Coreless induction furnaces, while efficient and versatile, have several disadvantages that can impact their performance and suitability for certain applications. These include limitations in refining capacity, dependence on high-quality charge materials, potential loss of alloying elements, and challenges in handling specific types of metals. Additionally, the initial setup and operational costs, along with the need for precise process control, can be significant. Understanding these drawbacks is crucial for making informed decisions when selecting melting equipment for industrial processes.
Key Points Explained:
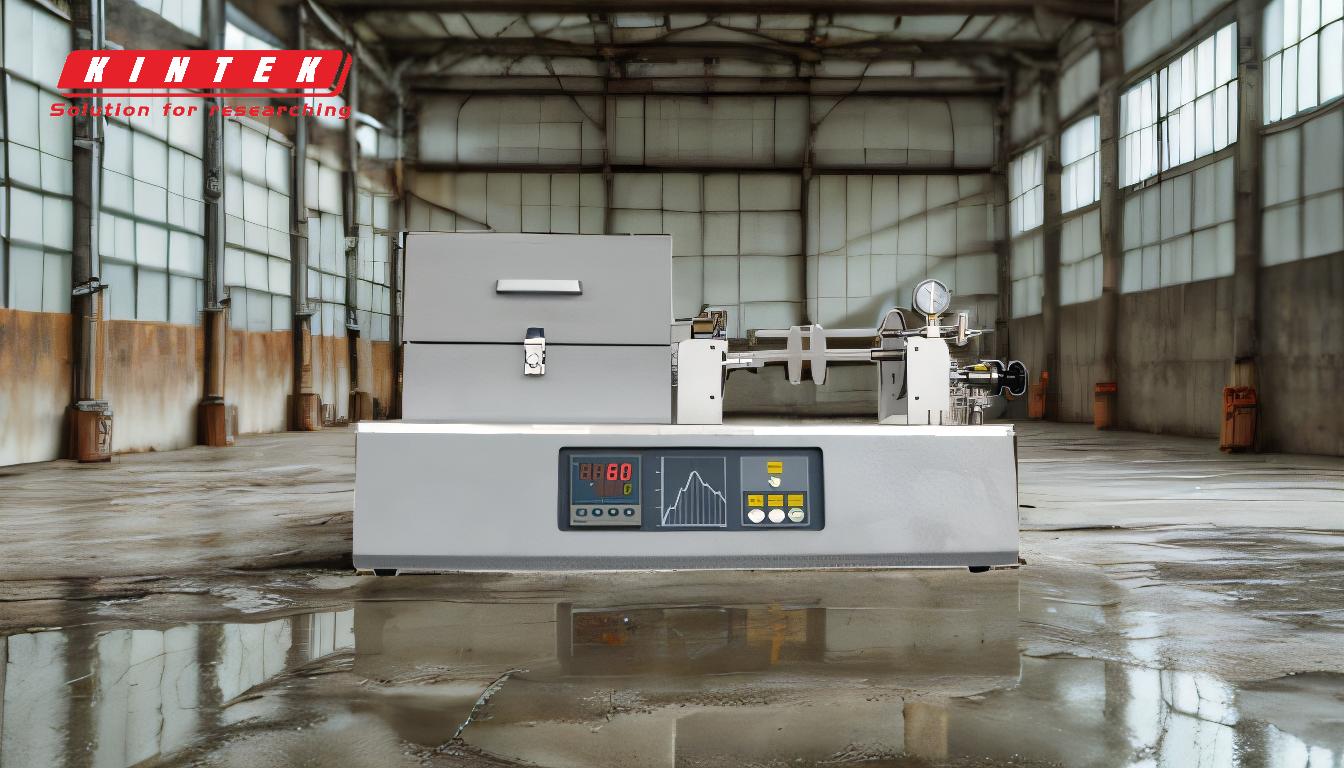
-
Lack of Refining Capacity:
- Coreless induction furnaces are primarily melting units and lack the ability to refine metals. This means that the charge materials must already be free of oxides and impurities. If the raw materials contain contaminants, the furnace cannot remove them, which can compromise the quality of the final product.
- This limitation makes it unsuitable for applications where refining is necessary, such as in the production of high-purity metals or alloys.
-
Dependence on High-Quality Charge Materials:
- Since the furnace cannot refine the charge, the quality of the final product is heavily dependent on the quality of the input materials. This requires careful selection and preparation of raw materials, which can increase costs and complexity.
- Any impurities or inconsistencies in the charge can lead to defects in the final product, making it less suitable for high-precision applications.
-
Loss of Alloying Elements:
- Some alloying elements may be lost during the melting process due to oxidation. This is particularly problematic for elements that are prone to oxidation, such as aluminum or magnesium.
- To compensate for this loss, additional alloying elements may need to be added to the melt, which can increase material costs and complicate the process.
-
Challenges with Specific Metals:
- Coreless induction furnaces may not be suitable for melting certain types of metals, such as those with high melting points or those that require specific atmospheric conditions (e.g., vacuum or inert gas environments).
- For such applications, a vacuum induction furnace might be more appropriate, as it can provide the necessary control over the melting environment.
-
High Initial and Operational Costs:
- The initial setup cost for a coreless induction furnace can be high, particularly when considering the need for a robust power supply unit, cooling system, and process control system.
- Operational costs can also be significant, especially in terms of energy consumption and maintenance of the furnace components.
-
Precision and Control Requirements:
- While induction furnaces offer high temperature control accuracy, achieving this level of precision requires sophisticated process control systems. Any failure in these systems can lead to inconsistencies in the melting process, affecting the quality of the final product.
- The need for precise control also means that operators must be highly skilled, adding to the operational complexity and cost.
-
Environmental and Safety Considerations:
- Although induction furnaces generate minimal waste and pollutants, they still require fume extraction equipment to handle any emissions. This adds to the overall cost and complexity of the system.
- Safety is another concern, particularly when dealing with high temperatures and molten metals. Proper safety measures must be in place to protect workers and equipment.
In summary, while coreless induction furnaces offer several advantages, such as fast heating and high efficiency, they also come with significant drawbacks. These include limitations in refining capacity, dependence on high-quality charge materials, potential loss of alloying elements, and challenges with specific metals. Additionally, the high initial and operational costs, along with the need for precise control, can make them less suitable for certain applications. Understanding these disadvantages is essential for making informed decisions when selecting melting equipment.
Summary Table:
Disadvantage | Key Details |
---|---|
Lack of Refining Capacity | Cannot refine metals; requires high-quality, impurity-free charge materials. |
Dependence on Quality Materials | Final product quality depends on input material quality, increasing costs. |
Loss of Alloying Elements | Oxidation leads to loss of elements like aluminum or magnesium. |
Challenges with Specific Metals | Unsuitable for high-melting-point metals or those needing controlled atmospheres. |
High Initial and Operational Costs | Significant setup and operational expenses, including energy and maintenance. |
Precision and Control Requirements | Requires skilled operators and advanced process control systems. |
Environmental and Safety Concerns | Needs fume extraction equipment and strict safety measures. |
Need help choosing the right melting equipment? Contact our experts today for tailored solutions!