Nitriding is a heat treatment process that introduces nitrogen into the surface of a metal to create a case-hardened surface. This process enhances the hardness, wear resistance, and fatigue life of the metal. There are several types of nitriding processes, each with its unique characteristics and applications. The most common types include gas nitriding, plasma (ion) nitriding, and salt bath nitriding. Each method has its advantages and is chosen based on the specific requirements of the material and the desired properties.
Key Points Explained:
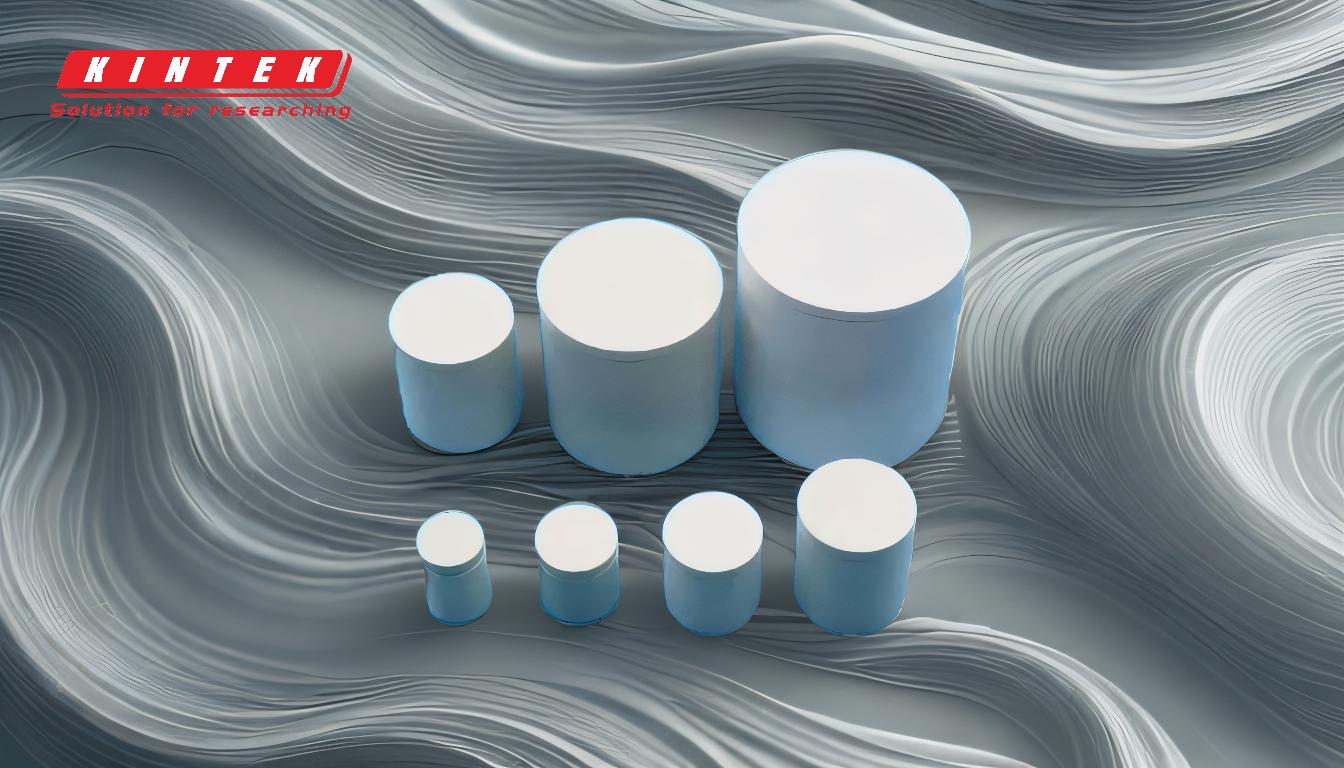
-
Gas Nitriding:
- Process: Gas nitriding involves heating the metal in an atmosphere of ammonia (NH₃) gas. At elevated temperatures, the ammonia decomposes into nitrogen and hydrogen. The nitrogen then diffuses into the surface of the metal, forming a hard nitride layer.
- Advantages: This method is known for its ability to produce a uniform and controllable case depth. It is suitable for a wide range of materials, including low-alloy steels, tool steels, and stainless steels.
- Applications: Gas nitriding is commonly used in the automotive and aerospace industries for components such as gears, crankshafts, and camshafts.
-
Plasma (Ion) Nitriding:
- Process: Plasma nitriding, also known as ion nitriding, involves placing the metal in a vacuum chamber and introducing nitrogen gas. A high-voltage electrical discharge ionizes the gas, creating a plasma that bombards the metal surface with nitrogen ions. This bombardment heats the metal and facilitates the diffusion of nitrogen into the surface.
- Advantages: This method offers precise control over the nitriding process, resulting in a very uniform and hard surface layer. It also allows for lower processing temperatures, reducing the risk of distortion in the metal.
- Applications: Plasma nitriding is often used for high-precision components in industries such as aerospace, medical devices, and tooling.
-
Salt Bath Nitriding:
- Process: Salt bath nitriding involves immersing the metal in a molten salt bath containing cyanide or cyanate salts. The nitrogen from the salts diffuses into the metal surface, forming a nitride layer.
- Advantages: This method is known for its rapid processing times and the ability to produce a very hard and wear-resistant surface. It is also relatively simple and cost-effective.
- Applications: Salt bath nitriding is commonly used for components that require high wear resistance, such as cutting tools, dies, and molds.
-
Flame Nitriding:
- Process: Flame nitriding involves exposing the metal surface to a high-temperature flame containing nitrogen. The nitrogen from the flame reacts with the metal surface, forming a nitride layer.
- Advantages: This method is relatively simple and can be performed with standard flame heating equipment. It is suitable for large or irregularly shaped components.
- Applications: Flame nitriding is used in applications where a hard surface layer is required, but the process needs to be performed quickly and with minimal equipment.
-
Laser Nitriding:
- Process: Laser nitriding involves using a high-power laser to irradiate the metal surface in the presence of nitrogen gas. The laser energy causes the nitrogen to react with the metal, forming a nitride layer.
- Advantages: This method offers precise control over the nitriding process, allowing for localized treatment of specific areas. It also produces a very hard and wear-resistant surface.
- Applications: Laser nitriding is used in applications where precise control over the nitriding process is required, such as in the aerospace and medical industries.
Each of these nitriding processes has its own set of advantages and is chosen based on the specific requirements of the metal and the desired properties. Understanding the differences between these processes can help in selecting the most appropriate method for a given application.
Summary Table:
Nitriding Process | Key Advantages | Common Applications |
---|---|---|
Gas Nitriding | Uniform case depth, suitable for various materials | Automotive gears, crankshafts, aerospace components |
Plasma (Ion) Nitriding | Precise control, lower distortion risk | Aerospace, medical devices, tooling |
Salt Bath Nitriding | Rapid processing, cost-effective | Cutting tools, dies, molds |
Flame Nitriding | Simple, minimal equipment | Large or irregularly shaped components |
Laser Nitriding | Localized treatment, high precision | Aerospace, medical industries |
Need help selecting the right nitriding process for your application? Contact our experts today!