Copper brazing, while a widely used and effective method for joining metals, comes with several hazards that need to be carefully managed. These hazards can affect both the quality of the brazed joint and the safety of the operator. Key concerns include thermal distortion, uneven temperature distribution, improper braze flow, quench cracking, and splatter. These issues can lead to structural weaknesses, compromised joint integrity, and potential safety risks during the brazing process. Understanding these hazards is crucial for ensuring successful brazing outcomes and maintaining a safe working environment.
Key Points Explained:
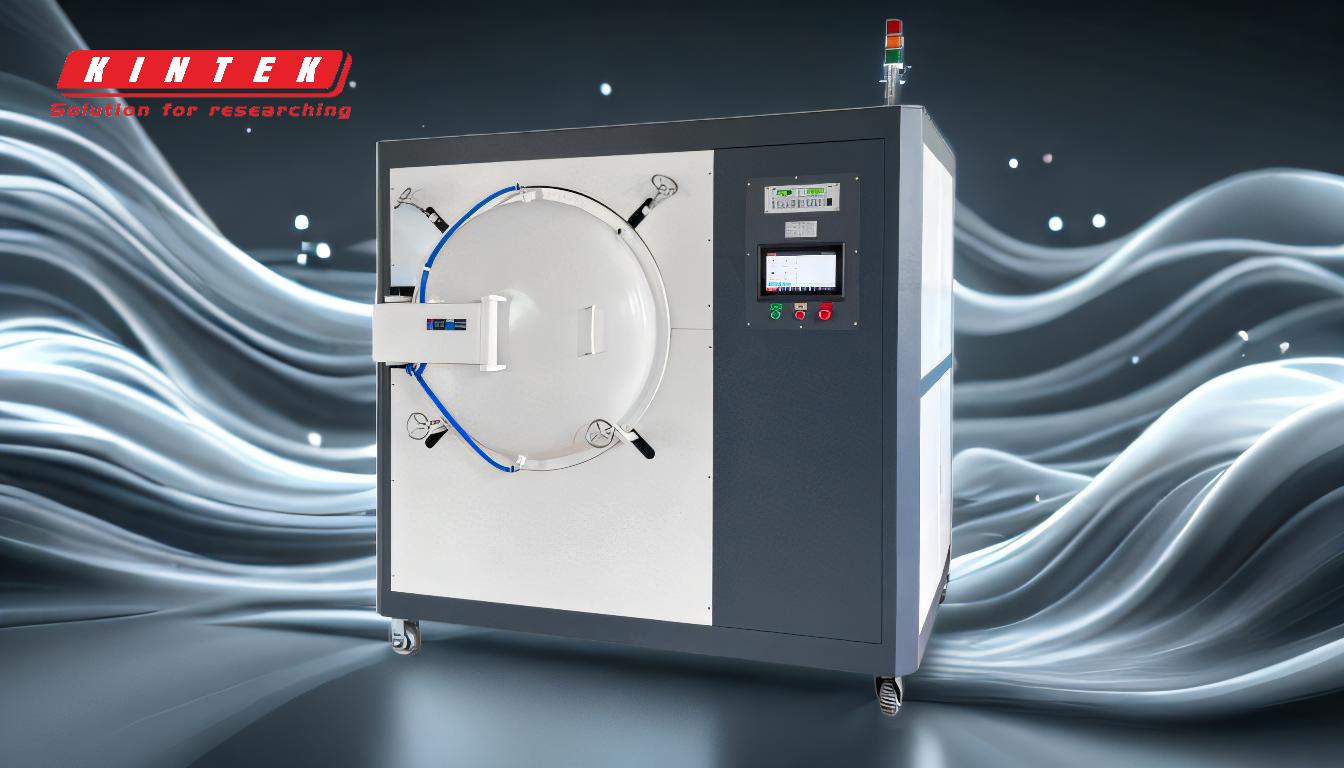
-
Thermal Distortion:
- Cause: Rapid heating or cooling during the brazing process can cause parts to expand or contract unevenly, leading to distortion.
- Impact: Distorted parts may not fit together properly, resulting in poor joint formation and potential failure under stress.
- Prevention: Gradual heating and cooling rates should be employed to minimize thermal shock. Proper fixturing can also help maintain part alignment during the brazing cycle.
-
Uneven Temperature Distribution:
- Cause: Inconsistent heating within the furnace can lead to parts of the assembly reaching different temperatures.
- Impact: Uneven temperatures can cause incomplete braze flow, leading to weak joints or voids in the brazed area.
- Prevention: Ensuring uniform heating by using properly calibrated furnaces and arranging parts to allow even heat distribution is essential.
-
Improper Braze Flow:
- Cause: If parts are not stabilized or if the temperature is not adequately controlled, the brazing filler metal may not flow correctly.
- Impact: Poor braze flow can result in incomplete joint coverage, reducing the strength and reliability of the brazed connection.
- Prevention: Proper temperature control and stabilization of parts before brazing are critical. Using the correct brazing alloy and flux can also improve flow characteristics.
-
Quench Cracking:
- Cause: Rapid cooling (quenching) after brazing can introduce thermal stresses that lead to cracking in the braze joint.
- Impact: Cracks can compromise the structural integrity of the joint, leading to potential failure under load.
- Prevention: Controlled cooling rates and the use of appropriate quenching media can help mitigate the risk of quench cracking.
-
Splatter:
- Cause: Rapid heating or cooling can cause the brazing filler metal to splatter, especially if the assembly is not properly stabilized.
- Impact: Splatter can lead to contamination of the brazing area, poor joint formation, and potential safety hazards for the operator.
- Prevention: Ensuring that parts are properly fixtured and that heating and cooling rates are controlled can reduce the likelihood of splatter.
By understanding and addressing these hazards, operators can improve the quality and reliability of copper brazed joints while maintaining a safe working environment. Proper process control, equipment calibration, and operator training are essential components of successful brazing operations.
Summary Table:
Hazard | Cause | Impact | Prevention |
---|---|---|---|
Thermal Distortion | Rapid heating or cooling causing uneven expansion/contraction. | Poor joint formation, potential failure under stress. | Gradual heating/cooling, proper fixturing. |
Uneven Temp. Distribution | Inconsistent heating in the furnace. | Incomplete braze flow, weak joints or voids. | Uniform heating, proper furnace calibration, and part arrangement. |
Improper Braze Flow | Unstable parts or inadequate temperature control. | Incomplete joint coverage, reduced strength. | Proper temperature control, stabilization, and correct brazing alloy/flux. |
Quench Cracking | Rapid cooling causing thermal stresses. | Cracks compromising joint integrity. | Controlled cooling rates, appropriate quenching media. |
Splatter | Rapid heating/cooling or improper stabilization. | Contamination, poor joint formation, safety hazards. | Proper fixturing and controlled heating/cooling rates. |
Ensure safe and effective copper brazing—contact our experts today for tailored solutions and support!