Vacuum casting, while a versatile and widely used manufacturing process, has several limitations that can impact its efficiency, cost, and the quality of the final product. These limitations stem from material properties, process constraints, and operational challenges. Key issues include shrinkage and porosity in cast components, the high cost and wear of mold materials, time-intensive cooling processes, difficulty in maintaining tight dimensional tolerances, and inefficiencies in furnace operations. These factors can collectively affect the mechanical properties, reliability, and economic viability of vacuum-cast parts.
Key Points Explained:
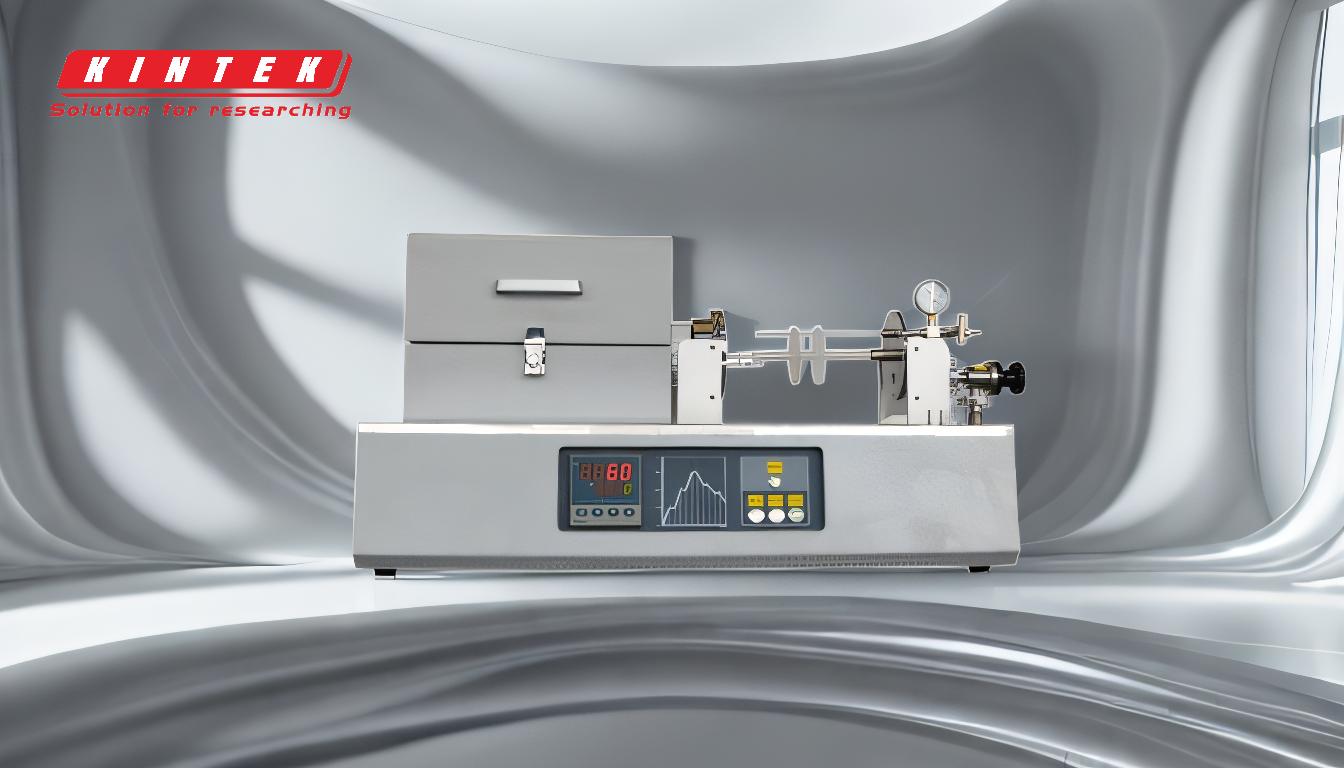
-
Shrinkage and Porosity in Cast Components:
- Explanation: During the solidification of metal in vacuum casting, shrinkage is an inherent property that can lead to defects such as residual shrinkage or gas porosity. These defects can compromise the mechanical properties of the cast parts, particularly their impact resistance and fatigue properties.
- Impact: This limitation is critical in applications where high reliability and performance are required, such as in aerospace components. The presence of porosity can also necessitate additional quality control measures and post-processing to ensure the integrity of the cast parts.
-
Challenges with Mold Materials:
- Explanation: The vacuum hot pressing method, a common technique in vacuum casting, often involves high temperatures and reactive environments that can degrade mold materials. This leads to significant die loss and necessitates the use of high-quality, often expensive, mold materials that can withstand these harsh conditions.
- Impact: The need for durable mold materials increases the overall cost of the casting process. Additionally, the wear and tear on molds can lead to more frequent replacements, further driving up costs and potentially causing delays in production.
-
Time-Intensive Cooling Process:
- Explanation: The cooling process in vacuum casting is inherently slow to ensure that the metal solidifies uniformly and to minimize defects. This slow cooling can be a bottleneck in the manufacturing process, especially when rapid production cycles are required.
- Impact: The extended cooling times can lead to longer lead times and reduced throughput, affecting the overall efficiency and cost-effectiveness of the manufacturing process.
-
Difficulty in Maintaining Tight Dimensional Tolerances:
- Explanation: Achieving precise dimensional tolerances in vacuum casting can be challenging due to the nature of the casting process and the behavior of materials during solidification. Variations in cooling rates and material properties can lead to deviations from the desired dimensions.
- Impact: This limitation may require additional machining or finishing processes to achieve the required specifications, adding to the cost and complexity of production. It is particularly problematic in industries where precision is paramount, such as in medical devices or precision engineering.
-
Inefficiencies in Furnace Operations:
- Explanation: Modern vacuum casting furnaces often require tilting and frequent mold changes, which can lead to material wastage and increased manufacturing time. These operational inefficiencies can be a significant drawback in high-volume production environments.
- Impact: The need for continuous tilting and mold changes not only slows down the production process but also increases the risk of errors and inconsistencies. This can lead to higher scrap rates and reduced overall productivity.
In summary, while vacuum casting offers numerous advantages, including the ability to produce complex shapes and high-quality surfaces, it is not without its limitations. These limitations—ranging from material shrinkage and mold wear to operational inefficiencies—must be carefully managed to ensure the economic and functional viability of the casting process. Manufacturers must weigh these factors against the specific requirements of their applications to determine the suitability of vacuum casting for their needs.
Summary Table:
Limitation | Explanation | Impact |
---|---|---|
Shrinkage and Porosity | Inherent shrinkage during solidification causes defects like porosity. | Compromises mechanical properties, requires additional QC and post-processing. |
High Cost and Wear of Mold Materials | High temperatures degrade molds, requiring expensive, durable materials. | Increases costs and production delays due to frequent mold replacements. |
Time-Intensive Cooling Process | Slow cooling ensures uniform solidification but delays production. | Reduces throughput and efficiency, leading to longer lead times. |
Difficulty in Dimensional Tolerances | Variations in cooling rates and material properties affect precision. | Requires additional machining, increasing costs and complexity. |
Inefficiencies in Furnace Operations | Frequent tilting and mold changes cause material wastage and production delays. | Slows production, increases scrap rates, and reduces overall productivity. |
Need help optimizing your vacuum casting process? Contact our experts today to find solutions tailored to your needs!