Annealing is a critical heat treatment process used to alter the physical and mechanical properties of metals, primarily to increase ductility, reduce hardness, and eliminate internal stresses. The process involves heating the metal to a specific temperature, holding it at that temperature for a period, and then cooling it in a controlled manner. Different annealing techniques are employed depending on the desired outcome, the type of metal, and the application. These techniques include Full Annealing, Process Annealing, Isothermal Annealing, Spheroidizing, and others like Black Annealing, Blue Annealing, and Bright Annealing. Each method has unique characteristics and is chosen based on the specific requirements of the material and its intended use.
Key Points Explained:
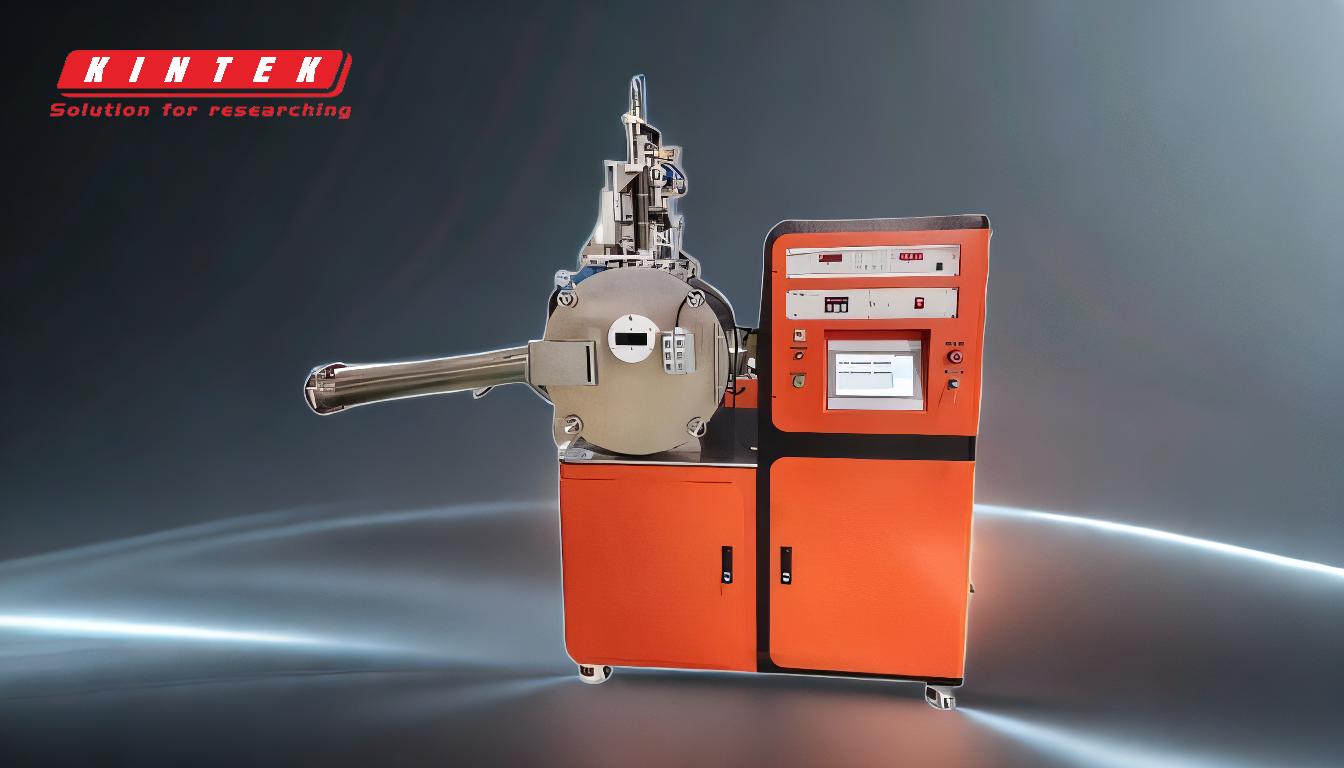
-
Full Annealing:
- Process: The metal is heated to a temperature above its upper critical temperature, held there to allow complete austenitization, and then slowly cooled in the furnace.
- Purpose: This technique is used to produce a coarse pearlitic microstructure, which increases ductility and reduces hardness. It is ideal for improving machinability and workability.
- Applications: Commonly used for steels, especially low-carbon and medium-carbon steels, to prepare them for further processing like machining or forming.
-
Process Annealing:
- Process: The metal is heated to a temperature below the lower critical temperature (typically 550°C to 650°C) and then cooled in air.
- Purpose: This method is used to relieve internal stresses in cold-worked metals without significantly altering their microstructure. It restores ductility and reduces hardness.
- Applications: Often used in the manufacturing of wires, sheets, and tubes where cold working has caused excessive hardening.
-
Isothermal Annealing:
- Process: The metal is heated to a temperature above the upper critical temperature, held for a short period, and then rapidly cooled to a specific temperature below the lower critical temperature. It is held at this temperature until the transformation to pearlite is complete.
- Purpose: This method ensures a uniform microstructure and is faster than full annealing.
- Applications: Suitable for alloy steels and high-carbon steels where precise control over microstructure is required.
-
Spheroidizing:
- Process: The metal is heated to a temperature just below the lower critical temperature and held for an extended period, or cycled between temperatures slightly above and below the lower critical temperature.
- Purpose: This technique produces a spheroidal or globular form of cementite in the microstructure, which improves machinability and reduces hardness.
- Applications: Typically used for high-carbon steels and tool steels to prepare them for machining or cold working.
-
Black Annealing:
- Process: The metal is annealed in a reducing atmosphere or in the presence of a carbon-rich environment, which results in a black oxide layer on the surface.
- Purpose: This method is used to improve surface properties and prevent oxidation during the annealing process.
- Applications: Commonly used for steel sheets and strips in applications where surface finish is not critical.
-
Blue Annealing:
- Process: The metal is heated in an oxidizing atmosphere, which forms a blue oxide layer on the surface.
- Purpose: This technique is used to improve corrosion resistance and surface hardness.
- Applications: Often used for stainless steel and other corrosion-resistant alloys.
-
Bright Annealing:
- Process: The metal is annealed in a controlled atmosphere (e.g., hydrogen or vacuum) to prevent oxidation, resulting in a bright, oxide-free surface.
- Purpose: This method is used to maintain a clean, bright surface finish while achieving the desired mechanical properties.
- Applications: Commonly used for stainless steel, titanium, and other metals where surface appearance is critical.
-
Cycle Annealing:
- Process: The metal is subjected to repeated heating and cooling cycles within a specific temperature range.
- Purpose: This technique is used to refine the grain structure and improve uniformity in the material.
- Applications: Suitable for materials that require a fine-grained microstructure, such as certain alloys and tool steels.
-
Quench Annealing:
- Process: The metal is heated to a high temperature and then rapidly quenched in water, oil, or air.
- Purpose: This method is used to achieve a fine-grained microstructure and improve toughness.
- Applications: Often used for stainless steels and other alloys that require a combination of strength and toughness.
-
Graphitizing:
- Process: The metal is heated to a high temperature and held for a prolonged period to promote the formation of graphite in the microstructure.
- Purpose: This technique is used to improve machinability and reduce brittleness in cast iron.
- Applications: Primarily used for cast iron components in automotive and machinery industries.
Each annealing technique serves a specific purpose and is selected based on the material properties required for the final application. Understanding these methods allows for better decision-making in material selection and processing, ensuring optimal performance and longevity of the components.
Summary Table:
Annealing Technique | Process | Purpose | Applications |
---|---|---|---|
Full Annealing | Heated above upper critical temp, slow cooling | Increase ductility, reduce hardness | Low/medium-carbon steels |
Process Annealing | Heated below lower critical temp, air cooling | Relieve internal stresses | Wires, sheets, tubes |
Isothermal Annealing | Rapid cooling to specific temp, held for transformation | Uniform microstructure | Alloy/high-carbon steels |
Spheroidizing | Heated below lower critical temp, held or cycled | Improve machinability | High-carbon/tool steels |
Black Annealing | Annealed in reducing atmosphere | Prevent oxidation, improve surface | Steel sheets, strips |
Blue Annealing | Heated in oxidizing atmosphere | Improve corrosion resistance | Stainless steel, alloys |
Bright Annealing | Annealed in controlled atmosphere | Maintain bright surface | Stainless steel, titanium |
Cycle Annealing | Repeated heating/cooling cycles | Refine grain structure | Alloys, tool steels |
Quench Annealing | Rapid quenching after heating | Improve toughness | Stainless steels, alloys |
Graphitizing | Prolonged heating for graphite formation | Improve machinability | Cast iron components |
Optimize your metal properties with the right annealing technique—contact our experts today!