Extrusion is a widely used manufacturing process, but it comes with several disadvantages that can impact product quality, cost, and flexibility. The primary drawbacks include variations in product size, limitations in product design due to the uniformity of cross-sections, and the high initial setup costs. These factors can make extrusion less suitable for certain applications, especially those requiring complex geometries or tight tolerances.
Key Points Explained:
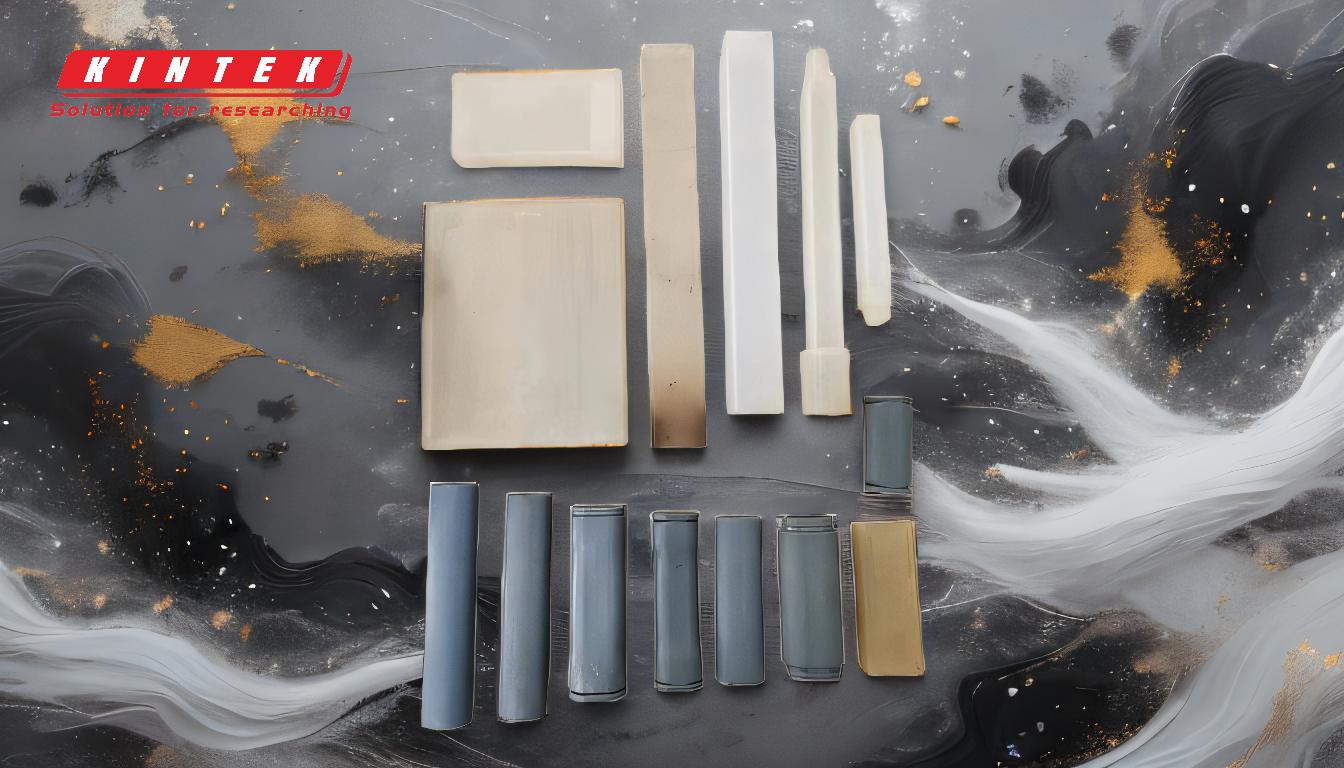
-
Variations in Product Size:
- Explanation: During the extrusion process, maintaining consistent product dimensions can be challenging. Factors such as temperature fluctuations, material inconsistencies, and machine wear can lead to variations in the size of the extruded product.
- Impact: These variations can result in products that do not meet precise specifications, leading to potential quality control issues and increased waste. For industries requiring tight tolerances, such as aerospace or medical devices, this can be a significant drawback.
-
Product Limitations:
- Explanation: Extrusion typically produces products with a uniform cross-section along the entire length. This means that only one type of cross-section can be obtained at a time, limiting the design flexibility.
- Impact: This limitation can be a significant disadvantage for applications that require complex geometries or varying cross-sections. For example, creating parts with intricate shapes or multiple profiles would require additional processing steps, increasing both time and cost.
-
High Initial Setup Cost:
- Explanation: The initial investment required for extrusion equipment and tooling can be substantial. This includes the cost of the extrusion machine, dies, and other necessary tooling, as well as the expenses associated with setting up the production line.
- Impact: The high upfront cost can be a barrier for small to medium-sized enterprises (SMEs) or startups looking to adopt extrusion processes. Additionally, the cost of maintaining and replacing tooling over time can add to the overall expense, making it less economical for low-volume production runs.
In summary, while extrusion is a versatile and efficient manufacturing process, it is not without its drawbacks. Variations in product size, design limitations, and high initial costs are significant factors that need to be considered when choosing extrusion for a particular application. Understanding these disadvantages can help manufacturers make informed decisions and explore alternative processes if necessary.
Summary Table:
Disadvantage | Explanation | Impact |
---|---|---|
Variations in Product Size | Temperature fluctuations, material inconsistencies, and machine wear cause size variations. | Leads to quality control issues, increased waste, and challenges in tight-tolerance industries. |
Product Limitations | Extrusion produces uniform cross-sections, limiting design flexibility. | Additional processing steps required for complex geometries, increasing time and cost. |
High Initial Setup Cost | Significant investment in equipment, tooling, and production line setup. | Barrier for SMEs and startups; less economical for low-volume production. |
Need help choosing the right manufacturing process? Contact our experts today for tailored solutions!