Induction heating, while efficient and clean, has several disadvantages that can impact its practicality and cost-effectiveness. These include high initial investment costs, the need for skilled personnel, limited refining capacity, and challenges related to heat distribution and material compatibility. Additionally, the requirement for specialized equipment and inductors can further complicate its application in certain scenarios. Below, we explore these drawbacks in detail to provide a comprehensive understanding of the limitations of induction heating.
Key Points Explained:
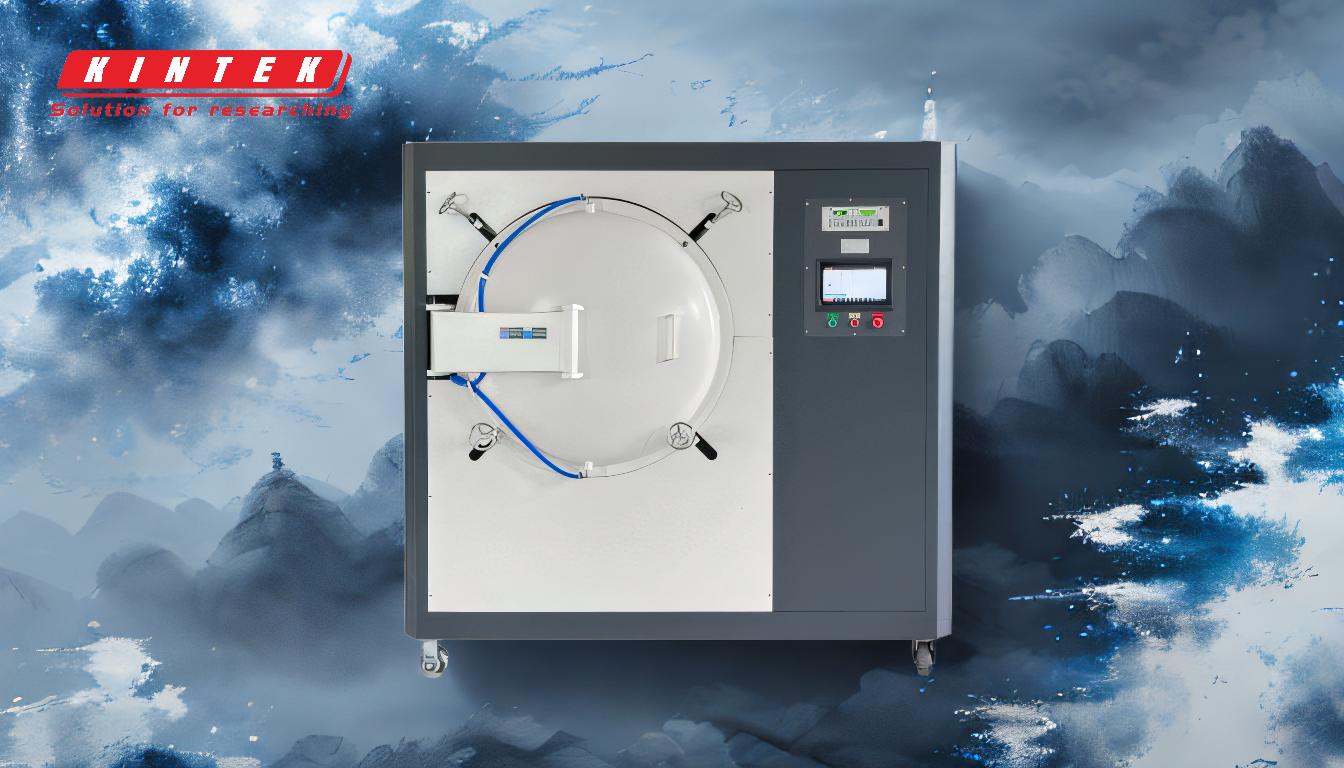
-
High Initial Investment Costs:
- Induction heating systems require significant upfront investment, including the cost of high-frequency generators, specialized power supplies, and other equipment.
- The need for dedicated inductors tailored to specific applications adds to the expense, as these components must be custom-designed and manufactured.
- This financial barrier can make induction heating less accessible for smaller operations or businesses with limited budgets.
-
Dependence on Skilled Personnel:
- Operating induction heating systems demands expertise in induction heating principles, safety protocols, and equipment maintenance.
- Skilled personnel are essential to ensure proper alignment, optimal inductive coupling, and efficient heat distribution.
- The reliance on specialized knowledge can increase labor costs and limit the scalability of induction heating in industries with a shortage of trained professionals.
-
Limited Refining Capacity:
- Induction furnaces lack refining capabilities, meaning charge materials must be free of oxides and of a known composition before heating.
- This limitation requires strict control over raw material purity, which can increase material costs and complicate the supply chain.
- Some alloying elements may be lost due to oxidation during the heating process, necessitating their re-addition to the melt and further increasing costs.
-
Challenges with Heat Distribution:
- Induction heating is most effective for surface heating, which can lead to uneven heat distribution in larger or more complex parts.
- High heating rates can exacerbate this issue, causing thermal stress and potential damage to the material.
- Achieving uniform heat distribution often requires precise control and optimization of the heating process, which can be technically challenging.
-
Material Compatibility Issues:
- The effectiveness of induction heating depends on the thermal conductivity and inductive coupling properties of the material being heated.
- Materials with poor thermal conductivity or low magnetic permeability may not heat efficiently, limiting the applicability of induction heating in certain scenarios.
- Refractory linings in induction furnaces can also pose reliability and safety concerns, as issues with these linings can affect furnace performance and longevity.
-
Specialized Engineering Requirements:
- Managing high-current densities in small copper inductors often requires specialized engineering and "copper-fitting," which can be complex and costly.
- The need for custom inductors for specific applications reduces the flexibility of induction heating and increases both design and production costs.
- These engineering challenges can make induction heating less practical for applications requiring frequent changes in heating configurations.
-
Energy Efficiency Concerns:
- While induction heating is generally energy-efficient, the high-frequency generators and power supplies required can consume significant amounts of electricity.
- Inefficiencies in the system, such as poor inductive coupling or suboptimal alignment, can further reduce energy efficiency and increase operational costs.
By understanding these disadvantages, potential users of induction heating can make informed decisions about whether this technology aligns with their specific needs and constraints. While induction heating offers many advantages, its limitations must be carefully considered to ensure successful implementation.
Summary Table:
Disadvantage | Key Details |
---|---|
High Initial Investment Costs | Requires expensive equipment, custom inductors, and significant upfront costs. |
Dependence on Skilled Personnel | Demands expertise in operation, maintenance, and safety protocols. |
Limited Refining Capacity | Materials must be pre-refined; alloying elements may be lost during heating. |
Heat Distribution Challenges | Uneven heating in complex parts; thermal stress risks. |
Material Compatibility Issues | Ineffective for materials with poor thermal conductivity or low permeability. |
Specialized Engineering Needs | Custom inductors and high-current density management increase complexity. |
Energy Efficiency Concerns | High electricity consumption and potential inefficiencies in the system. |
Need help deciding if induction heating is right for your needs? Contact our experts today for personalized advice!