Additive manufacturing (AM), commonly known as 3D printing, is rapidly evolving, driven by advancements in technology, materials, and applications. The future of AM is shaped by trends such as increased adoption in industrial production, the development of new materials, integration with artificial intelligence (AI) and machine learning, and the expansion of its use in sectors like healthcare, aerospace, and construction. Sustainability and customization are also key drivers, as AM offers solutions for reducing waste and enabling personalized products. These trends are transforming traditional manufacturing processes, making AM a cornerstone of Industry 4.0 and future innovation.
Key Points Explained:
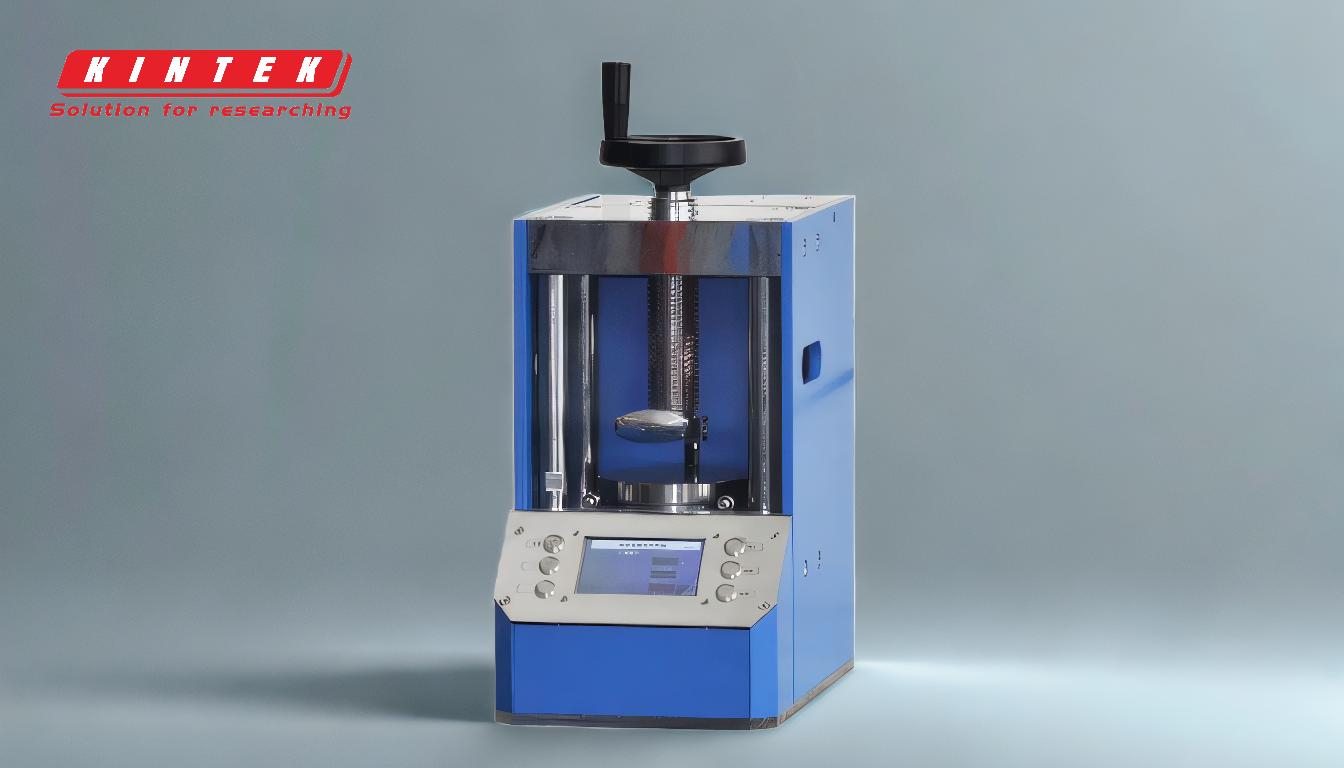
-
Industrial Adoption and Scalability
- Additive manufacturing is transitioning from prototyping to full-scale production. Industries like aerospace, automotive, and healthcare are increasingly adopting AM for end-use parts due to its ability to produce complex geometries and lightweight structures.
- Scalability is a major focus, with advancements in multi-material printing and large-format 3D printers enabling the production of larger and more complex components.
- Companies are investing in AM to reduce lead times, lower costs, and improve supply chain resilience.
-
Material Innovation
- The development of new materials, including high-performance polymers, metal alloys, and biocompatible materials, is expanding the applications of AM.
- Composite materials and nanomaterials are being integrated into AM processes to enhance the mechanical, thermal, and electrical properties of printed parts.
- Research is ongoing into sustainable materials, such as recycled plastics and bio-based polymers, to align AM with environmental goals.
-
Integration of AI and Machine Learning
- AI and machine learning are being integrated into AM systems to optimize design, improve print quality, and reduce errors.
- Predictive analytics and real-time monitoring are enhancing process control, ensuring consistent output and reducing material waste.
- AI-driven generative design tools are enabling the creation of optimized structures that are both lightweight and strong.
-
Sustainability and Circular Economy
- AM supports sustainability by minimizing material waste through precise layer-by-layer fabrication.
- The ability to produce parts on-demand reduces the need for large inventories and long-distance transportation, lowering the carbon footprint.
- AM is being used to create components for renewable energy systems, such as wind turbines and solar panels, contributing to a greener economy.
-
Customization and Personalization
- AM enables mass customization, allowing for the production of personalized products tailored to individual needs.
- In healthcare, this trend is evident in the production of custom prosthetics, implants, and dental devices.
- Consumer goods, such as footwear and eyewear, are also benefiting from AM's ability to create unique designs.
-
Expansion into New Sectors
- Beyond traditional manufacturing, AM is being adopted in sectors like construction, where 3D-printed buildings and infrastructure components are being developed.
- The food industry is exploring AM for creating customized meals and intricate food designs.
- The defense sector is leveraging AM for rapid prototyping and on-site production of spare parts.
-
Advancements in Printing Technologies
- New AM technologies, such as binder jetting, directed energy deposition (DED), and volumetric printing, are expanding the capabilities of 3D printing.
- Hybrid manufacturing, which combines AM with traditional subtractive methods, is gaining traction for producing high-precision parts.
- Continuous improvements in speed, resolution, and reliability are making AM more accessible and cost-effective.
-
Regulatory and Standardization Developments
- As AM becomes more prevalent, there is a growing need for industry standards and regulations to ensure quality and safety.
- Organizations like ASTM International and ISO are working on developing standards for AM materials, processes, and testing methods.
- Regulatory frameworks are being established to address challenges related to intellectual property, certification, and liability.
-
Collaboration and Ecosystem Growth
- The AM ecosystem is expanding through collaborations between manufacturers, material suppliers, software developers, and research institutions.
- Open innovation platforms and partnerships are accelerating the development and adoption of AM technologies.
- Governments and industry consortia are investing in AM research and infrastructure to drive innovation and competitiveness.
-
Education and Workforce Development
- As AM becomes more integral to manufacturing, there is a growing demand for skilled professionals in design, engineering, and operations.
- Educational institutions are incorporating AM into their curricula, offering specialized courses and certifications.
- Workforce training programs are being developed to equip workers with the skills needed to operate and maintain AM systems.
In conclusion, the future of additive manufacturing is bright, with trends like industrial adoption, material innovation, AI integration, and sustainability driving its growth. These advancements are reshaping industries and creating new opportunities for innovation, making AM a key enabler of the next industrial revolution.
Summary Table:
Trend | Key Insights |
---|---|
Industrial Adoption | Transition to full-scale production in aerospace, automotive, and healthcare. |
Material Innovation | Development of high-performance, biocompatible, and sustainable materials. |
AI and Machine Learning | Optimized designs, predictive analytics, and real-time process control. |
Sustainability | Reduced waste, on-demand production, and renewable energy applications. |
Customization | Personalized products in healthcare, consumer goods, and more. |
Expansion into New Sectors | Adoption in construction, food, and defense industries. |
Printing Technology Advances | Binder jetting, DED, volumetric printing, and hybrid manufacturing. |
Regulatory Developments | Industry standards and certifications for quality and safety. |
Collaboration Growth | Partnerships driving innovation in materials, software, and infrastructure. |
Workforce Development | Increased demand for skilled professionals in AM design and operations. |
Ready to embrace the future of additive manufacturing? Contact us today to learn how AM can transform your business!