Dental furnaces are essential equipment in dental laboratories and clinics, used for processing dental materials such as ceramics, metals, and zirconia. They play a critical role in creating durable and aesthetically pleasing dental restorations. The primary types of dental furnaces include sintering furnaces, ceramic furnaces, pressing furnaces, and burnout furnaces. Each type is designed for specific applications, such as sintering zirconia, firing porcelain, or pressing ceramic materials. Understanding the differences between these furnaces is crucial for selecting the right equipment based on the materials and procedures used in dental practices.
Key Points Explained:
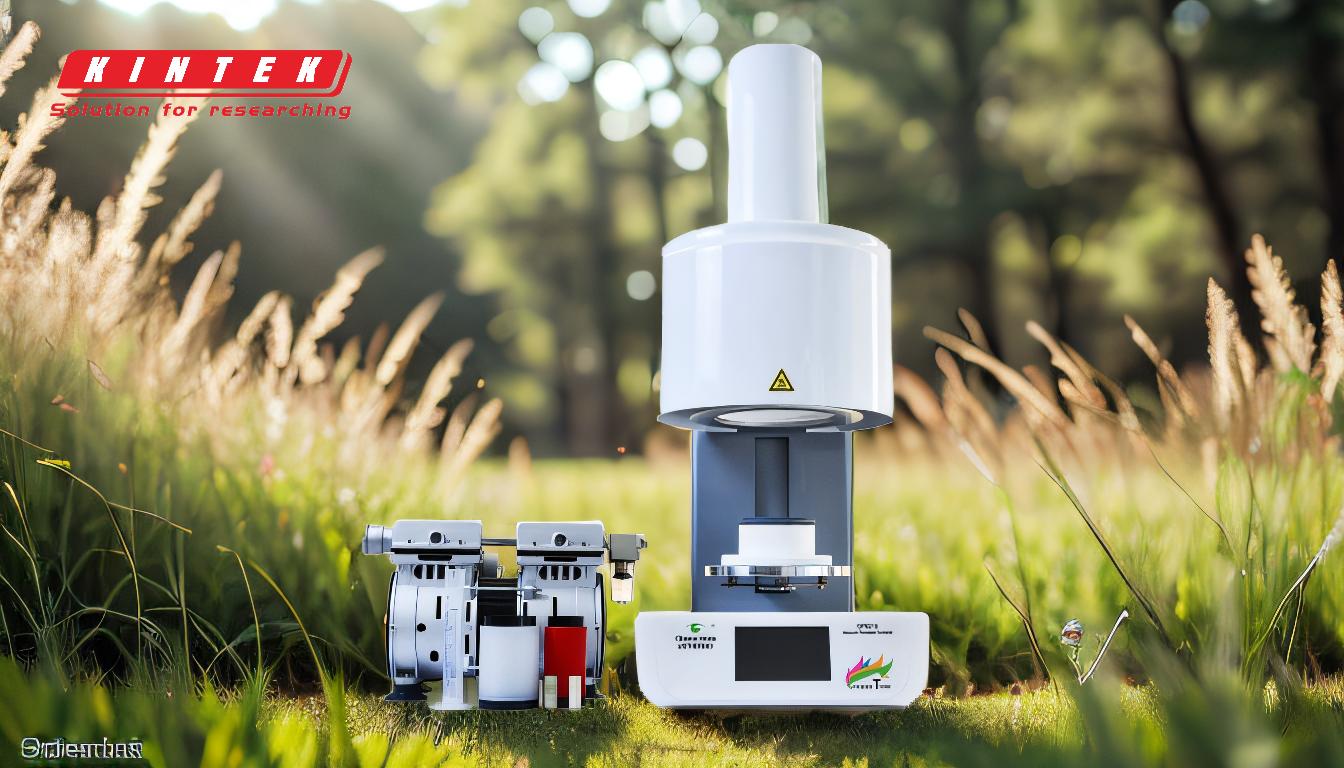
-
Sintering Furnaces
- Sintering furnaces are specifically designed for processing zirconia, a popular material for dental crowns, bridges, and implants.
- These furnaces heat zirconia to high temperatures (typically between 1,400°C and 1,600°C) to achieve optimal density and strength.
- Modern sintering furnaces often feature programmable settings and vacuum technology to ensure uniform heating and prevent oxidation.
- They are essential for achieving the high mechanical strength and aesthetic properties required in zirconia restorations.
-
Ceramic Furnaces
- Ceramic furnaces are used for firing porcelain and other ceramic materials to create dental crowns, veneers, and bridges.
- They operate at lower temperatures compared to sintering furnaces, typically ranging from 600°C to 1,000°C.
- These furnaces often include features like vacuum firing to eliminate air bubbles and ensure a smooth, high-quality finish.
- They are ideal for achieving the natural translucency and color matching required in esthetic dental restorations.
-
Pressing Furnaces
- Pressing furnaces are used in conjunction with pressing techniques to create dental restorations from ceramic materials like lithium disilicate.
- These furnaces heat the ceramic material until it becomes malleable, allowing it to be pressed into a mold to form the desired shape.
- They typically operate at temperatures between 700°C and 900°C and include programmable cycles for precise control.
- Pressing furnaces are valued for their ability to produce highly accurate and durable restorations with minimal material waste.
-
Burnout Furnaces
- Burnout furnaces are used to remove wax or resin patterns from investment molds before casting metal or pressing ceramic materials.
- They operate at moderate temperatures (usually between 500°C and 800°C) to ensure complete removal of the wax or resin without damaging the mold.
- These furnaces are essential for creating precise and defect-free dental restorations.
-
Key Features to Consider When Choosing a Dental Furnace
- Temperature Range and Control: Ensure the furnace can reach and maintain the required temperatures for your specific applications.
- Programmability: Look for furnaces with customizable programs to accommodate different materials and procedures.
- Vacuum Technology: Vacuum firing helps eliminate air bubbles and ensures consistent results.
- Cooling System: Efficient cooling systems reduce processing time and improve workflow efficiency.
- Ease of Use: User-friendly interfaces and automated features simplify operation and reduce the risk of errors.
By understanding the different types of dental furnaces and their specific applications, dental professionals can make informed decisions when selecting equipment for their practices. Each type of furnace offers unique advantages, and choosing the right one depends on the materials and techniques used in your dental laboratory or clinic.
Summary Table:
Type of Furnace | Primary Use | Temperature Range | Key Features |
---|---|---|---|
Sintering Furnaces | Processing zirconia for crowns, bridges, and implants | 1,400°C–1,600°C | Programmable settings, vacuum technology |
Ceramic Furnaces | Firing porcelain for crowns, veneers, and bridges | 600°C–1,000°C | Vacuum firing, smooth finish |
Pressing Furnaces | Pressing ceramic materials like lithium disilicate | 700°C–900°C | Programmable cycles, minimal waste |
Burnout Furnaces | Removing wax/resin from molds | 500°C–800°C | Precise, defect-free results |
Need help choosing the right dental furnace for your practice? Contact our experts today for personalized advice!