Heating elements in a vacuum furnace are critical components that determine the furnace's operational efficiency and temperature range. These elements are typically made from materials that can withstand high temperatures and resist oxidation in a vacuum environment. Common materials include nickel-chromium alloys for lower temperatures, molybdenum and tungsten for higher temperatures, and graphite for very high temperatures. The choice of material depends on the specific temperature requirements and the design of the furnace. Understanding the properties and applications of these materials is essential for selecting the appropriate heating element for a vacuum furnace.
Key Points Explained:
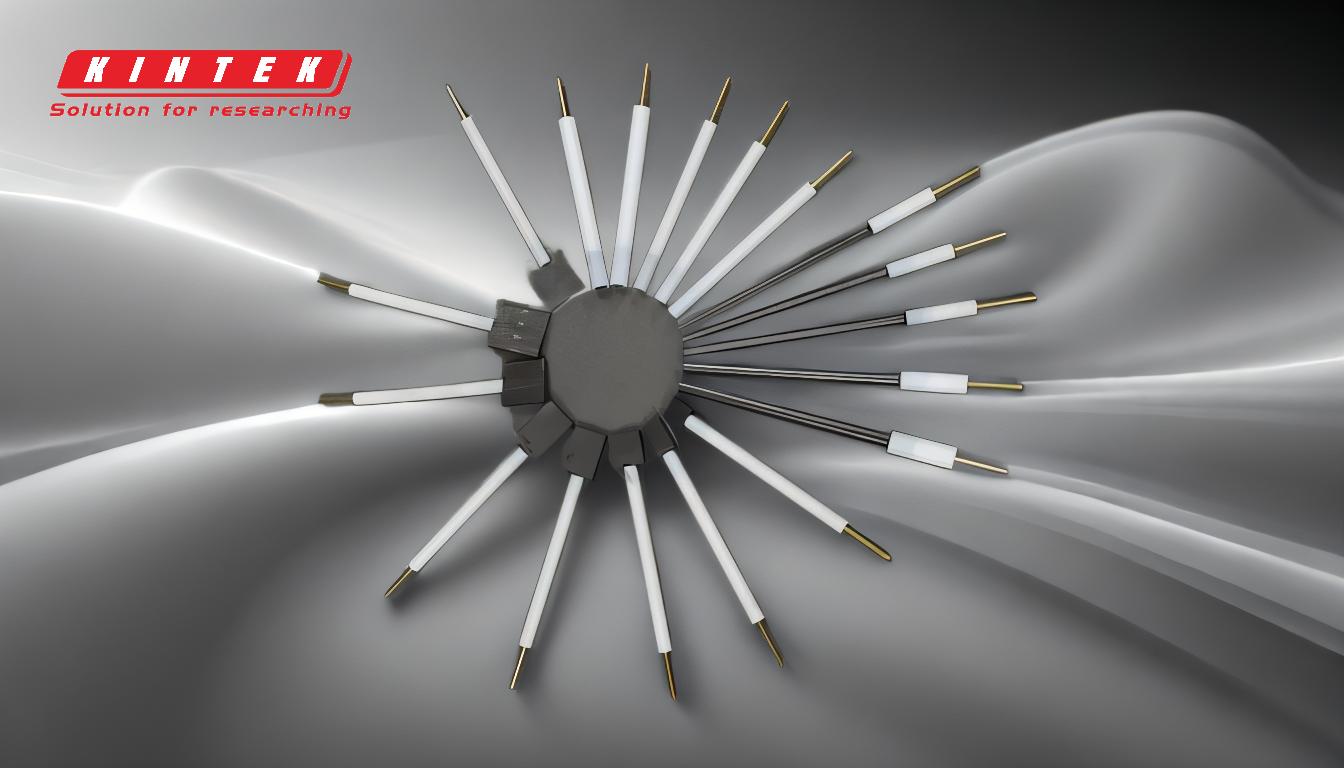
-
Materials Used in Heating Elements:
- Nickel-Chromium Alloys: These are commonly used for low to medium temperature applications, typically not exceeding 1000°C. They are known for their good resistance to oxidation and high electrical resistance.
- Molybdenum and Tungsten: These metals are suitable for higher temperature applications, often used in furnaces that operate above 1200°C. They have high melting points and excellent thermal conductivity.
- Graphite: Graphite is used for very high temperature applications, capable of withstanding temperatures up to 2200°C. It is also resistant to thermal shock and has good electrical conductivity.
- Tantalum: This refractory metal is used in extreme high-temperature environments due to its very high melting point and resistance to corrosion.
-
Types of Heating Elements:
- Resistance Wire: Often made from nickel-chromium or iron-chromium-aluminum alloys, used in lower temperature furnaces.
- Silicon Carbide Rods: These can operate at very high temperatures and are known for their durability and resistance to thermal shock.
- Molybdenum Wire and Rods: These are used in high-temperature vacuum furnaces due to their high melting points and strength at elevated temperatures.
- Graphite Elements: Used in the highest temperature ranges, graphite elements are favored for their thermal and electrical properties.
- Induction Coils: These are used in induction heating applications within vacuum furnaces, providing precise and localized heating.
-
Temperature Ranges:
- Low to Medium Temperature (up to 1000°C): Nickel-chromium and iron-chromium-aluminum alloys are typically used.
- High Temperature (above 1200°C): Molybdenum, tungsten, and graphite are preferred due to their higher melting points and thermal stability.
- Very High Temperature (up to 2200°C): Graphite and tantalum are used for their exceptional high-temperature performance.
-
Selection Criteria:
- Operating Temperature: The primary factor in selecting a heating element material is the maximum operating temperature of the furnace.
- Thermal Conductivity: Materials with high thermal conductivity are preferred for efficient heat transfer.
- Resistance to Oxidation: In a vacuum environment, resistance to oxidation is crucial to prevent degradation of the heating element.
- Mechanical Strength: The material must maintain its structural integrity at high temperatures.
-
Applications:
- Industrial Processes: Vacuum furnaces with various heating elements are used in processes like annealing, brazing, sintering, and heat treatment.
- Research and Development: High-temperature vacuum furnaces are essential in material science research for developing new alloys and materials.
Understanding the different types of electric heating elements and their properties is crucial for optimizing the performance of a vacuum furnace. The selection of the right heating element material and type ensures efficient operation, longevity, and reliability of the furnace in various industrial and research applications.
Summary Table:
Aspect | Details |
---|---|
Materials | Nickel-Chromium Alloys, Molybdenum, Tungsten, Graphite, Tantalum |
Types | Resistance Wire, Silicon Carbide Rods, Molybdenum Wire, Graphite Elements, Induction Coils |
Temperature Ranges | Low-Medium (up to 1000°C), High (above 1200°C), Very High (up to 2200°C) |
Selection Criteria | Operating Temperature, Thermal Conductivity, Oxidation Resistance, Mechanical Strength |
Applications | Annealing, Brazing, Sintering, Heat Treatment, Material Science Research |
Need help selecting the right heating elements for your vacuum furnace? Contact our experts today!