Batch furnaces are essential in industrial and laboratory settings for processes like heat treatment, annealing, and curing. Among the various types, box furnaces stand out due to their versatility, simple design, and ability to handle a wide range of temperatures and applications. Other types include elevator furnaces, chamber and muffle furnaces, tube furnaces, and high-temperature chamber furnaces. Each type has unique structural characteristics, heating elements, and temperature capabilities, making them suitable for specific industrial or laboratory needs.
Key Points Explained:
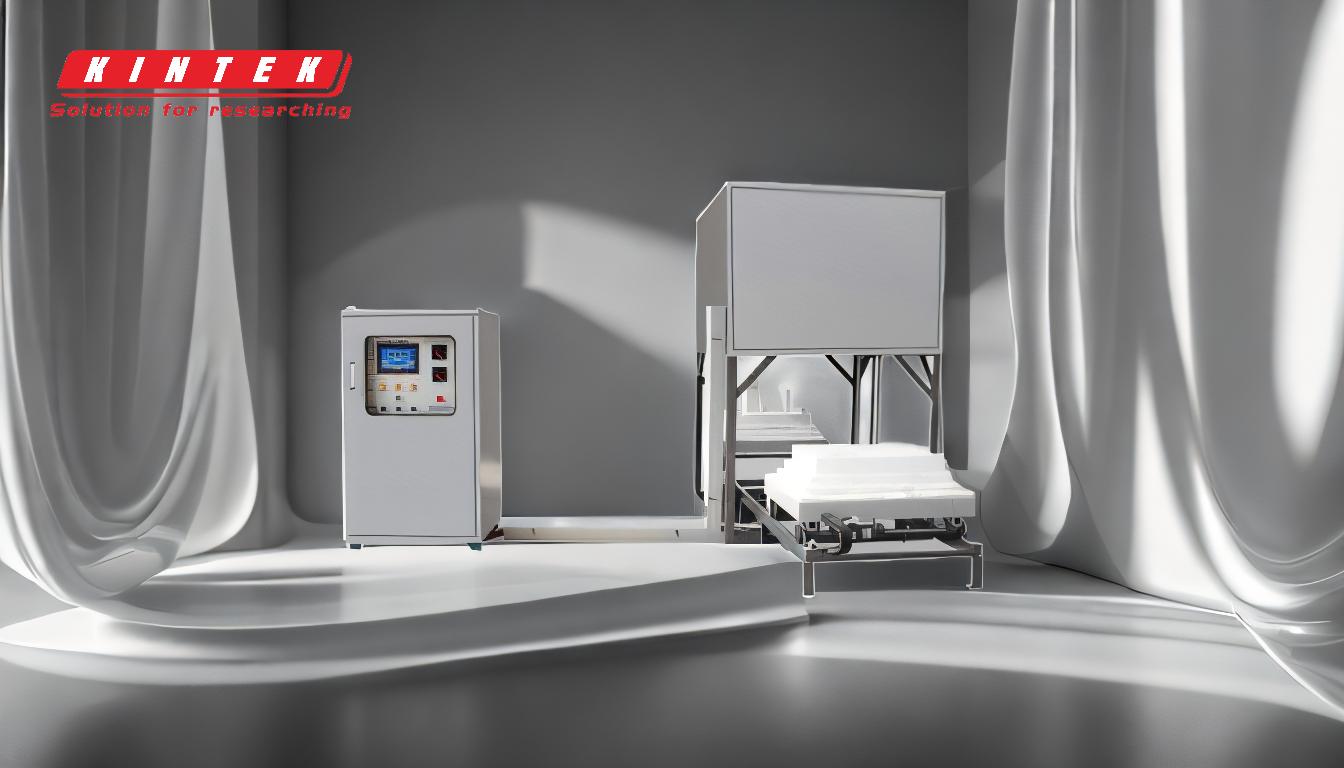
-
Box Furnaces
- Design and Functionality: Box furnaces are batch-operating furnaces with a simple yet robust design. They are front-loaded or forklift-loaded, making them versatile for various applications. The furnace can have single or multiple door systems that open vertically or horizontally, depending on the model.
- Temperature Range: These furnaces can achieve temperatures between 1800 °F and 3100 °F (1000 °C and 1700 °C), making them suitable for high-temperature processes.
- Applications: Commonly used for heat treatment, calcining, curing, annealing, stress relieving, preheating, and tempering. Their versatility makes them a popular choice in both industrial and laboratory settings.
- Configurations: Available in various sizes, from compact tabletop models to large, heavy-duty multi-level models, catering to different operational needs.
-
Elevator Furnaces
- Structural Characteristics: These furnaces feature a unique design where the heating chamber is lifted vertically to load or unload materials. This design minimizes heat loss and improves efficiency.
- Applications: Ideal for processes requiring uniform heating and precise temperature control, such as sintering and brazing.
-
Chamber and Muffle Furnaces
- Heating Elements: These furnaces use insulated chambers or muffle systems to isolate the heating environment from external contaminants.
- Applications: Suitable for processes like ashing, annealing, and heat treatment, where contamination must be avoided.
-
Tube Furnaces
- Design: Tube furnaces consist of a cylindrical heating chamber, often used for heating small samples or materials in a controlled atmosphere.
- Applications: Commonly used in research and development for processes like chemical vapor deposition, pyrolysis, and material testing.
-
High-Temperature Chamber Furnaces
- Temperature Capabilities: These furnaces can achieve extremely high temperatures, often exceeding 3000 °F (1650 °C).
- Applications: Used for advanced material testing, ceramic sintering, and other high-temperature processes.
-
Annealing and Curing Furnaces
- Purpose: Specifically designed for annealing (softening materials) and curing (hardening materials through heat).
- Applications: Widely used in the manufacturing of metals, glass, and polymers.
By understanding the different types of batch furnaces, including their designs, temperature ranges, and applications, users can select the most suitable furnace for their specific needs. Whether it's a versatile box furnace or a specialized tube furnace, each type offers unique advantages for industrial and laboratory processes.
Summary Table:
Type of Batch Furnace | Key Features | Applications |
---|---|---|
Box Furnaces | Versatile, front-loaded or forklift-loaded, temperature range up to 3100 °F. | Heat treatment, annealing, curing, calcining, stress relieving, preheating. |
Elevator Furnaces | Vertical heating chamber design for minimal heat loss and high efficiency. | Sintering, brazing, uniform heating processes. |
Chamber and Muffle Furnaces | Insulated chambers to prevent contamination, precise temperature control. | Ashing, annealing, heat treatment in contamination-sensitive processes. |
Tube Furnaces | Cylindrical heating chamber for controlled atmosphere heating. | Chemical vapor deposition, pyrolysis, material testing. |
High-Temperature Furnaces | Extremely high temperatures (exceeding 3000 °F). | Advanced material testing, ceramic sintering, high-temperature processes. |
Annealing and Curing Furnaces | Designed for softening (annealing) and hardening (curing) materials. | Manufacturing of metals, glass, and polymers. |
Need help choosing the right batch furnace for your needs? Contact our experts today for personalized advice!