Pellet mill dies are critical components in pellet production, determining the size, shape, and quality of the pellets. They come in various types, each designed for specific materials, production requirements, and operational conditions. The primary types include flat die and ring die pellet mills, with further classifications based on material, hole shape, and compression ratio. Understanding these types helps in selecting the right die for efficient and high-quality pellet production.
Key Points Explained:
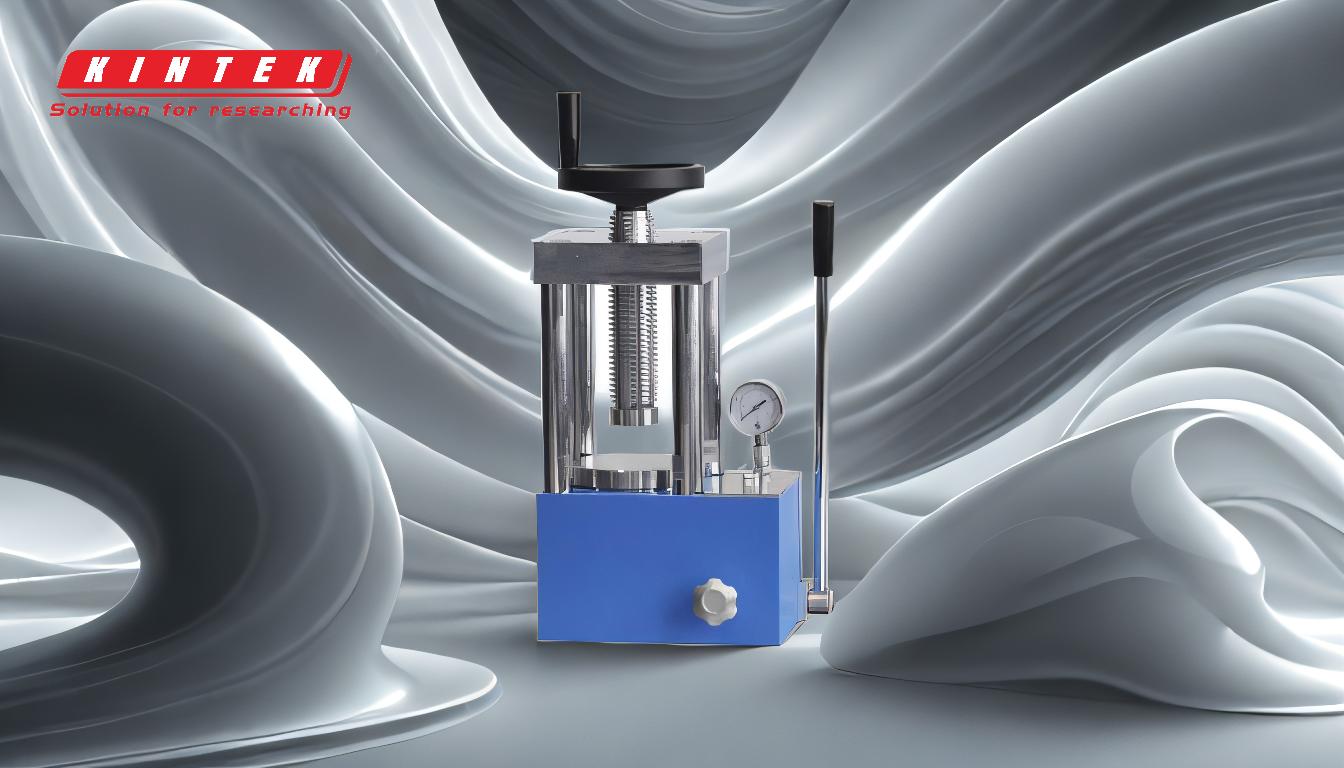
-
Flat Die Pellet Mill Dies
- Flat die pellet mills are commonly used for small-scale or home-based pellet production.
- The die is a flat, circular disk with holes through which the material is compressed to form pellets.
- These dies are simpler in design and easier to maintain, making them suitable for softer materials like biomass or animal feed.
- They are cost-effective and ideal for low-capacity operations.
-
Ring Die Pellet Mill Dies
- Ring die pellet mills are used for large-scale industrial pellet production.
- The die is a rotating ring with holes on its outer surface, and rollers press the material through these holes.
- These dies are more complex and durable, capable of handling harder materials like wood or feed grains.
- They offer higher production capacity and efficiency, making them suitable for commercial operations.
-
Die Material Types
- Stainless Steel Dies: Resistant to corrosion and wear, ideal for processing materials with high moisture or corrosive properties.
- Alloy Steel Dies: Known for their hardness and durability, suitable for abrasive materials like wood or minerals.
- Carbon Steel Dies: Cost-effective and commonly used for general-purpose pellet production.
-
Hole Shape and Configuration
- Cylindrical Holes: Produce uniform pellets with consistent size and shape, commonly used for feed pellets.
- Tapered Holes: Reduce friction and improve pellet density, often used for biomass or wood pellets.
- Step Holes: Combine cylindrical and tapered features, enhancing pellet quality and reducing energy consumption.
-
Compression Ratio
- The compression ratio is the ratio of the effective length of the die hole to its diameter.
- Higher compression ratios produce denser and harder pellets, suitable for materials requiring high durability.
- Lower compression ratios are used for softer materials or when energy efficiency is a priority.
-
Die Maintenance and Lifespan
- Regular cleaning and proper lubrication extend the lifespan of pellet mill dies.
- Abrasive materials can cause faster wear, so choosing the right die material is crucial.
- Reconditioning or re-boring dies can restore their performance and reduce replacement costs.
By understanding these types and features, pellet mill operators can select the most appropriate die for their specific needs, ensuring optimal performance and cost-efficiency in pellet production.
Summary Table:
Type | Description | Best For |
---|---|---|
Flat Die | Flat, circular disk with holes; simple design, easy maintenance. | Small-scale or home-based production, softer materials like biomass or feed. |
Ring Die | Rotating ring with holes; durable, high-capacity. | Large-scale industrial production, harder materials like wood or feed grains. |
Stainless Steel | Resistant to corrosion and wear. | Materials with high moisture or corrosive properties. |
Alloy Steel | Hard and durable. | Abrasive materials like wood or minerals. |
Carbon Steel | Cost-effective, general-purpose. | General-purpose pellet production. |
Cylindrical Holes | Uniform pellets with consistent size and shape. | Feed pellets. |
Tapered Holes | Reduce friction, improve pellet density. | Biomass or wood pellets. |
Step Holes | Combine cylindrical and tapered features, enhance quality, reduce energy use. | High-quality pellets with energy efficiency. |
Need help selecting the right pellet mill die for your production needs? Contact our experts today!