Pellet properties are influenced by a variety of factors, including raw material composition, processing conditions, and post-processing treatments. These factors collectively determine the physical, chemical, and mechanical characteristics of pellets, such as density, durability, moisture content, and combustion efficiency. Understanding these factors is crucial for optimizing pellet production and ensuring high-quality end products suitable for various applications, including energy generation and animal feed. Below, we delve into the key factors affecting pellet properties, providing a detailed explanation of each.
Key Points Explained:
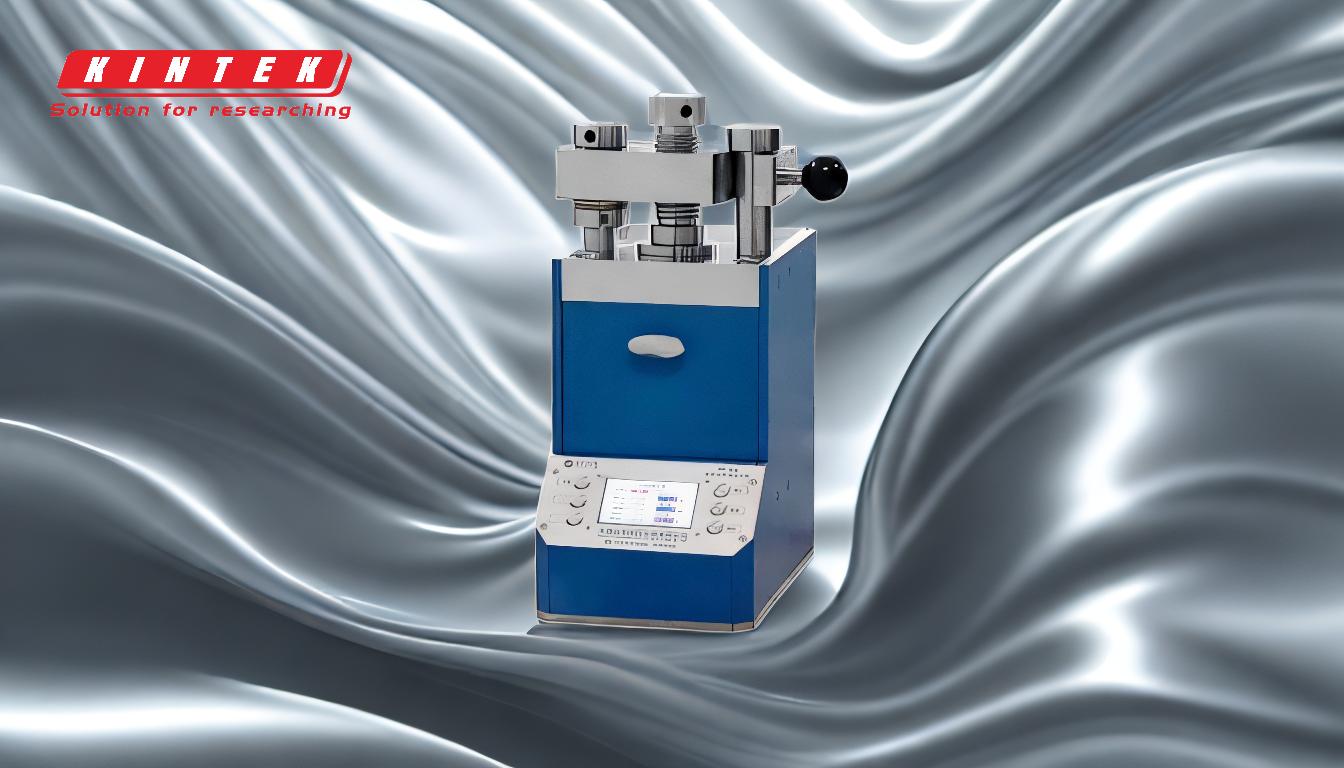
-
Raw Material Composition:
- Type of Biomass: The type of biomass used (e.g., wood, agricultural residues, or industrial waste) significantly impacts pellet properties. For instance, wood pellets typically have higher durability and energy content compared to agricultural residues due to their lignin content.
- Particle Size and Distribution: Smaller and uniformly sized particles enhance pellet density and durability by improving inter-particle bonding during compression.
- Moisture Content: Optimal moisture content (usually 8–12%) is critical for binding particles together. Too much moisture can lead to poor pellet formation, while too little can reduce binding efficiency.
- Chemical Composition: The presence of lignin, cellulose, and hemicellulose affects pellet strength and combustion properties. Lignin acts as a natural binder, while cellulose and hemicellulose influence energy content.
-
Processing Conditions:
- Compression Pressure: Higher compression pressure increases pellet density and durability by forcing particles closer together. However, excessive pressure can lead to equipment wear and energy inefficiency.
- Temperature: Elevated temperatures during pelleting soften lignin, enhancing its binding properties. However, excessively high temperatures can degrade biomass components, reducing pellet quality.
- Die Specifications: The design of the pellet mill die, including its length-to-diameter (L/D) ratio and hole size, affects pellet density and durability. A higher L/D ratio generally produces denser pellets.
- Residence Time: The time biomass spends in the pellet mill influences the degree of particle bonding. Longer residence times can improve pellet quality but may reduce production efficiency.
-
Post-Processing Treatments:
- Cooling: Proper cooling after pelleting stabilizes pellets and reduces moisture content, preventing cracking and improving durability.
- Drying: Drying pellets to the desired moisture level enhances storage stability and combustion efficiency.
- Storage Conditions: Pellets stored in humid environments can absorb moisture, leading to degradation. Proper storage in dry, ventilated areas is essential for maintaining pellet quality.
-
Environmental and External Factors:
- Ambient Humidity: High humidity during production or storage can increase pellet moisture content, reducing their durability and energy content.
- Feedstock Variability: Variations in feedstock composition (e.g., seasonal changes in agricultural residues) can lead to inconsistencies in pellet properties.
- Additives: The use of binders, lubricants, or other additives can improve pellet properties but may also introduce additional costs and environmental considerations.
-
End-Use Requirements:
- Combustion Efficiency: Pellets intended for energy generation must have high calorific value, low ash content, and consistent size to ensure efficient combustion.
- Animal Feed Pellets: For animal feed, pellets must meet specific nutritional and digestibility standards, requiring careful control of raw material composition and processing conditions.
- Transport and Handling: Pellets with high durability and low moisture content are better suited for long-distance transport and handling without degradation.
By carefully controlling these factors, pellet producers can optimize the quality and performance of their products, meeting the diverse needs of end-users across industries. Understanding the interplay between raw materials, processing conditions, and post-processing treatments is essential for achieving consistent and high-quality pellet properties.
Summary Table:
Factor | Key Points |
---|---|
Raw Material Composition | - Type of biomass (e.g., wood, agricultural residues) affects durability and energy content. |
- Particle size, moisture content, and chemical composition (lignin, cellulose) impact pellet strength and combustion. | |
Processing Conditions | - Compression pressure, temperature, die specifications, and residence time influence pellet density and durability. |
Post-Processing Treatments | - Cooling, drying, and proper storage conditions stabilize pellets and prevent degradation. |
Environmental Factors | - Ambient humidity, feedstock variability, and additives can alter pellet properties. |
End-Use Requirements | - Combustion efficiency, animal feed standards, and transport durability dictate pellet quality. |
Optimize your pellet production for superior quality—contact our experts today to learn more!