PVD (Physical Vapor Deposition) coating is a widely used technique for applying thin films to surfaces, offering benefits such as high hardness, wear resistance, and lower process temperatures. However, it also comes with several disadvantages that can impact its suitability for certain applications. These drawbacks include high costs due to specialized equipment and vacuum requirements, limitations in coating complex geometries, low deposition rates, and being a "line of sight" process that restricts its use for non-visible surfaces. Additionally, the process can be time-consuming and requires careful temperature control and cooling systems to prevent damage to components.
Key Points Explained:
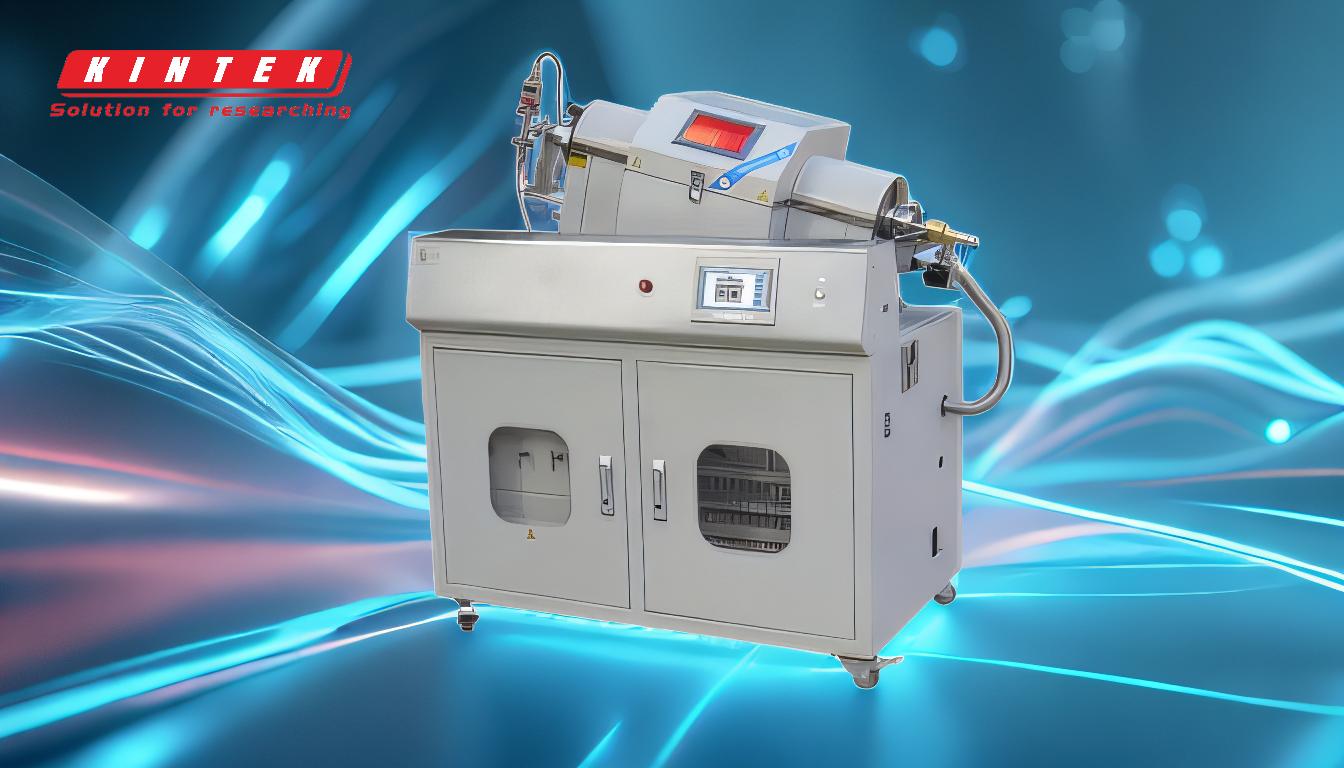
-
High Cost of Equipment and Operation
- PVD coating requires specialized equipment, including large vacuum chambers and cooling systems, which can be expensive to purchase and maintain.
- The process involves intense heating and cooling cycles, increasing operational costs.
- The need for high expertise and precision in handling the equipment further adds to the overall expense.
-
Line of Sight Limitation
- PVD is a "line of sight" process, meaning it can only coat surfaces directly exposed to the vapor stream.
- This limitation makes it unsuitable for coating complex geometries or non-visible surfaces, such as internal cavities or intricate designs.
-
Low Deposition Rate and Throughput
- The deposition rate of PVD is relatively slow, typically ranging from 1-2 Å/s, which can lead to longer processing times.
- The process is not easily scalable, resulting in lower throughput compared to other coating methods.
- This makes PVD less efficient for high-volume production.
-
Complexity and Time-Consuming Nature
- PVD is one of the most complex deposition methods, requiring precise control of vacuum conditions, temperature, and cooling systems.
- The process is slower compared to other techniques, which can delay production timelines.
-
Challenges with Complex Geometries
- While advancements have been made to address this issue, PVD still struggles with uniformly coating parts with complex shapes.
- Specialized methods and equipment may be required to achieve consistent coatings on intricate designs, adding to the complexity and cost.
-
Material Wastage and Color Distortion
- PVD can aggressively alter or destroy colors, leading to material wastage and potential aesthetic issues.
- This drawback may limit its use in applications where color preservation is critical.
-
High Stress and Thermal Management
- PVD coatings can produce high stress during the deposition process, which may affect the durability of the coating.
- Proper cooling systems are essential to dissipate heat and prevent damage to both the coating and the substrate.
-
Limited Suitability for Certain Applications
- Despite its advantages, PVD may not be the best choice for all applications, particularly those requiring rapid production, complex geometries, or non-line-of-sight coating.
In summary, while PVD coating offers significant benefits such as high hardness, wear resistance, and lower process temperatures, its drawbacks—including high costs, line-of-sight limitations, low deposition rates, and challenges with complex geometries—must be carefully considered when selecting a coating method for specific applications.
Summary Table:
Disadvantages of PVD Coating | Details |
---|---|
High Cost of Equipment | Specialized equipment, vacuum chambers, and cooling systems increase costs. |
Line of Sight Limitation | Cannot coat non-visible surfaces or complex geometries effectively. |
Low Deposition Rate | Slow deposition rates (1-2 Å/s) reduce throughput and efficiency. |
Complexity and Time-Consuming | Requires precise control of vacuum, temperature, and cooling systems. |
Challenges with Complex Shapes | Uniform coating on intricate designs is difficult and costly. |
Material Wastage | May alter or destroy colors, leading to aesthetic and material issues. |
High Stress and Thermal Issues | Requires effective cooling systems to manage heat and stress. |
Limited Suitability | Not ideal for rapid production or non-line-of-sight applications. |
Need help deciding if PVD coating is right for your project? Contact our experts today for personalized advice!