Molten metals pose significant hazards due to their high temperatures, chemical reactivity, and physical properties. These hazards can lead to severe injuries, environmental damage, and equipment failure if proper safety measures are not followed. Understanding the risks associated with molten metals is crucial for ensuring workplace safety and preventing accidents. Key hazards include burns, explosions, toxic fumes, and structural failures. This answer explores these risks in detail, providing a comprehensive overview of the dangers and how to mitigate them.
Key Points Explained:
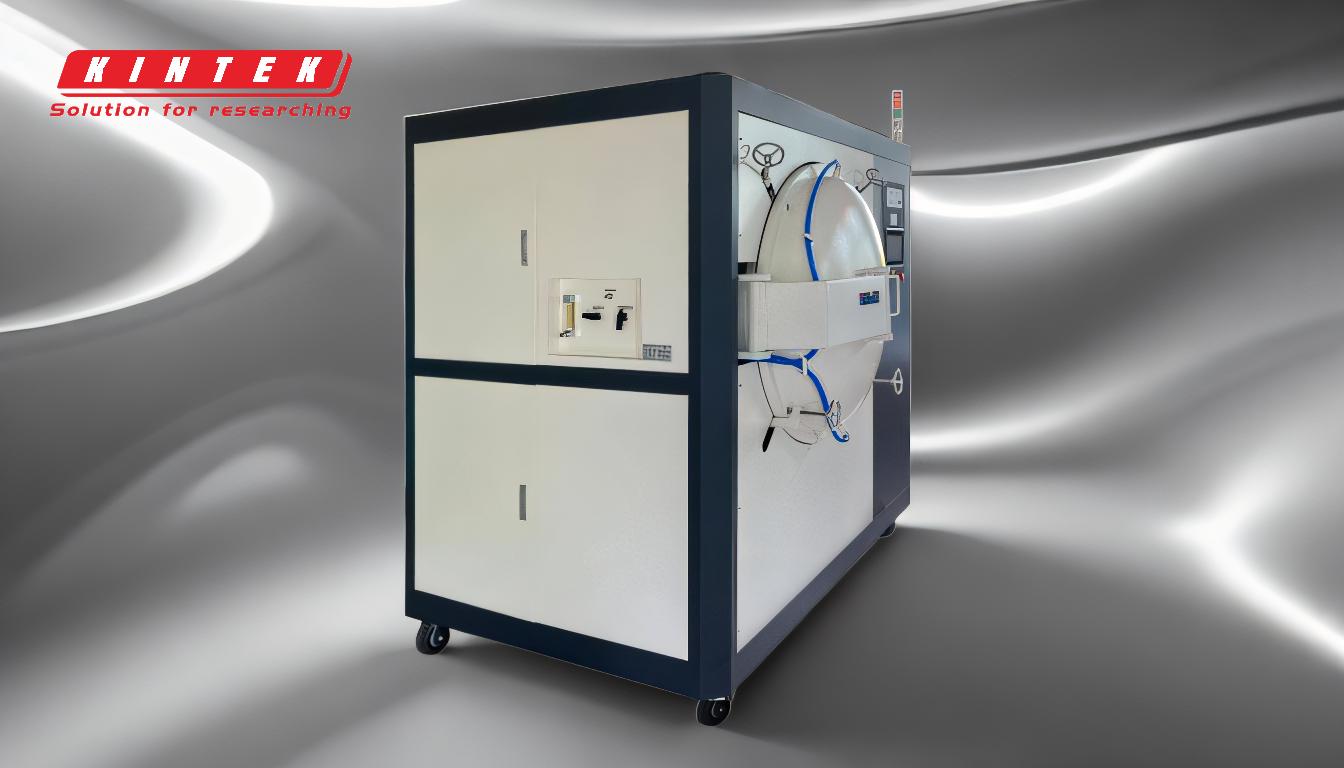
-
Thermal Burns and Injuries:
- Molten metals are typically heated to extremely high temperatures, often exceeding 1000°C. Contact with molten metal can cause severe burns, which may penetrate deep into the skin and underlying tissues.
- Splashes or spills of molten metal can result in catastrophic injuries, especially if protective gear is not worn. Proper personal protective equipment (PPE), such as heat-resistant gloves, aprons, and face shields, is essential to minimize the risk of burns.
-
Explosion Risks:
- Molten metals can react violently with water or moisture, leading to steam explosions. When water comes into contact with molten metal, it rapidly vaporizes, causing a sudden expansion of steam that can propel molten metal and debris at high speeds.
- To prevent explosions, it is critical to ensure that all equipment and materials are dry before coming into contact with molten metals. Additionally, proper ventilation and containment measures should be in place to manage any potential reactions.
-
Toxic Fumes and Airborne Contaminants:
- Heating metals to high temperatures can release toxic fumes, such as metal oxides, which can be harmful if inhaled. For example, molten aluminum can produce aluminum oxide fumes, which are hazardous to respiratory health.
- Proper ventilation systems and respiratory protection are necessary to reduce exposure to these fumes. Workers should also be trained to recognize the signs of fume exposure and take appropriate action.
-
Structural Failures and Equipment Damage:
- The extreme heat of molten metals can cause structural failures in equipment, such as crucibles, ladles, and furnaces. Over time, thermal stress can weaken materials, leading to cracks or breaks that may result in spills or leaks.
- Regular inspection and maintenance of equipment are essential to prevent failures. Using materials that can withstand high temperatures and thermal cycling is also critical for ensuring safety.
-
Chemical Reactions and Fire Hazards:
- Molten metals can react with other substances, such as acids or oxidizing agents, leading to fires or chemical burns. For instance, molten magnesium is highly reactive and can ignite in the presence of air or water.
- Proper storage and handling of reactive metals are necessary to prevent accidents. Fire suppression systems and emergency response plans should be in place to address any incidents that may occur.
-
Environmental Hazards:
- Spills or leaks of molten metal can cause environmental damage, contaminating soil and water sources. The high temperatures of molten metals can also ignite surrounding materials, leading to fires that may spread rapidly.
- Containment measures, such as spill trays and barriers, should be implemented to prevent environmental contamination. Emergency response plans should include procedures for containing and cleaning up spills.
By understanding these hazards and implementing appropriate safety measures, the risks associated with molten metals can be effectively managed. Training, proper equipment, and adherence to safety protocols are essential for protecting workers and minimizing the potential for accidents.
Summary Table:
Hazard | Description | Prevention Measures |
---|---|---|
Thermal Burns and Injuries | Severe burns from contact with molten metals exceeding 1000°C. | Use heat-resistant PPE (gloves, aprons, face shields). |
Explosion Risks | Steam explosions caused by water or moisture contact with molten metals. | Ensure dry equipment and materials; implement proper ventilation and containment. |
Toxic Fumes | Harmful fumes like metal oxides released during heating. | Install ventilation systems; provide respiratory protection and worker training. |
Structural Failures | Equipment damage due to extreme heat and thermal stress. | Regular inspections; use high-temperature-resistant materials. |
Chemical Reactions | Fires or chemical burns from reactions with acids or oxidizing agents. | Proper storage and handling; fire suppression systems and emergency plans. |
Environmental Hazards | Soil and water contamination from spills; risk of igniting surrounding materials. | Use spill trays and barriers; implement emergency cleanup procedures. |
Ensure workplace safety with expert guidance on handling molten metals—contact us today for tailored solutions!