Heat treatment furnaces are essential in various industries, including manufacturing, laboratories, and foundries, for processes like annealing, carburizing, and oxidation. The types of furnaces used depend on the specific application, material, and desired outcome. Common furnace types include tube furnaces, box furnaces, muffle furnaces, and specialized industrial furnaces like induction and cupola furnaces. Each furnace type is designed to operate under specific conditions, such as controlled atmospheres or high temperatures, to achieve precise heat treatment results. Below, we explore the different types of furnaces used in heat treatment and their applications.
Key Points Explained:
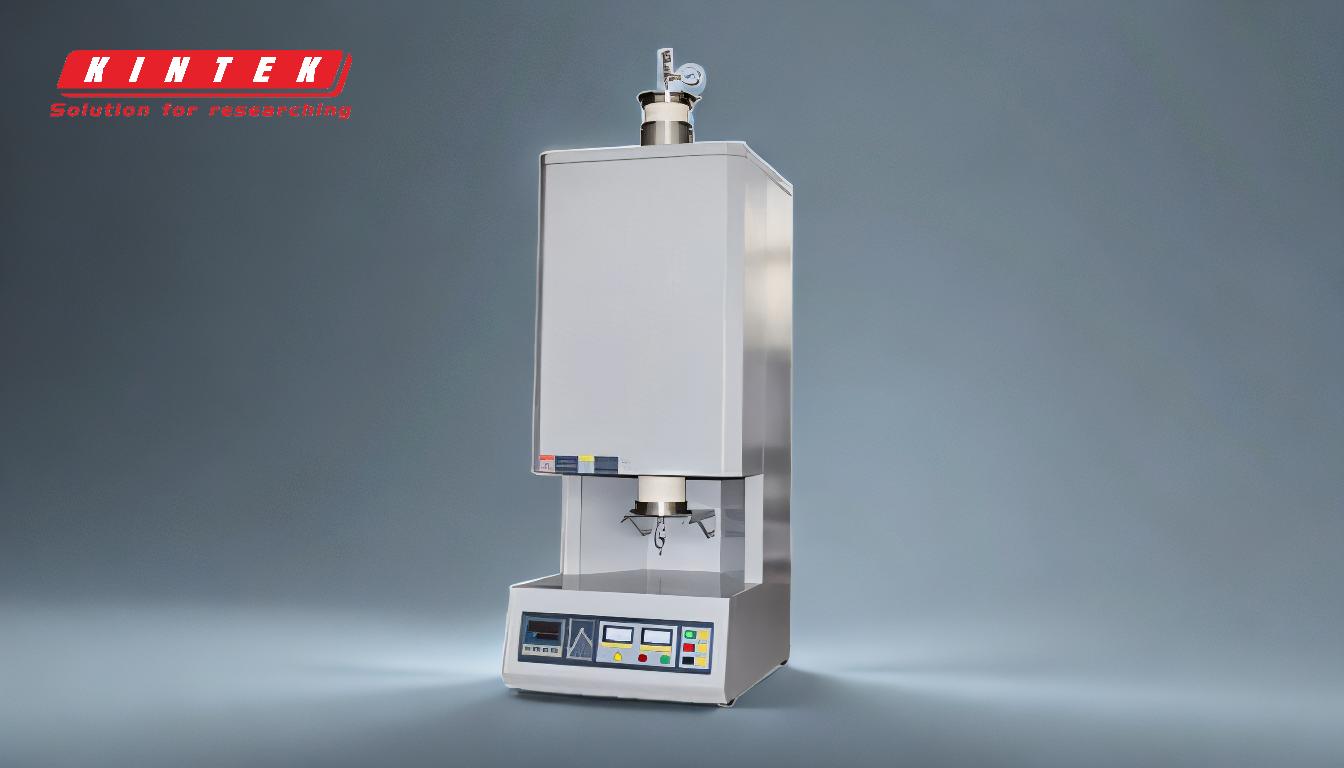
-
Tube Furnaces
- Tube furnaces are cylindrical in design and are commonly used in laboratories and small-scale industrial applications.
- They are ideal for processes requiring uniform heating, such as chemical vapor deposition and material testing.
- The cylindrical shape allows for precise temperature control and efficient heat distribution.
- Often used in research settings for annealing, sintering, and other heat treatment processes.
-
Box Furnaces
- Box furnaces, also known as chamber furnaces, are versatile and widely used in both laboratories and manufacturing.
- They feature a rectangular chamber and are suitable for batch processing of materials.
- Commonly used for annealing, tempering, and stress relieving of metals and ceramics.
- Their design allows for easy loading and unloading of materials, making them practical for industrial applications.
-
Muffle Furnaces
- Muffle furnaces are designed to isolate the material being heated from combustion byproducts, ensuring a clean heating environment.
- They are commonly used in laboratories for ashing, calcination, and heat treatment of small samples.
- The muffle design prevents contamination, making them ideal for processes requiring high purity.
- Often used in research and quality control applications.
-
Industrial Furnaces in Foundries
- Foundries use specialized furnaces for large-scale metal processing, including iron casting, induction heating, and crucible melting.
- Iron Casting Furnaces: Used for melting and casting iron, these furnaces operate at extremely high temperatures.
- Induction Furnaces: Utilize electromagnetic induction to heat metals, offering precise temperature control and energy efficiency.
- Crucible Furnaces: Small-scale furnaces used for melting non-ferrous metals, often in artisanal or small foundries.
- Cupola Furnaces: Vertical furnaces used primarily for melting iron in large quantities, commonly found in traditional foundries.
-
Controlled Atmosphere Furnaces
- These furnaces use specific gaseous mediums to achieve desired heat treatment outcomes.
- Carbon: Used in carburizing processes to harden the surface of steel.
- Nitrogen: Augments annealing processes by preventing oxidation.
- Argon: An inert gas used to improve annealing by creating a non-reactive environment.
- Carbon Dioxide: Provides strong oxygenated properties, aiding in oxidation processes.
-
Applications of Heat Treatment Furnaces
- Heat treatment furnaces are used across industries to alter the physical and chemical properties of materials.
- Common applications include annealing (softening metals), hardening (increasing strength), and tempering (reducing brittleness).
- In laboratories, furnaces are used for material research, quality testing, and small-scale production.
- In foundries, furnaces are critical for melting and shaping metals into usable forms.
By understanding the different types of furnaces and their specific applications, equipment and consumable purchasers can make informed decisions based on their operational needs. Whether for laboratory research, industrial manufacturing, or foundry operations, selecting the right furnace ensures optimal performance and desired outcomes in heat treatment processes.
Summary Table:
Furnace Type | Key Features | Applications |
---|---|---|
Tube Furnaces | Cylindrical design, uniform heating, precise temperature control | Chemical vapor deposition, material testing, annealing, sintering |
Box Furnaces | Rectangular chamber, batch processing, easy loading/unloading | Annealing, tempering, stress relieving of metals and ceramics |
Muffle Furnaces | Isolates material from combustion byproducts, clean heating environment | Ashing, calcination, heat treatment of small samples, high-purity processes |
Industrial Furnaces | Includes induction, crucible, and cupola furnaces for large-scale metal processing | Iron casting, induction heating, melting non-ferrous metals, traditional foundries |
Controlled Atmosphere | Uses gases like carbon, nitrogen, argon, and CO2 for specific heat treatment | Carburizing, annealing, oxidation processes |
Need help selecting the right furnace for your heat treatment needs? Contact our experts today!