The choice of frequency in induction heating is influenced by several key factors, including the material properties, size and thickness of the workpiece, desired heating depth, efficiency, and specific application requirements. Higher frequencies are suitable for smaller, thinner materials and shallow heating depths, while lower frequencies are better for larger, thicker materials requiring deeper heat penetration. Material resistivity, power supply capacity, and inductor design also play critical roles. Additionally, cost considerations and process requirements, such as the need for stirring effects or noise reduction, must be taken into account to optimize the system's performance and cost-effectiveness.
Key Points Explained:
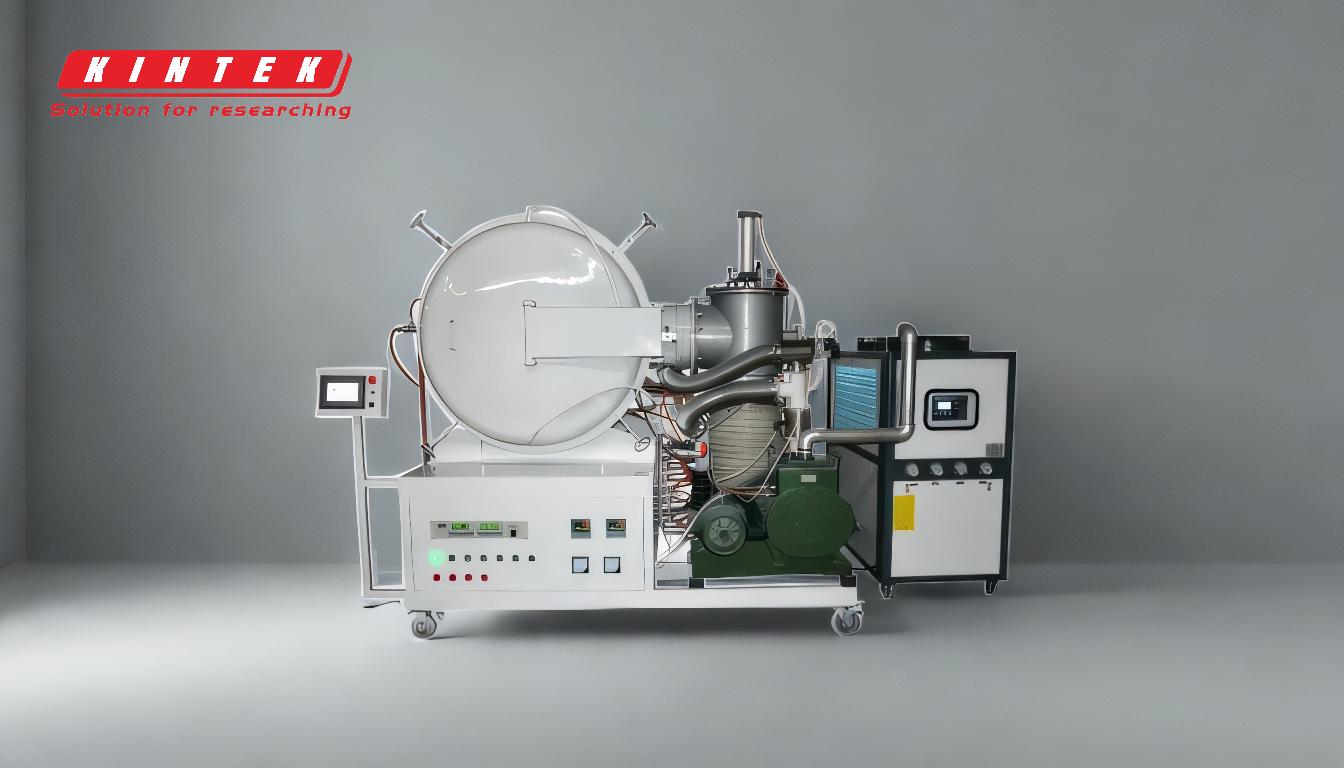
-
Material Properties:
- Type of Material: Induction heating is typically used for metals and conductive materials. The choice of frequency depends on the material's resistivity and magnetic properties. Higher resistivity materials heat faster and may require lower frequencies.
- Resistivity: Materials with higher resistivity generate more heat when subjected to alternating current, influencing the frequency selection.
-
Size and Thickness of the Workpiece:
- Small and Thin Materials: These heat faster and are better suited for higher frequencies, which provide shallow heating depths.
- Large and Thick Materials: These require lower frequencies to achieve deeper heat penetration.
-
Desired Heating Depth:
- Higher Frequencies: Result in lower heating depths, making them ideal for surface heating or thin materials.
- Lower Frequencies: Provide deeper heat penetration, suitable for thicker materials or applications requiring uniform heating throughout the workpiece.
-
Efficiency and Power Supply Capacity:
- Efficiency: The efficiency of the induction heating system depends on the frequency, material properties, and inductor design. Higher frequencies may offer better efficiency for specific applications.
- Power Supply Capacity: The power supply must account for the material's specific heat, mass, required temperature rise, and heat loss. Higher power may be needed for greater temperature variations.
-
Inductor Design:
- Coil and Capacitor Configuration: The design of the inductor coil and compensating capacitor can be adjusted to optimize the frequency for specific applications, such as achieving a desired stirring effect or reducing working noise.
-
Application-Specific Requirements:
- Stirring Effect: Certain applications, like induction melting, may require specific frequencies to achieve a desired stirring effect in the molten material.
- Noise Reduction: Lower frequencies may be chosen to reduce working noise in certain environments.
-
Cost Considerations:
- Purchase Cost: The selection of frequency band should consider the customer's budget. Low-power high-frequency equipment and higher-power ultra-audio equipment may offer similar heating effects for certain workpieces, but at different costs.
- Operational Cost: The operational efficiency and energy consumption of the system should be balanced against the initial purchase cost.
-
Process Requirements:
- Temperature Variation: The degree of temperature variation required in the application influences the choice of frequency. More power may be utilized to achieve wider temperature ranges.
- Heat Loss: Factors such as conduction, convection, and radiation must be considered to minimize heat loss and optimize the heating process.
By carefully evaluating these factors, one can select the most appropriate frequency for an induction heating system, ensuring optimal performance, efficiency, and cost-effectiveness for the specific application.
Summary Table:
Factor | Description |
---|---|
Material Properties | Resistivity and magnetic properties dictate frequency selection. |
Workpiece Size/Thickness | Smaller, thinner materials use higher frequencies; larger, thicker ones use lower. |
Heating Depth | Higher frequencies for shallow heating; lower frequencies for deeper penetration. |
Efficiency | Frequency impacts system efficiency based on material and inductor design. |
Inductor Design | Coil and capacitor configurations optimize frequency for specific applications. |
Application Needs | Stirring effects, noise reduction, and temperature variations influence frequency. |
Cost Considerations | Balance purchase and operational costs with performance requirements. |
Need help selecting the right frequency for your induction heating system? Contact our experts today for tailored solutions!