Thin film technologies are diverse and cater to a wide range of applications across various industries. They are broadly categorized based on their properties and the deposition methods used. The main types of thin films include optical, electrical/electronic, magnetic, chemical, mechanical, and thermal films. These films are created using different deposition technologies, such as physical vapor deposition (PVD), chemical vapor deposition (CVD), and epitaxial processes. The materials used for thin film deposition include chemical precursors, electrochemical deposition materials, evaporation materials, and sputtering targets. Each type of thin film and deposition method has unique properties and applications, making them suitable for specific industrial needs.
Key Points Explained:
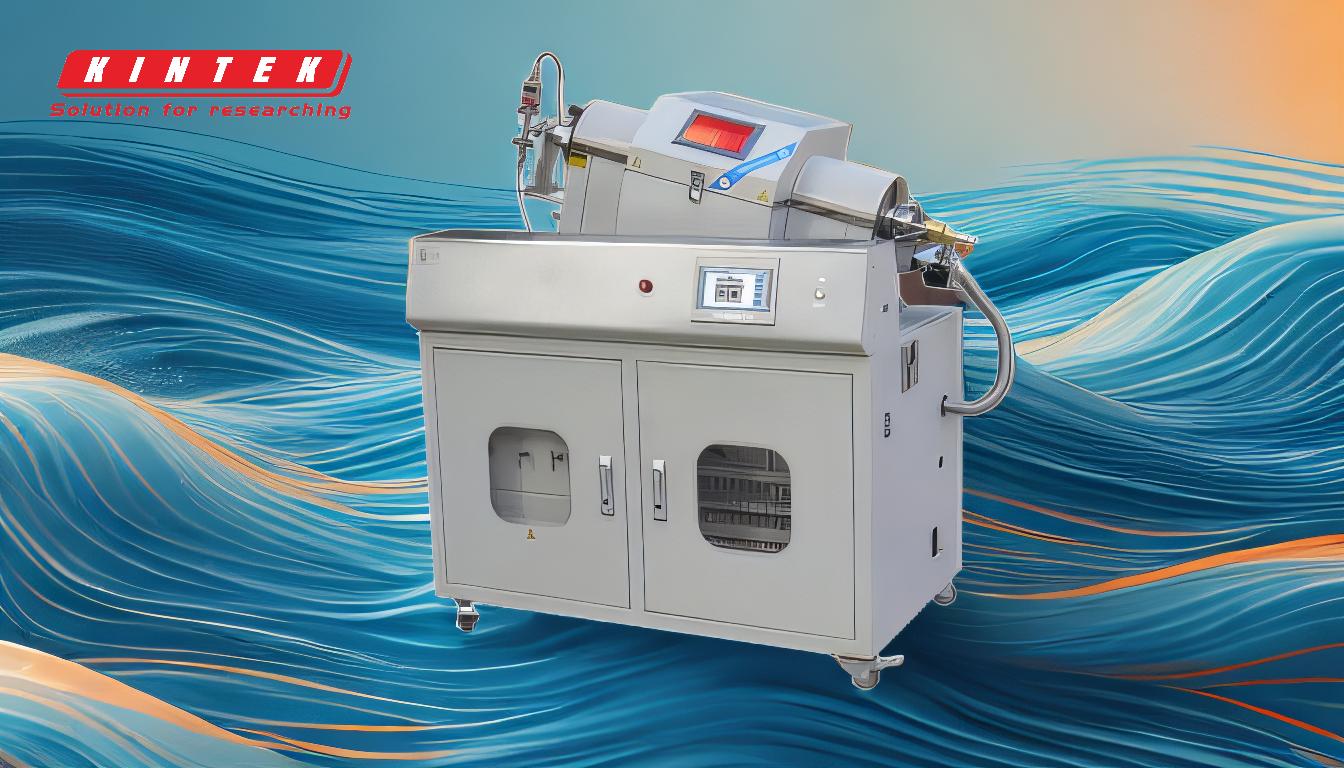
-
Types of Thin Films Based on Properties:
- Optical Films: Used for reflective coatings, anti-reflective coatings, solar cells, monitors, waveguides, and optical detector arrays. These films manipulate light to enhance or reduce reflection, improve efficiency in solar cells, or guide light in optical devices.
- Electrical/Electronic Films: Used for insulators, conductors, semiconductor devices, integrated circuits, and piezoelectric drives. These films are essential in the electronics industry for creating components that conduct or insulate electricity.
- Magnetic Films: Primarily used for memory disks. These films store data magnetically and are crucial in data storage technologies.
- Chemical Films: Provide resistance to alloying, diffusion, corrosion, and oxidation. They are also used in gas and liquid sensors. These films protect surfaces from chemical degradation and are used in sensing applications.
- Mechanical Films: Used for tribological coatings to protect against abrasion, increase hardness and adhesion, and utilize micro-mechanical properties. These films enhance the durability and performance of mechanical components.
- Thermal Films: Used for insulation layers and heat sinks. These films manage heat transfer, making them essential in thermal management applications.
-
Thin Film Deposition Technologies:
- Physical Vapor Deposition (PVD): Involves physical processes like sputtering and evaporation. In sputtering, atoms or molecules are knocked off a target material and deposited onto a substrate. In evaporation, materials are heated until they vaporize and then condense onto a substrate.
- Chemical Vapor Deposition (CVD): Involves chemical reactions to deposit thin films. Precursor gases react on the substrate surface to form the desired film. This method is widely used for creating high-quality, uniform films.
- Epitaxial Processes: Involve the growth of a crystalline film on a crystalline substrate. This method is used to create films with precise crystal structures, essential for semiconductor applications.
-
Materials Used in Thin Film Deposition:
- Chemical Precursors: Stock products in liquid, solid, or gaseous form that undergo chemical changes to deposit onto a substrate. These are used in CVD and other chemical deposition methods.
- Electrochemical Deposition Materials: Deposited onto a substrate in a wet electrochemical process. This method is often used for creating metal films.
- Evaporation Materials: Include wire, sheet, or bulk solids that are boiled or sublimed to produce vapors, which then condense onto a substrate. This is a common PVD technique.
- Sputtering Targets: Used in sputtering processes where atoms or molecules of the target material are knocked off and deposited onto a substrate. This method is widely used in the production of thin films for electronics and optics.
-
Applications of Thin Film Technologies:
- Optical Applications: Enhancing the performance of optical devices, improving energy efficiency in solar cells, and creating anti-reflective coatings for lenses and displays.
- Electronic Applications: Fabricating semiconductor devices, integrated circuits, and piezoelectric components. These films are critical in the miniaturization and performance enhancement of electronic devices.
- Magnetic Applications: Data storage in memory disks and other magnetic storage devices. These films are essential for the high-density storage of digital information.
- Chemical Applications: Protecting surfaces from corrosion and oxidation, and creating sensors for detecting gases and liquids. These films are vital in industries where chemical resistance is required.
- Mechanical Applications: Improving the durability and performance of mechanical components through tribological coatings. These films reduce wear and extend the life of mechanical parts.
- Thermal Applications: Managing heat transfer in electronic devices and other applications requiring thermal insulation or heat dissipation. These films help in maintaining optimal operating temperatures.
-
Industry-Specific Techniques:
- Magnetron Sputtering: A specific PVD technique used for depositing thin films with high precision and uniformity. It is widely used in the production of optical and electronic films.
- Molecular Beam Epitaxy (MBE): An epitaxial process used for growing high-quality crystalline films. This technique is essential in the semiconductor industry for creating precise layers in electronic devices.
By understanding the different types of thin films, their deposition methods, and the materials used, one can select the appropriate technology for specific applications, ensuring optimal performance and efficiency in various industries.
Summary Table:
Category | Types of Thin Films | Deposition Methods | Key Applications |
---|---|---|---|
Optical | Reflective, anti-reflective | PVD, CVD | Solar cells, monitors, optical devices |
Electrical/Electronic | Conductors, insulators | PVD, CVD, epitaxial processes | Semiconductor devices, integrated circuits, piezoelectric drives |
Magnetic | Memory disks | PVD | Data storage technologies |
Chemical | Corrosion-resistant coatings | CVD, electrochemical | Gas/liquid sensors, surface protection |
Mechanical | Tribological coatings | PVD | Abrasion protection, hardness enhancement |
Thermal | Insulation layers, heat sinks | PVD, CVD | Thermal management in electronics and industrial applications |
Need help selecting the right thin film technology for your application? Contact our experts today!