Tungsten, despite its impressive physical properties such as the highest melting point among pure metals and excellent high-temperature strength, has several disadvantages that limit its applications and handling. These include difficulties in machining, brittleness at low temperatures, susceptibility to embrittlement and oxidation at high temperatures, and challenges in processing and fabrication. Understanding these limitations is crucial for industries that rely on tungsten for its unique properties.
Key Points Explained:
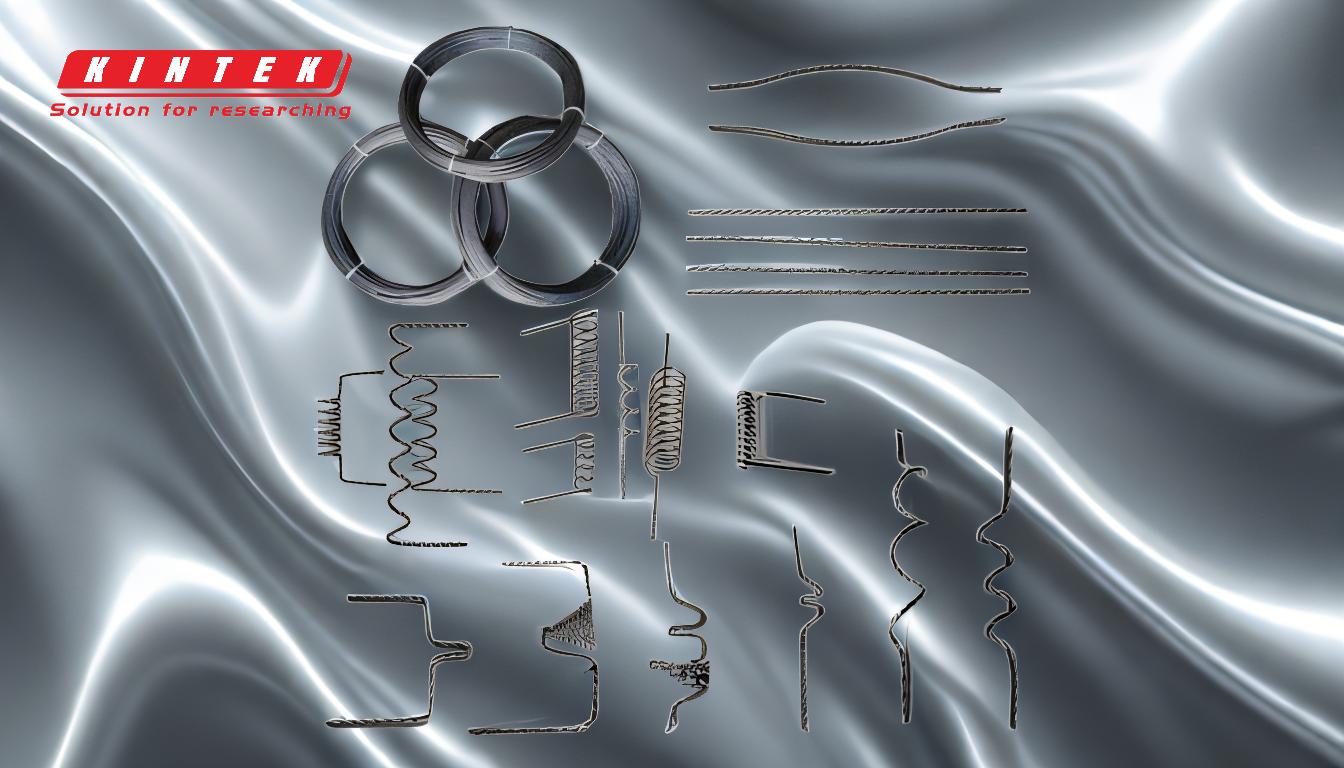
-
Difficulty in Machining and Fabrication:
- Loading of Diamond Tools: Pure tungsten is difficult to machine because it becomes compacted into the spaces between diamond tools, a condition known as loading. This renders the cutting tool ineffective and complicates the machining process.
- Limited Fabrication Techniques: Pure tungsten cannot be drawn over a mandrel or extruded into a tube, limiting the methods available for shaping the material.
-
Brittleness at Low Temperatures:
- Ductile-to-Brittle Transition Temperature (DBTT): Tungsten has a ductile-to-brittle transition temperature (DBTT) that is higher than room temperature. This means that at low temperatures, tungsten is brittle and difficult to work with, which can lead to cracking or failure under stress.
- Impact of Impurities: The presence of impurities or contamination can exacerbate the brittleness of tungsten, making it even more challenging to handle and process.
-
Susceptibility to Embrittlement and Oxidation at High Temperatures:
- Embrittlement: Tungsten heating elements are susceptible to embrittlement, mechanical and thermal shock, and oxidation in air at elevated temperatures. This limits their use in high-temperature environments unless protective measures are taken.
- Oxidation: Tungsten must not be exposed to air above 500°C (932°F) to avoid oxidation, which can degrade its properties and lead to failure. A ramping temperature control system is often required to prevent embrittlement during cold start-up.
-
Challenges in Processing and Alloying:
- Metalworking and Alloying: The mechanical properties of tungsten are influenced by its purity, type, and composition of alloying elements, as well as heat treatment and microstructure. While metalworking and alloying can reduce the ductile-to-brittle transition temperature and improve strength and ductility, these processes add complexity and cost to the production of tungsten components.
- Thermal Stability: Although tungsten has high thermal stability, its brittleness and susceptibility to oxidation at high temperatures can limit its use in certain high-temperature applications.
In summary, while tungsten offers exceptional properties such as high melting point and thermal stability, its disadvantages—including difficulties in machining, brittleness at low temperatures, and susceptibility to embrittlement and oxidation at high temperatures—pose significant challenges. These limitations must be carefully considered in applications where tungsten is used, and appropriate measures should be taken to mitigate these issues.
Summary Table:
Disadvantages of Tungsten | Key Details |
---|---|
Machining and Fabrication | - Loading of diamond tools complicates machining. |
- Limited fabrication techniques (e.g., cannot be drawn or extruded). | |
Brittleness at Low Temperatures | - High ductile-to-brittle transition temperature (DBTT). |
- Impurities worsen brittleness, increasing risk of cracking. | |
Embrittlement and Oxidation | - Susceptible to embrittlement and oxidation above 500°C (932°F). |
- Requires protective measures for high-temperature use. | |
Processing and Alloying | - Alloying adds complexity and cost. |
- Brittleness and oxidation limit high-temperature applications. |
Need help managing tungsten's challenges? Contact our experts today for tailored solutions!