Electric Arc Furnaces (EAFs) are critical in modern metallurgy, offering a highly efficient and flexible method for melting metals using an electric arc. These furnaces are widely used in industries for steelmaking, recycling scrap metal, and producing alloys. EAFs are categorized based on their design, application, and operational characteristics. Below is a detailed explanation of the different types of EAFs and their unique features.
Key Points Explained:
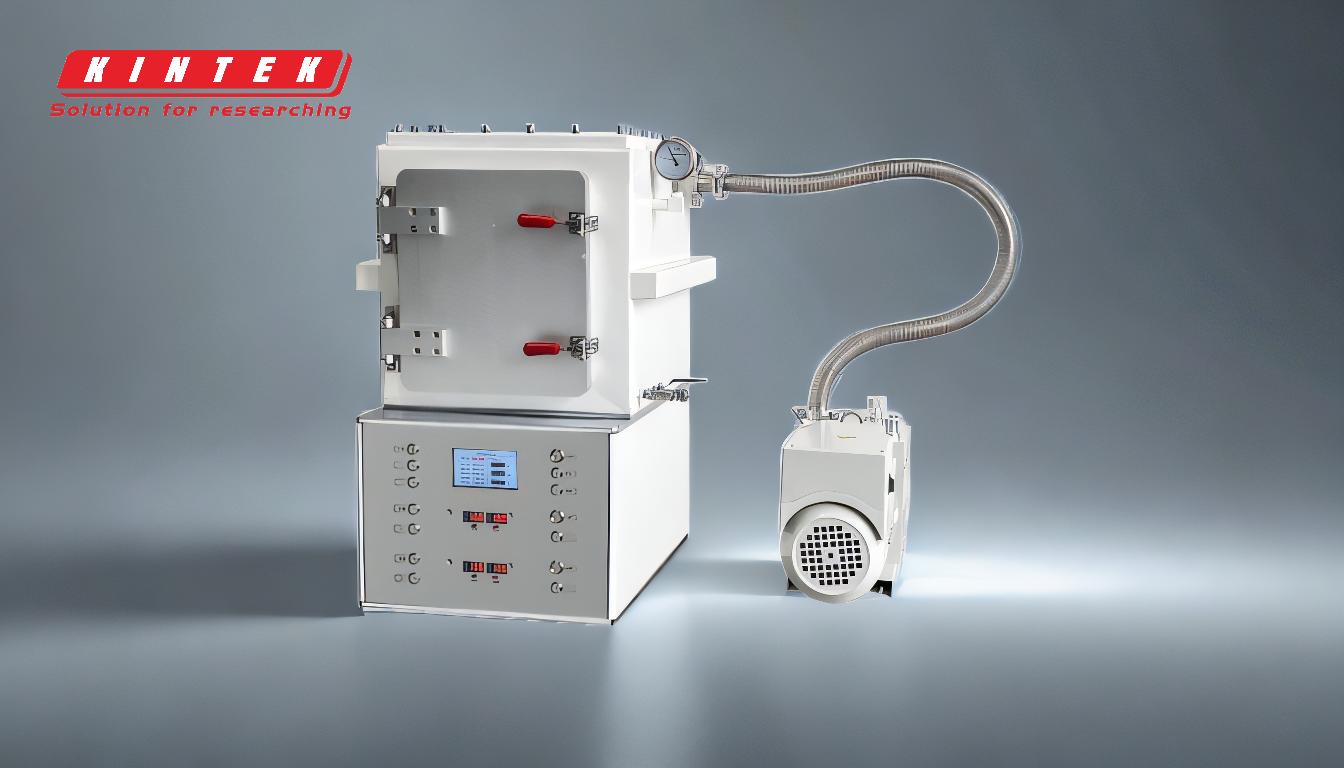
-
Basic Design and Functionality of EAFs
- EAFs generate heat by creating an electric arc between electrodes and the metal charge, reaching temperatures up to 1,800°C in industrial settings and even higher in laboratory conditions.
- They are primarily used for melting scrap metal, refining steel, and producing specialty alloys.
- The absence of a secondary heat source makes EAFs more energy-efficient and environmentally friendly compared to traditional blast furnaces.
-
Types of EAFs Based on Application
-
Steelmaking EAFs:
- These are the most common type, used in large-scale steel production.
- They are designed to handle high volumes of scrap metal and can produce a wide range of steel grades.
-
Foundry EAFs:
- Smaller in size, these furnaces are used in foundries for casting and producing small batches of metal.
- They are ideal for melting non-ferrous metals like aluminum, copper, and brass.
-
Laboratory EAFs:
- Used for research and development, these furnaces can achieve extremely high temperatures (over 3,000°C) for specialized metallurgical experiments.
-
Steelmaking EAFs:
-
Types of EAFs Based on Electrode Configuration
-
Direct Arc Furnaces:
- The most common type, where the arc is struck directly between the electrodes and the metal charge.
- This design ensures efficient heat transfer and uniform melting.
-
Indirect Arc Furnaces:
- The arc is struck between two electrodes, and the heat is transferred to the metal charge indirectly.
- These are less common and typically used for smaller-scale operations.
-
Direct Arc Furnaces:
-
Types of EAFs Based on Power Supply
-
AC (Alternating Current) EAFs:
- The most widely used type, offering cost-effectiveness and simplicity in operation.
- Suitable for large-scale industrial applications.
-
DC (Direct Current) EAFs:
- These furnaces use a single electrode and a conductive bottom plate, reducing electrode consumption and energy losses.
- They are more efficient but require higher initial investment.
-
AC (Alternating Current) EAFs:
-
Specialized EAFs
-
Vacuum Arc Furnaces:
- Operate under vacuum conditions to prevent oxidation and contamination of the metal.
- Used for producing high-purity metals and alloys, such as titanium and nickel-based superalloys.
-
Plasma Arc Furnaces:
- Use plasma torches instead of traditional electrodes, offering precise temperature control and the ability to melt refractory metals.
- Ideal for advanced materials research and specialty metal production.
-
Vacuum Arc Furnaces:
-
Advantages of EAFs
- Flexibility: Can melt a wide range of metals and alloys.
- Energy Efficiency: Lower energy consumption compared to traditional furnaces.
- Environmental Benefits: Reduced emissions and the ability to recycle scrap metal.
- Scalability: Available in various sizes to suit different production needs.
-
Challenges and Considerations
- High Initial Cost: Especially for advanced designs like DC and vacuum arc furnaces.
- Electrode Wear: Electrodes degrade over time and need regular replacement.
- Power Supply Requirements: EAFs require a stable and high-capacity power supply.
In summary, Electric Arc Furnaces are versatile and essential tools in modern metallurgy, with various types tailored to specific applications and operational requirements. Understanding the differences between these types helps in selecting the right EAF for a given industrial or research need.
Summary Table:
Category | Types of EAFs | Key Features |
---|---|---|
Based on Application | Steelmaking EAFs | Large-scale steel production, handles high volumes of scrap metal. |
Foundry EAFs | Smaller size, ideal for melting non-ferrous metals like aluminum and copper. | |
Laboratory EAFs | High-temperature capabilities (over 3,000°C) for specialized experiments. | |
Based on Electrodes | Direct Arc Furnaces | Arc struck directly between electrodes and metal charge for efficient melting. |
Indirect Arc Furnaces | Arc struck between two electrodes, heat transferred indirectly to metal charge. | |
Based on Power Supply | AC (Alternating Current) EAFs | Cost-effective, simple operation, suitable for large-scale industrial use. |
DC (Direct Current) EAFs | Higher efficiency, reduced electrode consumption, but higher initial cost. | |
Specialized EAFs | Vacuum Arc Furnaces | Operates under vacuum to produce high-purity metals like titanium. |
Plasma Arc Furnaces | Uses plasma torches for precise temperature control and refractory metal melting. |
Need help selecting the right Electric Arc Furnace for your needs? Contact our experts today for personalized advice!