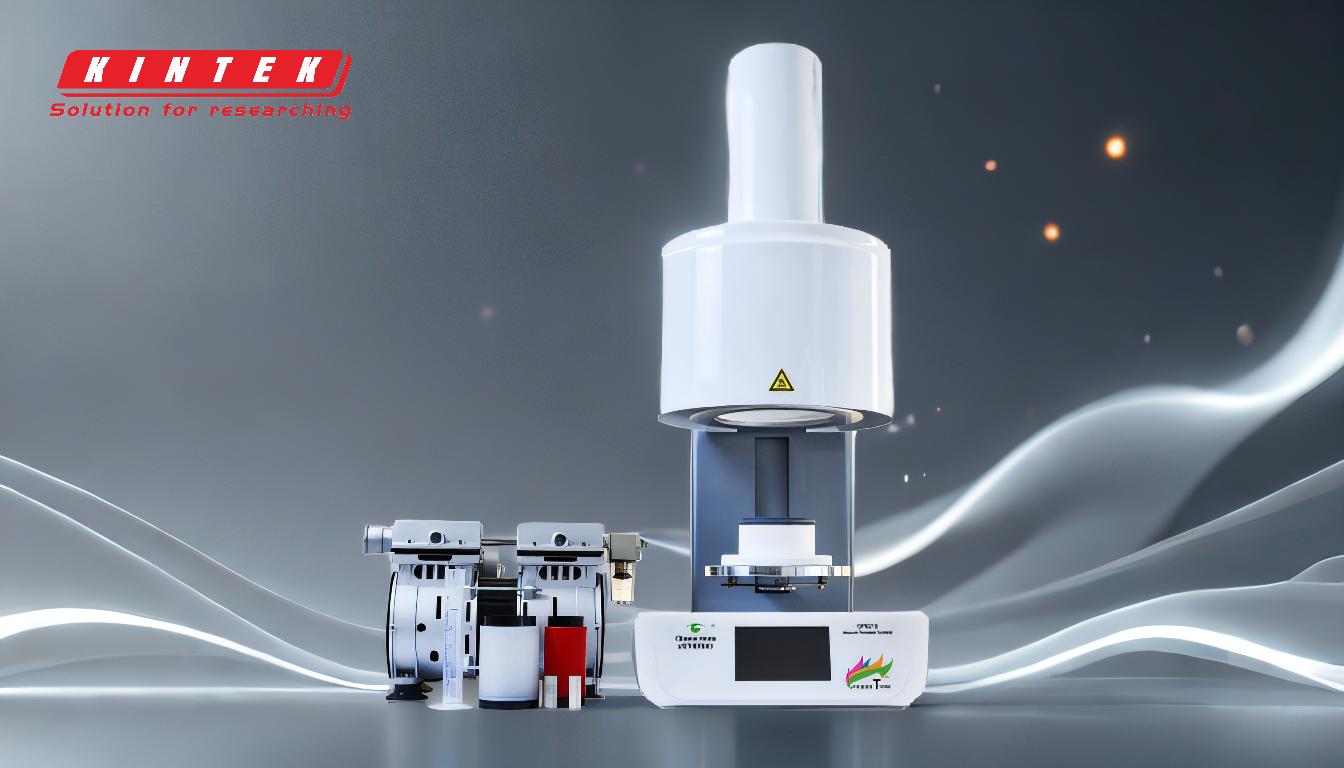
-
Motor:
- The motor is the power source for mechanical forging presses. It drives the ram, which applies the necessary force to shape the metal. The motor's power and efficiency are critical for the performance of the press.
-
Ram:
- The ram is the moving component that delivers the force to the workpiece. In mechanical presses, the ram is driven by the motor and moves in a controlled manner to compress the metal between the dies.
-
Die:
- The die is the tooling that shapes the metal. It is typically made of hardened steel and is designed to withstand the high pressures and temperatures involved in forging. The die's design and quality directly impact the final product's accuracy and surface finish.
-
Anvil:
- The anvil is the stationary component that supports the workpiece during forging. It provides a stable surface against which the ram presses the metal. The anvil must be robust and durable to handle the repetitive impacts and pressures.
-
Bailing Compartment:
- The bailing compartment is a feature in some mechanical forging presses that helps in ejecting the finished part from the die. It ensures smooth operation and reduces downtime between forging cycles.
-
Safety Door:
- In hydraulic forging presses, the safety door is a protective barrier that prevents access to the working area during operation. It enhances operator safety by minimizing the risk of injury from moving parts or ejected material.
-
Limit Switch:
- The limit switch is a safety and control component that stops the press when the ram reaches a predetermined position. It ensures precise control over the forging process and prevents over-travel, which could damage the press or the workpiece.
-
Manual Control Valve:
- The manual control valve allows operators to adjust the flow of hydraulic fluid, controlling the speed and force of the ram. It provides flexibility in operation, enabling adjustments based on the specific requirements of the forging process.
-
Relief Valve:
- The relief valve is a safety device that protects the hydraulic system from excessive pressure. It opens to release fluid when the pressure exceeds a set limit, preventing damage to the press and ensuring safe operation.
-
Pressure Gauge:
- The pressure gauge monitors the hydraulic system's pressure, providing real-time feedback to the operator. Accurate pressure measurement is crucial for maintaining consistent forging quality and preventing system overload.
-
Hydraulic Cylinder:
- The hydraulic cylinder is the main actuator in hydraulic forging presses. It converts hydraulic energy into mechanical force, driving the ram to compress the metal. The cylinder's size and capacity determine the press's maximum force output.
-
Oil Tank:
- The oil tank stores the hydraulic fluid used in the press. It must be designed to maintain the fluid's temperature and cleanliness, ensuring efficient and reliable operation of the hydraulic system.
-
Pressing Plate:
- The pressing plate is the component that directly contacts the workpiece during forging. It must be durable and precisely machined to ensure uniform pressure distribution and high-quality forging results.
Understanding these components and their functions is essential for anyone involved in the selection, operation, or maintenance of forging presses. Each component plays a vital role in ensuring the press's performance, safety, and longevity.
Summary Table:
Component | Function | Type |
---|---|---|
Motor | Powers the ram in mechanical presses. | Mechanical |
Ram | Applies force to shape metal. | Mechanical |
Die | Shapes metal under high pressure. | Both |
Anvil | Supports the workpiece during forging. | Mechanical |
Bailing Compartment | Ejects finished parts from the die. | Mechanical |
Safety Door | Protects operators from moving parts. | Hydraulic |
Limit Switch | Stops the press at a predetermined position. | Hydraulic |
Manual Control Valve | Adjusts hydraulic fluid flow for ram speed and force. | Hydraulic |
Relief Valve | Releases excess pressure to protect the system. | Hydraulic |
Pressure Gauge | Monitors hydraulic pressure for consistent forging. | Hydraulic |
Hydraulic Cylinder | Converts hydraulic energy into mechanical force. | Hydraulic |
Oil Tank | Stores and maintains hydraulic fluid. | Hydraulic |
Pressing Plate | Directly contacts the workpiece for uniform pressure. | Hydraulic |
Ready to optimize your metalworking process? Contact us today to learn more about forging presses!