Shrinkage during sintering is a critical phenomenon that directly impacts the final dimensions and properties of sintered parts. It is influenced by a combination of factors, including the characteristics of the powder particles, compaction parameters, sintering conditions, and post-sintering processes. The composition, size, shape, and distribution of powder particles play a significant role in determining how the material densifies. Compaction pressure and time affect the initial density of the green part, while sintering temperature, heating rate, and duration control the diffusion and bonding of particles. Additionally, the cooling rate and sintering atmosphere influence the final microstructure and properties of the sintered part. Understanding these factors is essential for optimizing the sintering process and achieving the desired product quality.
Key Points Explained:
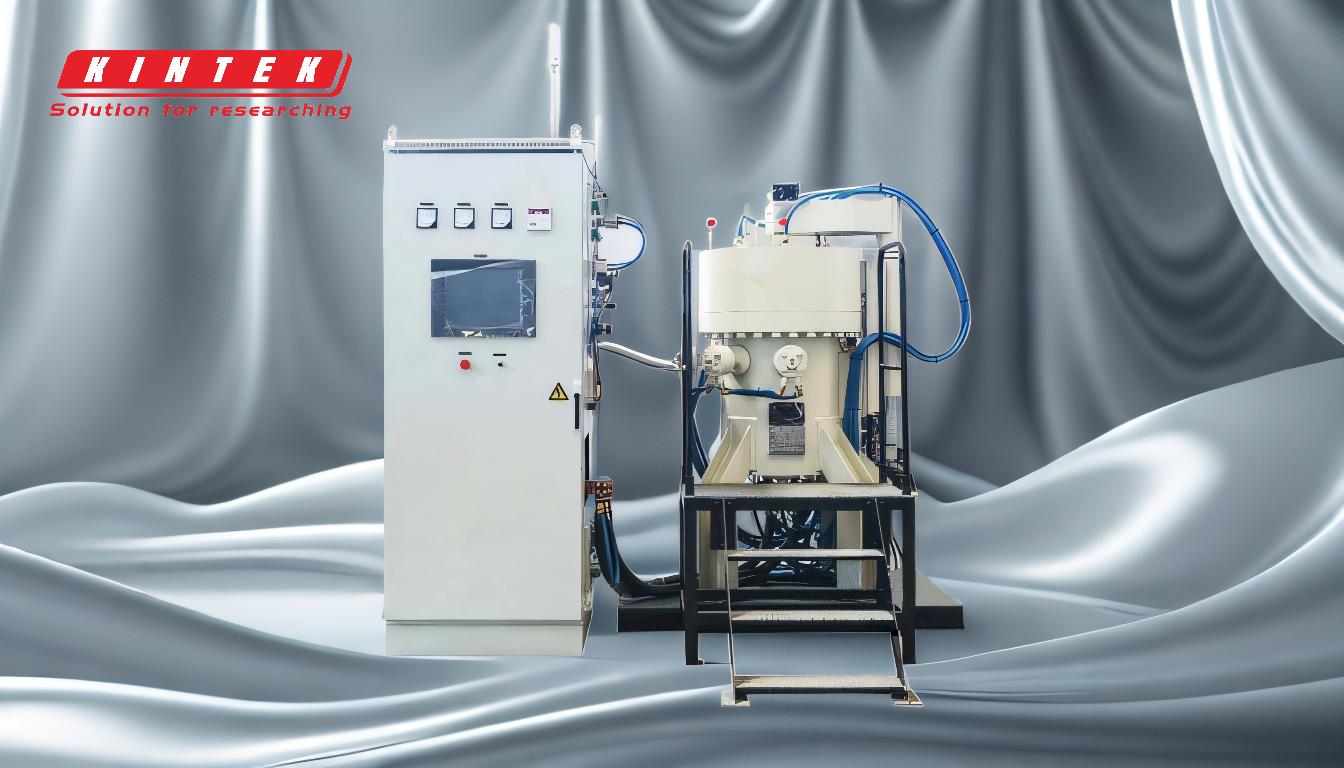
-
Powder Particle Characteristics:
- Composition: The chemical makeup of the powder affects its sintering behavior. Homogeneous compositions tend to promote better densification and uniform shrinkage.
- Size: Smaller particles have a higher surface area-to-volume ratio, which enhances diffusion and bonding during sintering, leading to more pronounced shrinkage.
- Shape and Distribution: Irregularly shaped particles or uneven distribution can lead to non-uniform shrinkage, causing defects such as warping or cracking.
-
Compaction Parameters:
- Pressure: Higher compaction pressure increases the initial density of the green part, reducing porosity and influencing the extent of shrinkage during sintering.
- Time: Longer compaction times allow for better particle rearrangement, which can improve the uniformity of shrinkage.
-
Sintering Conditions:
- Temperature: The sintering temperature determines the kinetics of diffusion and bonding. Higher temperatures generally increase shrinkage but must be carefully controlled to avoid excessive grain growth or melting.
- Heating Rate: A controlled heating rate ensures uniform densification. Rapid heating can lead to uneven shrinkage and defects.
- Duration: Longer sintering times allow for more complete densification but may also lead to grain coarsening, which can affect mechanical properties.
-
Post-Sintering Processes:
- Cooling Rate: The rate at which the part is cooled after sintering can influence the final microstructure and properties. Faster cooling rates may lead to residual stresses, while slower cooling can promote phase transformations.
- Atmosphere: The sintering atmosphere (e.g., inert, reducing, or oxidizing) affects the surface chemistry and diffusion mechanisms, impacting shrinkage and final properties.
-
Other Influencing Factors:
- Gaseous Atmosphere: The presence of gases during sintering can influence the diffusion of atoms and the formation of phases, affecting shrinkage.
- Liquid Phase: If a liquid phase forms during sintering, it can enhance densification but must be carefully controlled to avoid excessive shrinkage or distortion.
By carefully controlling these factors, manufacturers can optimize the sintering process to achieve the desired dimensions, density, and mechanical properties of the final product.
Summary Table:
Factor | Key Points |
---|---|
Powder Particle Characteristics | - Composition: Homogeneous compositions promote uniform shrinkage. |
- Size: Smaller particles enhance diffusion and bonding. | |
- Shape and Distribution: Irregular shapes or uneven distribution cause defects. | |
Compaction Parameters | - Pressure: Higher pressure increases initial density, reducing porosity. |
- Time: Longer compaction improves particle rearrangement and uniformity. | |
Sintering Conditions | - Temperature: Higher temperatures increase shrinkage but risk grain growth. |
- Heating Rate: Controlled rates ensure uniform densification. | |
- Duration: Longer sintering times improve densification but may coarsen grains. | |
Post-Sintering Processes | - Cooling Rate: Affects microstructure and residual stresses. |
- Atmosphere: Inert, reducing, or oxidizing atmospheres impact shrinkage. | |
Other Factors | - Gaseous Atmosphere: Influences diffusion and phase formation. |
- Liquid Phase: Enhances densification but must be controlled to avoid defects. |
Optimize your sintering process today—contact our experts for tailored solutions!