The refractory lining of kilns is a critical component designed to withstand high temperatures, provide thermal insulation, and protect the kiln structure. The materials used in these linings vary depending on the specific application and process requirements. Common materials include high-strength alumina, silicon carbide, high-purity alumina fiber, vacuum-formed fiber materials, light hollow aluminum oxide plates, and specialized bricks like low-iron alumina, magnesium-spinel, and magnesite. These materials are chosen for their ability to offer high service temperatures, rapid heat and cold resistance, low heat storage, and excellent thermal insulation, ensuring efficient and durable kiln operation.
Key Points Explained:
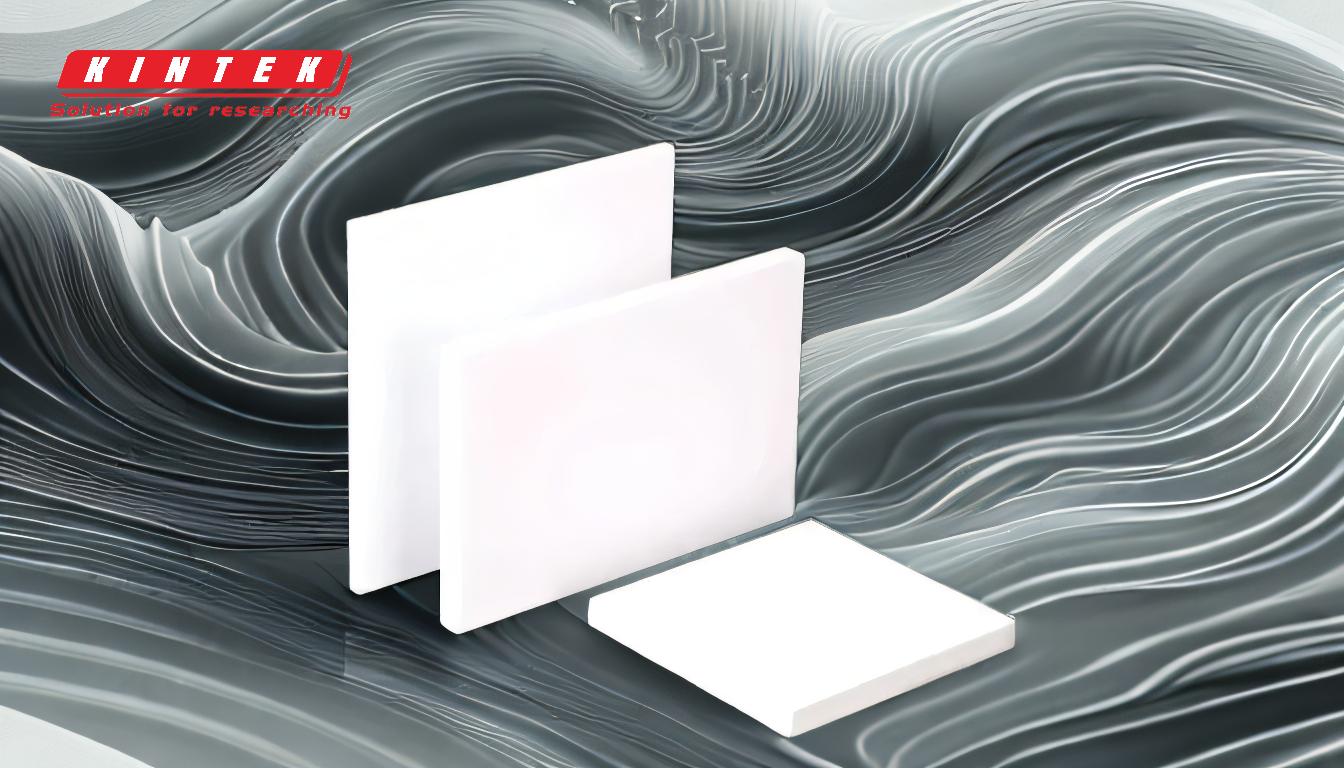
-
High-Strength Alumina (Al₂O₃):
- High-strength alumina is a widely used material in refractory linings due to its excellent thermal stability, mechanical strength, and resistance to chemical corrosion.
- It is particularly effective in muffle furnaces, where it ensures accurate and uniform process conditions by maintaining consistent temperatures.
- Alumina's high melting point (over 2000°C) makes it suitable for applications involving extreme heat.
-
Silicon Carbide (SiC):
- Silicon carbide is another key material used in refractory linings, especially in insulating firebricks.
- It offers superior thermal conductivity, high thermal shock resistance, and excellent mechanical strength, making it ideal for kilns that experience rapid temperature changes.
- SiC is often used in combination with other materials to enhance the overall performance of the refractory lining.
-
High-Purity Alumina Fiber:
- High-purity alumina fiber is a lightweight, high-temperature-resistant material used in kiln linings.
- It provides excellent thermal insulation, reduces heat storage capacity, and allows for rapid heating and cooling without cracking or slagging.
- This material is often used in vacuum-formed fiber linings, which are known for their durability and efficiency.
-
Vacuum-Formed Fiber Materials:
- These materials are created by forming fibers under vacuum conditions, resulting in a lightweight, highly insulating refractory lining.
- They are composed of high-purity alumina fibers and other components, offering a combination of high service temperature and low heat loss.
- Vacuum-formed linings are particularly effective in reducing energy consumption and improving kiln efficiency.
-
Light Hollow Aluminum Oxide Plates:
- Light hollow aluminum oxide plates are used in kiln linings for their excellent thermal insulation properties and low heat storage capacity.
- These plates are designed to withstand high temperatures and rapid thermal cycling without cracking or degrading.
- They are often used in multi-layer insulation designs to enhance the overall thermal performance of the kiln.
-
Specialized Bricks (Low-Iron Alumina, Magnesium-Spinel, Magnesite):
- The choice of specialized bricks depends on the specific process carried out in the kiln. For example:
- Low-Iron Alumina Bricks: Used in iron ore reduction kilns due to their high purity and resistance to chemical attack.
- Magnesium-Spinel Bricks: Known for their excellent thermal shock resistance and high-temperature stability, making them suitable for harsh environments.
- Magnesite Bricks: Commonly used in cement kilns for their ability to withstand high temperatures and chemical corrosion.
- The choice of specialized bricks depends on the specific process carried out in the kiln. For example:
-
Multi-Layer Insulation Design:
- Refractory linings often employ a multi-layer insulation design, combining lightweight alumina ceramic fiber with high-quality insulation board backing.
- This design ensures low heat loss, low energy consumption, and improved thermal efficiency.
- The absence of asbestos components in these designs makes them safer and more environmentally friendly.
-
Functional Benefits of Refractory Linings:
- Thermal Insulation: Refractory materials provide excellent insulation, reducing heat loss and improving energy efficiency.
- Mechanical Protection: They protect the kiln shell from high temperatures and mechanical wear, extending the lifespan of the kiln.
- Chemical Resistance: Refractory linings resist chemical reactions with the materials being processed, ensuring consistent performance.
- Thermal Shock Resistance: Materials like silicon carbide and high-purity alumina fiber can withstand rapid temperature changes without cracking or degrading.
By carefully selecting and combining these materials, kiln manufacturers can create refractory linings that meet the specific needs of their processes, ensuring optimal performance, durability, and efficiency.
Summary Table:
Material | Key Properties | Applications |
---|---|---|
High-Strength Alumina | Thermal stability, mechanical strength, chemical corrosion resistance | Muffle furnaces, extreme heat environments |
Silicon Carbide | Thermal conductivity, thermal shock resistance, mechanical strength | Kilns with rapid temperature changes |
High-Purity Alumina Fiber | Lightweight, high-temperature resistance, thermal insulation | Vacuum-formed fiber linings |
Vacuum-Formed Fiber | Lightweight, high insulation, low heat loss | Energy-efficient kiln linings |
Light Hollow Aluminum Oxide Plates | Thermal insulation, low heat storage, rapid thermal cycling resistance | Multi-layer insulation designs |
Specialized Bricks | High purity, chemical resistance, thermal shock resistance | Iron ore reduction, cement kilns, harsh environments |
Optimize your kiln's performance with the right refractory lining—contact our experts today!