Powder metallurgy is a versatile manufacturing process that involves the production of parts from metal powders. The process is influenced by several factors, including the properties of the metal powders, the requirements of the final part, and the specific techniques used in the process. Key considerations include the flow rate, density, compressibility, and strength of the powders, as well as the mechanical properties of the metals such as corrosion resistance, hardness, tensile strength, impact toughness, and fatigue strength. Additionally, the choice of process—whether conventional methods, injection molding, isostatic pressing, or additive manufacturing—plays a significant role in determining the final product's characteristics. Sintering, a critical step in powder metallurgy, involves heating the parts to bond the powder particles without fully melting them, ensuring the structural integrity of the final part.
Key Points Explained:
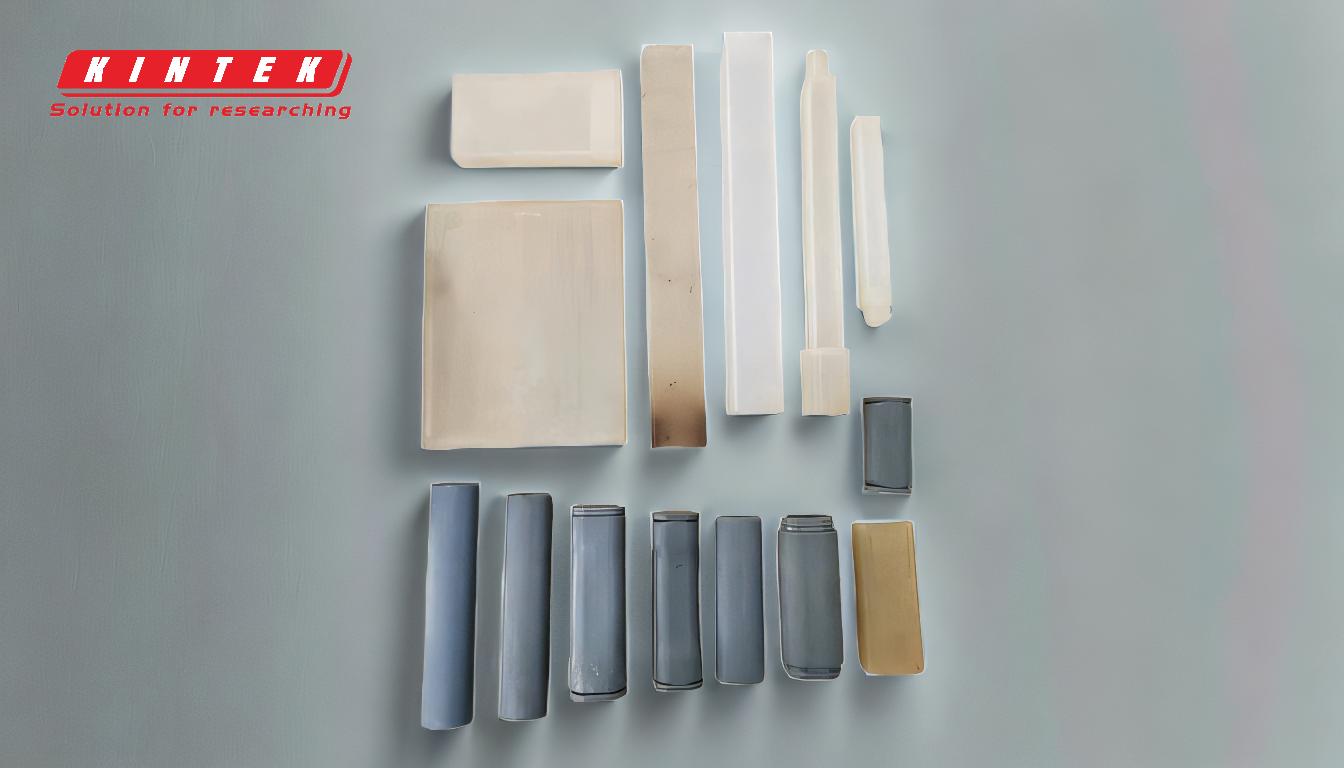
-
Powder Properties:
- Flow Rate: The ability of the powder to flow freely is crucial for uniform filling of molds and dies. Powders with good flow characteristics ensure consistent part density and shape.
- Density: The density of the powder affects the final part's density and mechanical properties. Higher density powders generally lead to stronger parts.
- Compressibility: This refers to how well the powder can be compacted under pressure. High compressibility is desirable for achieving high-density parts with minimal porosity.
- Strength: The inherent strength of the powder particles influences the final part's strength and durability.
-
Metal Selection Criteria:
- Corrosion Resistance: Metals with high corrosion resistance are chosen for parts exposed to harsh environments, such as marine or chemical applications.
- Hardness: Hardness is a critical factor for parts that require wear resistance, such as gears or bearings.
- Tensile Strength: This property is important for parts that must withstand high stress or load-bearing applications.
- Impact Toughness: Metals with good impact toughness are selected for parts that may experience sudden shocks or impacts.
- Fatigue Strength: This is crucial for parts subjected to cyclic loading, such as automotive or aerospace components.
-
Process Variations:
- Conventional Methods: These include pressing and sintering, which are widely used for producing simple to moderately complex parts.
- Injection Molding: Metal injection molding (MIM) allows for the production of complex, high-precision parts with intricate geometries.
- Isostatic Pressing: Hot isostatic pressing (HIP) is used to produce parts with high density and uniform properties, often used in aerospace and medical applications.
- Additive Manufacturing: This is the newest advancement, allowing for the production of highly complex and customized parts with minimal material waste.
-
Sintering Process:
- Temperature Control: Sintering is performed at temperatures slightly below the melting point of the primary metal to ensure that the powder particles bond together without melting.
- Bonding Mechanism: The heat causes the particles to diffuse into one another, creating a solid part with good mechanical properties.
- Final Properties: The sintering process significantly influences the final part's density, strength, and dimensional accuracy.
-
Techniques in Powder Metallurgy:
- Metal Injection Molding (MIM): Combines the flexibility of plastic injection molding with the strength and integrity of metal parts.
- Hot Isostatic Pressing (HIP): Used to eliminate porosity and improve the mechanical properties of parts.
- Additive Manufacturing: Enables the production of complex geometries and customized parts with high precision.
- Spark Plasma Sintering (SPS): A rapid sintering technique that uses electrical pulses to heat the powder, resulting in dense and high-strength parts.
In summary, powder metallurgy is a multifaceted process influenced by the properties of the metal powders, the mechanical requirements of the final part, and the specific techniques employed. Understanding these factors is essential for selecting the right materials and processes to produce high-quality, durable parts.
Summary Table:
Aspect | Key Details |
---|---|
Powder Properties | Flow rate, density, compressibility, and strength influence part quality. |
Metal Selection Criteria | Corrosion resistance, hardness, tensile strength, impact toughness, fatigue strength. |
Process Variations | Conventional, injection molding, isostatic pressing, additive manufacturing. |
Sintering Process | Temperature control, bonding mechanism, and final properties. |
Advanced Techniques | Metal injection molding, hot isostatic pressing, additive manufacturing, SPS. |
Discover how powder metallurgy can enhance your manufacturing process—contact us today for expert guidance!