Press working, while efficient for mass production and capable of producing high-strength components, comes with several disadvantages that can impact cost, efficiency, and operational flexibility. The process places significant stress on dies, requiring harder and more durable materials to prevent breakage, which increases tooling costs. Additionally, the fabrication and maintenance of dies are expensive, and the process of changing dies is time-consuming, reducing overall productivity. These factors make press working less suitable for small-scale or custom production runs.
Key Points Explained:
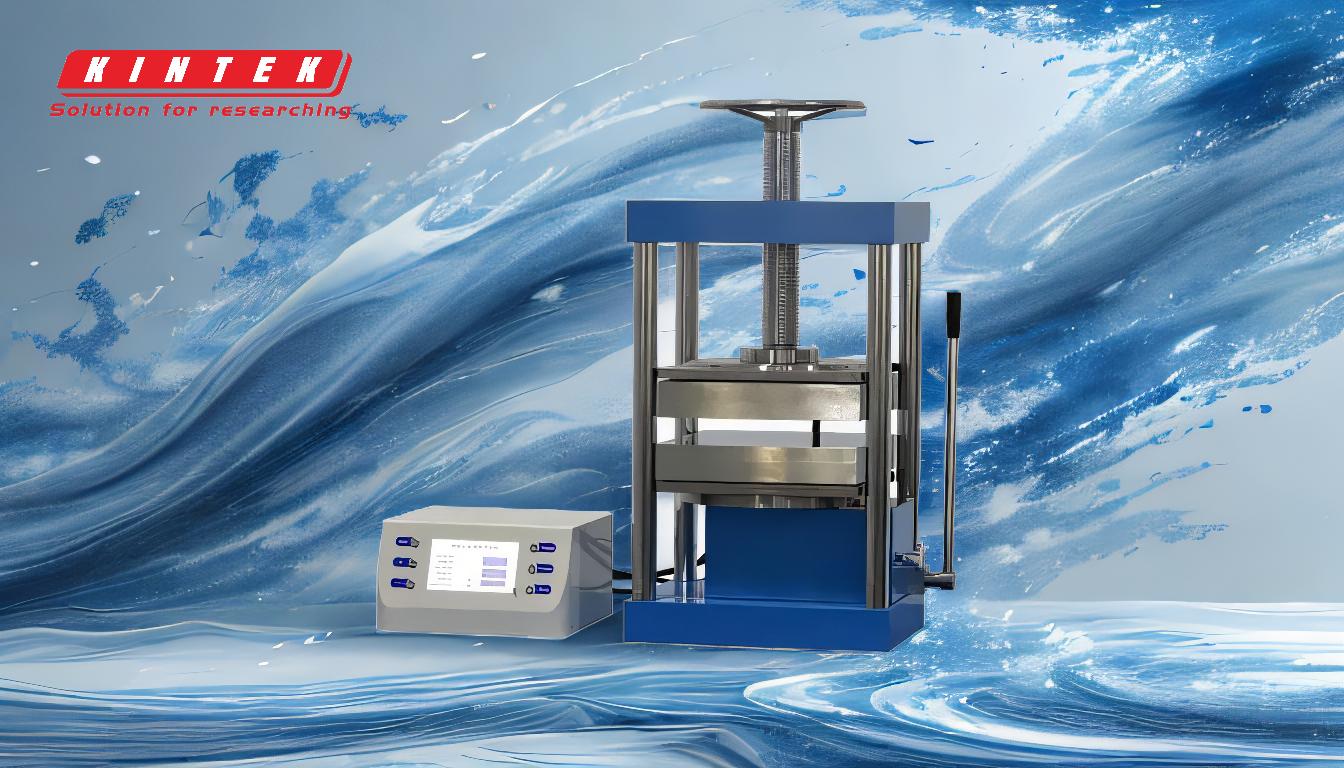
-
High Stress on Dies:
- Press working involves applying substantial mechanical force to shape materials, which places a great deal of stress on the dies. This stress can lead to wear and tear, requiring harder and more durable die materials to prevent breakage and damage. The need for high-quality dies increases the overall cost of the process.
-
Expensive Tooling and Die Fabrication:
- The fabrication of dies is a complex and costly process. Dies must be precisely engineered to withstand the forces involved in press working, and this precision engineering comes at a high price. Additionally, maintaining these dies to ensure they remain in good working condition adds to the ongoing costs.
-
Slow and Tedious Die Changes:
- Changing dies in a press working setup is a slow and labor-intensive process. This can lead to significant downtime, reducing the overall efficiency and productivity of the manufacturing process. For operations that require frequent die changes, this can be a major drawback.
-
Limited Flexibility for Small-Scale Production:
- Due to the high costs associated with tooling and die changes, press working is less economical for small-scale or custom production runs. The initial investment in dies and the time required for setup make it more suitable for large-scale, high-volume production.
-
Impact on Operational Efficiency:
- The combination of high tooling costs, the need for durable dies, and the time-consuming nature of die changes can significantly impact the operational efficiency of a press working setup. These factors must be carefully managed to ensure that the benefits of press working outweigh the disadvantages.
In summary, while press working offers many advantages in terms of production speed and component strength, the disadvantages related to die stress, tooling costs, and operational flexibility must be carefully considered. These factors can impact the overall cost-effectiveness and efficiency of the process, particularly for smaller production runs or custom manufacturing needs.
Summary Table:
Disadvantages | Key Details |
---|---|
High Stress on Dies | Requires durable, expensive materials to prevent wear and tear. |
Expensive Tooling & Dies | Complex fabrication and maintenance increase costs. |
Slow Die Changes | Time-consuming process reduces productivity and efficiency. |
Limited Small-Scale Suitability | High costs make it less economical for custom or small production runs. |
Operational Efficiency Impact | Tooling costs and downtime affect overall efficiency. |
Need help optimizing your production process? Contact our experts today to find the best solution for your needs!