Annealing in semiconductors is a critical thermal process used to modify the material's properties, such as reducing defects, improving electrical characteristics, and enhancing structural integrity. Unlike metal annealing, which primarily focuses on stress relief and ductility, semiconductor annealing is tailored to address the unique requirements of semiconductor materials, such as silicon wafers. The process involves heating the material to a specific temperature and then cooling it under controlled conditions. This thermal treatment can be categorized into several types, each serving distinct purposes in semiconductor manufacturing.
Key Points Explained:
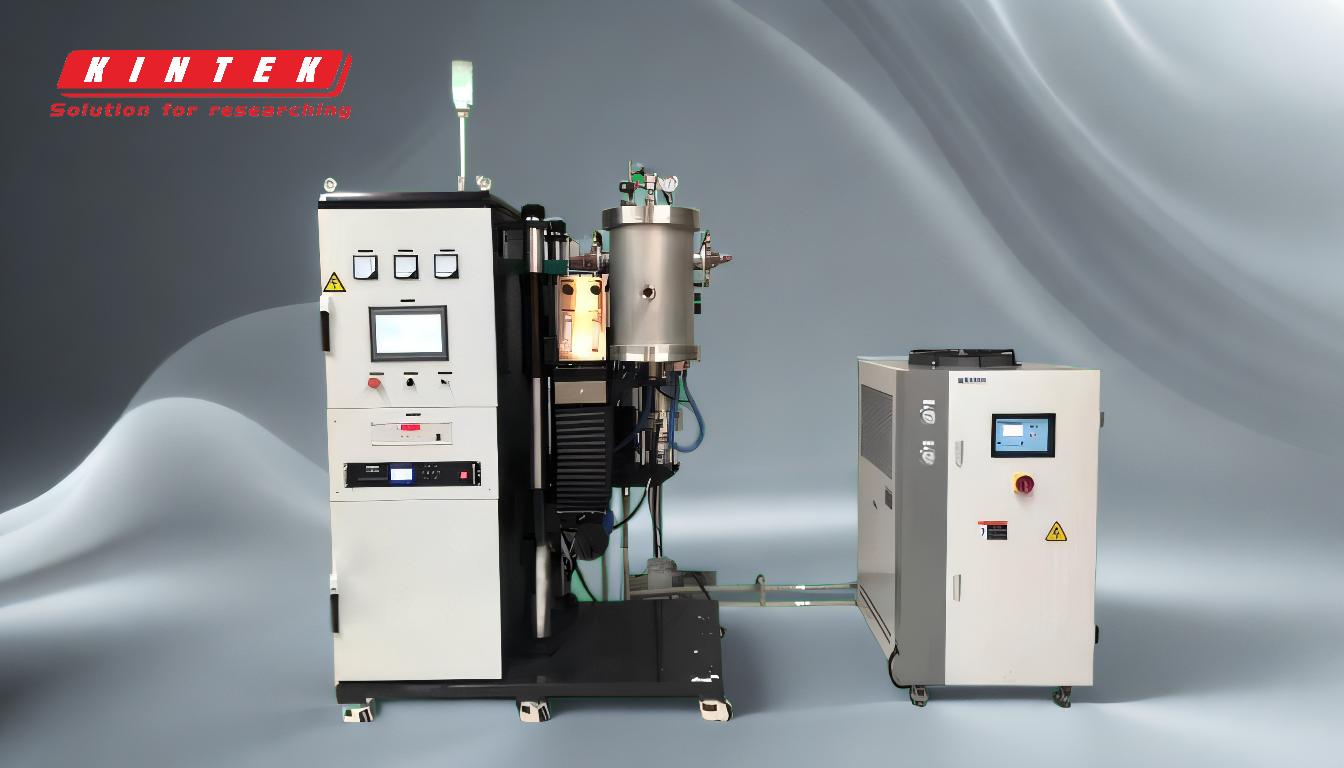
-
Purpose of Annealing in Semiconductors:
- Defect Reduction: Annealing helps reduce defects in the crystal lattice, such as vacancies and dislocations, which can negatively impact the performance of semiconductor devices.
- Dopant Activation: In semiconductor manufacturing, dopants are introduced to modify electrical properties. Annealing activates these dopants by incorporating them into the crystal lattice.
- Stress Relief: Similar to metal annealing, semiconductor annealing can relieve internal stresses that arise during fabrication processes like deposition or etching.
- Recrystallization: Annealing can promote recrystallization, which improves the material's structural integrity and electrical properties.
-
Types of Annealing in Semiconductors:
-
Furnace Annealing:
- Process: The semiconductor wafer is heated in a furnace at temperatures typically ranging from 600°C to 1200°C for several minutes to hours.
- Applications: Used for bulk processing, such as dopant activation and defect annealing. It is suitable for large-scale production due to its ability to handle multiple wafers simultaneously.
- Advantages: Uniform heating and long processing times allow for thorough defect reduction and dopant activation.
- Limitations: Longer processing times can lead to unwanted diffusion of dopants, affecting device performance.
-
Rapid Thermal Annealing (RTA):
- Process: The wafer is heated to high temperatures (up to 1200°C) for a very short duration, typically a few seconds, using intense light sources like halogen lamps.
- Applications: Ideal for processes requiring precise control over temperature and time, such as shallow junction formation in advanced semiconductor devices.
- Advantages: Minimizes dopant diffusion, making it suitable for modern devices with smaller feature sizes.
- Limitations: Requires sophisticated equipment and precise control to avoid thermal stress and damage to the wafer.
-
Laser Annealing:
- Process: A high-energy laser beam is used to heat the surface of the wafer to extremely high temperatures for a very short time (nanoseconds to milliseconds).
- Applications: Used for localized annealing, such as repairing defects in specific areas or activating dopants in small regions.
- Advantages: Highly precise and localized heating, minimizing thermal impact on surrounding areas.
- Limitations: Limited to surface treatments and requires advanced laser systems.
-
Flash Lamp Annealing:
- Process: Intense light from a flash lamp is used to heat the wafer surface rapidly, similar to RTA but with even shorter durations (milliseconds).
- Applications: Suitable for ultra-shallow junction formation and surface defect repair.
- Advantages: Extremely fast processing, reducing the risk of dopant diffusion.
- Limitations: Limited to surface treatments and requires specialized equipment.
-
-
Comparison of Annealing Techniques:
- Temperature and Time: Furnace annealing operates at lower temperatures for longer durations, while RTA, laser annealing, and flash lamp annealing involve higher temperatures for shorter times.
- Precision and Localization: Laser and flash lamp annealing offer higher precision and localization compared to furnace annealing and RTA.
- Equipment Complexity: Furnace annealing is relatively simple, while RTA, laser annealing, and flash lamp annealing require more advanced and expensive equipment.
-
Applications in Semiconductor Manufacturing:
- Dopant Activation: All annealing techniques are used to activate dopants, but the choice depends on the device's requirements and feature size.
- Defect Repair: Laser and flash lamp annealing are particularly useful for repairing defects in specific areas without affecting the entire wafer.
- Stress Relief: Furnace annealing is commonly used for stress relief in bulk processing, while RTA is preferred for stress relief in advanced devices.
-
Future Trends in Semiconductor Annealing:
- Advanced Materials: As semiconductor materials evolve, annealing techniques will need to adapt to handle new materials like gallium nitride (GaN) and silicon carbide (SiC).
- 3D Devices: With the rise of 3D semiconductor devices, annealing techniques will need to address challenges related to heat distribution and stress management in complex structures.
- Energy Efficiency: Future annealing processes may focus on reducing energy consumption while maintaining or improving performance.
In summary, annealing in semiconductors is a versatile and essential process that plays a crucial role in device performance and reliability. The choice of annealing technique depends on the specific requirements of the semiconductor device, such as feature size, material properties, and desired electrical characteristics. As semiconductor technology continues to advance, annealing processes will evolve to meet the demands of next-generation devices.
Summary Table:
Type | Process | Applications | Advantages | Limitations |
---|---|---|---|---|
Furnace Annealing | Heated at 600°C–1200°C for minutes to hours | Bulk processing, dopant activation, defect annealing | Uniform heating, thorough defect reduction | Longer processing times may cause dopant diffusion |
Rapid Thermal (RTA) | Heated to 1200°C for seconds using halogen lamps | Shallow junction formation, advanced devices | Minimizes dopant diffusion, precise control | Requires sophisticated equipment, risk of thermal stress |
Laser Annealing | High-energy laser heats surface for nanoseconds to milliseconds | Localized defect repair, dopant activation | Highly precise, minimal thermal impact on surrounding areas | Limited to surface treatments, requires advanced laser systems |
Flash Lamp Annealing | Intense light heats surface rapidly (milliseconds) | Ultra-shallow junction formation, surface defect repair | Extremely fast processing, reduces dopant diffusion | Limited to surface treatments, requires specialized equipment |
Discover the best annealing technique for your semiconductor needs—contact our experts today!