Annealing heat treatment, while beneficial for improving machinability, mechanical properties, and workability of materials, has several disadvantages. These include potential material softening, which may reduce hardness and strength, making it unsuitable for applications requiring high wear resistance. The process can also lead to grain growth, negatively impacting mechanical properties. Additionally, annealing requires precise temperature control and cooling rates, making it time-consuming and energy-intensive. It may also alter the material's microstructure in undesirable ways, and in some cases, it can introduce surface oxidation or decarburization, compromising the material's surface integrity.
Key Points Explained:
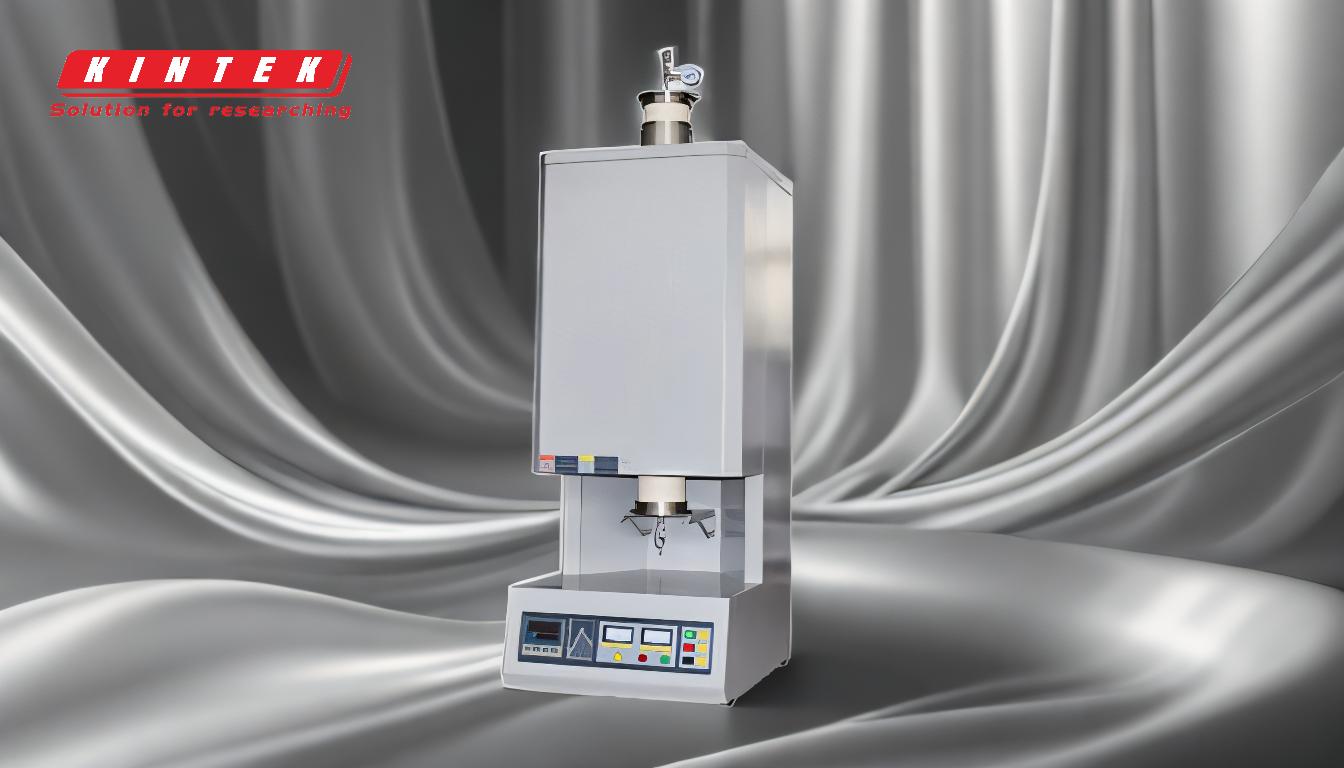
-
Material Softening:
- Annealing reduces the hardness and strength of the material by softening it. This can be a disadvantage in applications where high wear resistance or strength is required. For instance, tools or components subjected to high stress may not perform well after annealing.
-
Grain Growth:
- During annealing, grains within the material can grow larger. This grain growth can negatively affect mechanical properties such as toughness and fatigue resistance. Larger grains can lead to a reduction in the material's overall performance under load.
-
Time and Energy Consumption:
- The annealing process requires precise control over temperature and cooling rates, making it a time-consuming and energy-intensive process. This can increase production costs and lead times, especially for large-scale manufacturing.
-
Microstructural Changes:
- Annealing can alter the material's microstructure in ways that may not be desirable for specific applications. For example, certain phases or structures that contribute to the material's strength or other properties may be lost or transformed during the annealing process.
-
Surface Oxidation and Decarburization:
- The high temperatures involved in annealing can lead to surface oxidation or decarburization, especially in metals like steel. This can compromise the surface integrity and mechanical properties of the material, requiring additional surface treatments or machining to restore the desired properties.
-
Limited Applicability:
- Not all materials or applications benefit from annealing. For example, materials that require high hardness or specific microstructures may not be suitable for annealing, as the process can counteract these requirements.
-
Potential for Distortion:
- During the heating and cooling phases of annealing, there is a risk of distortion or warping of the material, especially in complex or thin-walled components. This can lead to dimensional inaccuracies and the need for additional machining or corrective measures.
By understanding these disadvantages, equipment and consumable purchasers can make informed decisions about whether annealing is the appropriate heat treatment for their specific needs and applications.
Summary Table:
Disadvantage | Impact |
---|---|
Material Softening | Reduces hardness and strength, unsuitable for high wear resistance. |
Grain Growth | Negatively affects toughness and fatigue resistance. |
Time and Energy Consumption | Increases production costs and lead times. |
Microstructural Changes | May alter desirable phases or structures in the material. |
Surface Oxidation/Decarburization | Compromises surface integrity, requiring additional treatments. |
Limited Applicability | Not suitable for materials requiring high hardness or specific microstructures. |
Potential for Distortion | Risk of warping, especially in complex or thin-walled components. |
Need help deciding if annealing is right for your application? Contact our experts today for personalized advice!