Chemical vapor deposition (CVD) is a versatile and widely used technique for depositing thin films and coatings onto substrates. The process involves several key steps, including the transport of gaseous reactants to the substrate, adsorption, surface reactions, and the removal of by-products. CVD methods vary based on the specific mechanisms and conditions used to achieve deposition, such as thermal activation, plasma enhancement, or laser-assisted processes. Understanding these methods is crucial for selecting the appropriate technique for specific applications, such as semiconductor manufacturing, protective coatings, or nanotechnology.
Key Points Explained:
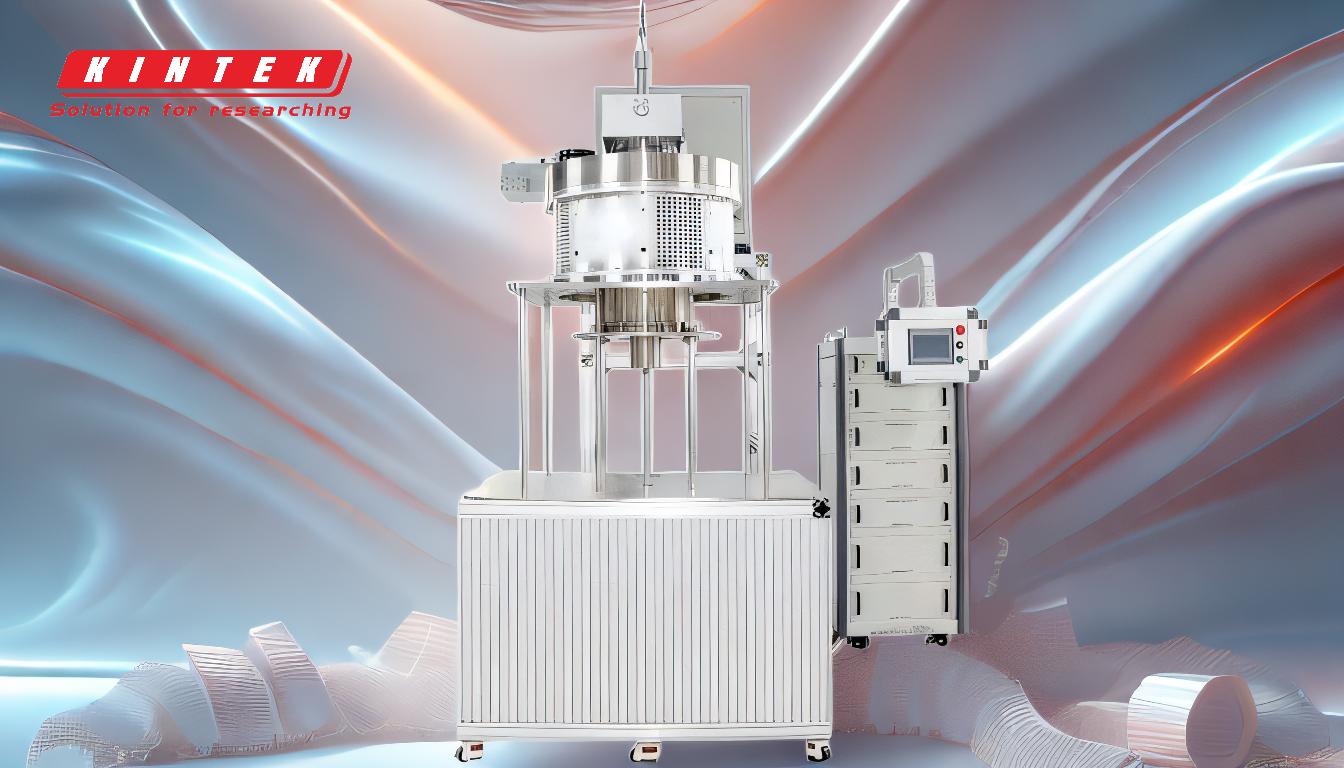
-
Transport of Reactants to the Substrate:
- In CVD, gaseous reactants are transported to the substrate surface through convection or diffusion. This step ensures that the reactants reach the reaction zone where deposition occurs.
- The efficiency of this step depends on factors like gas flow rates, pressure, and the geometry of the reaction chamber.
-
Adsorption of Reactants on the Substrate:
- Once the reactants reach the substrate, they adsorb onto its surface. This adsorption can be physical or chemical, depending on the nature of the reactants and the substrate.
- Adsorption is a critical step because it determines the availability of reactants for subsequent surface reactions.
-
Surface Reactions and Film Formation:
- Heterogeneous surface-catalyzed reactions occur at the substrate, leading to the formation of a solid film. These reactions can involve decomposition, reduction, or chemical reactions between the adsorbed species.
- The film grows as atoms or molecules from the reactants are incorporated into the solid structure.
-
Desorption and Removal of By-products:
- Volatile by-products formed during the surface reactions desorb from the substrate and are transported away from the reaction zone.
- Efficient removal of by-products is essential to prevent contamination and ensure the quality of the deposited film.
-
Types of CVD Methods:
- Thermal CVD: Relies on heat to activate the chemical reactions. It is widely used for depositing materials like silicon dioxide and silicon nitride.
- Plasma-Enhanced CVD (PECVD): Uses plasma to lower the reaction temperature, making it suitable for temperature-sensitive substrates.
- Low-Pressure CVD (LPCVD): Operates at reduced pressures to improve film uniformity and reduce unwanted gas-phase reactions.
- Metal-Organic CVD (MOCVD): Utilizes metal-organic precursors for depositing compound semiconductors like gallium nitride.
- Atomic Layer Deposition (ALD): A variant of CVD that allows precise control over film thickness by alternating the introduction of reactants.
-
Applications of CVD:
- CVD is used in various industries, including electronics (for semiconductor devices), optics (for anti-reflective coatings), and materials science (for protective coatings).
- The choice of CVD method depends on the desired film properties, substrate material, and application requirements.
By understanding these key points, one can appreciate the complexity and versatility of CVD methods and their importance in modern technology and manufacturing.
Summary Table:
CVD Method | Key Features | Applications |
---|---|---|
Thermal CVD | Uses heat to activate reactions; high-temperature process. | Silicon dioxide, silicon nitride deposition. |
Plasma-Enhanced CVD | Lowers reaction temperature using plasma; ideal for temperature-sensitive substrates. | Semiconductor devices, protective coatings. |
Low-Pressure CVD | Operates at reduced pressures for uniform films and fewer gas-phase reactions. | High-quality thin films in electronics. |
Metal-Organic CVD | Uses metal-organic precursors for compound semiconductors. | Gallium nitride, LED manufacturing. |
Atomic Layer Deposition | Precise control over film thickness; alternates reactant introduction. | Nanotechnology, advanced semiconductor devices. |
Discover the right CVD method for your application—contact our experts today!