Graphene synthesis methods can be broadly categorized into two main approaches: top-down and bottom-up methods. The top-down methods involve breaking down graphite or graphite derivatives into graphene layers, while bottom-up methods build graphene from carbon atoms or molecules. Each method has its unique advantages and limitations, making them suitable for different applications. Mechanical exfoliation, chemical vapor deposition (CVD), and reduction of graphene oxide (GO) are among the most widely used techniques. The choice of method depends on factors such as the desired graphene quality, scalability, and application requirements.
Key Points Explained:
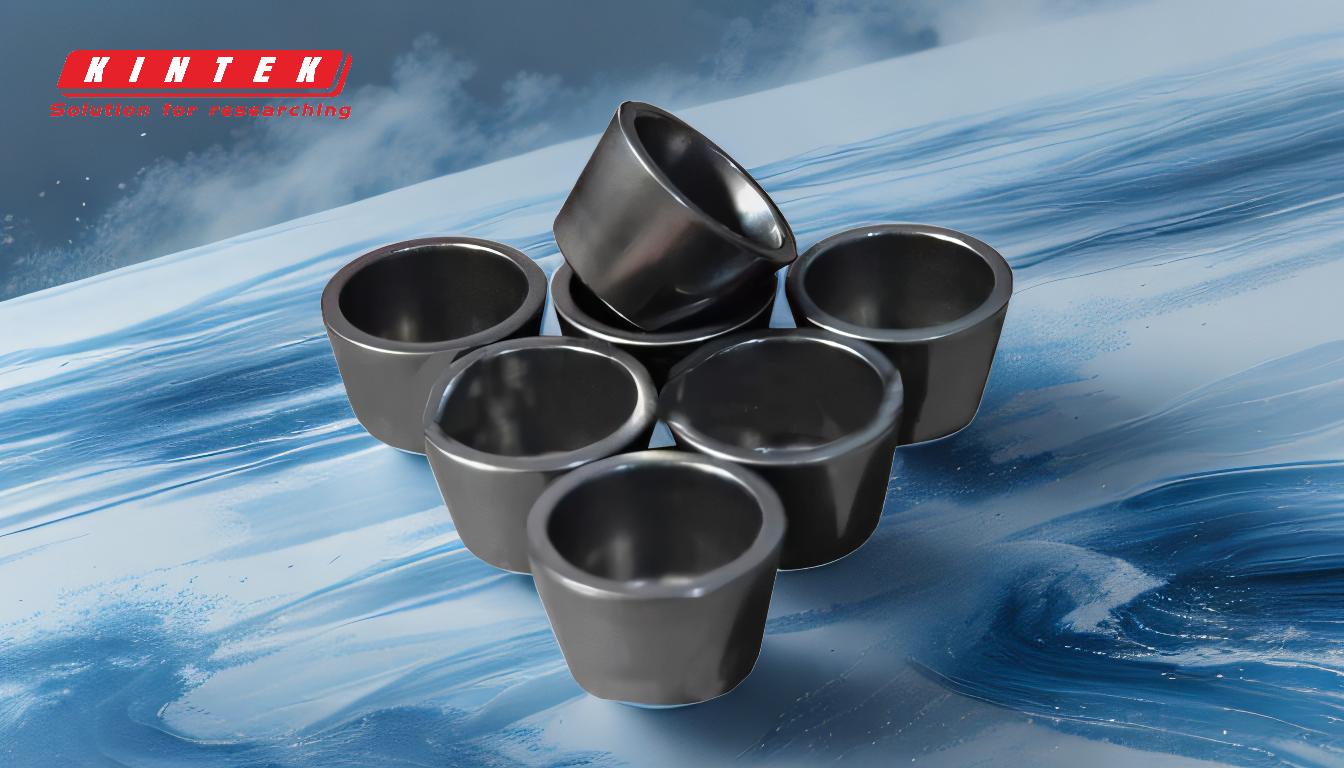
-
Top-Down Methods
-
Mechanical Exfoliation:
- This method involves peeling off graphene layers from graphite using adhesive tape or other mechanical means.
- Advantages: Produces high-quality graphene with minimal defects, ideal for fundamental research.
- Disadvantages: Not scalable, low yield, and unsuitable for industrial applications.
-
Chemical Oxidation and Reduction of Graphene Oxide (GO):
- Graphite is oxidized to produce graphene oxide, which is then chemically reduced to obtain graphene.
- Advantages: Scalable and cost-effective for producing graphene in large quantities.
- Disadvantages: Graphene produced often contains defects and impurities, reducing its electrical and mechanical properties.
-
Liquid-Phase Exfoliation:
- Graphite is exfoliated in a liquid medium using sonication or shear forces.
- Advantages: Suitable for mass production and compatible with solution-based processing.
- Disadvantages: Graphene quality is lower compared to mechanical exfoliation, with issues like aggregation and incomplete exfoliation.
-
-
Bottom-Up Methods
-
Chemical Vapor Deposition (CVD):
- Graphene is grown on a substrate (e.g., copper or nickel) by decomposing carbon-containing gases at high temperatures.
- Advantages: Produces large-area, high-quality graphene with excellent electrical properties, making it suitable for electronics and industrial applications.
- Disadvantages: Requires high temperatures, specialized equipment, and post-processing steps like transfer to other substrates.
-
Epitaxial Growth on Silicon Carbide (SiC):
- Graphene is formed by sublimating silicon from a silicon carbide substrate at high temperatures.
- Advantages: Produces high-quality graphene directly on an insulating substrate, ideal for electronic applications.
- Disadvantages: Expensive due to the high cost of SiC substrates and the need for high-temperature processing.
-
Arc Discharge and Laser Ablation:
- These methods involve vaporizing carbon sources using high-energy processes to form graphene.
- Advantages: Can produce graphene with unique properties, such as tailored edge structures.
- Disadvantages: Limited scalability, high energy consumption, and challenges in controlling graphene quality.
-
-
Comparison of Methods
- Quality: Mechanical exfoliation and CVD produce the highest-quality graphene, while liquid-phase exfoliation and GO reduction yield graphene with more defects.
- Scalability: CVD and liquid-phase exfoliation are more scalable than mechanical exfoliation and epitaxial growth.
- Cost: CVD and GO reduction are more cost-effective for large-scale production compared to epitaxial growth and arc discharge.
-
Applications:
- Mechanical exfoliation is used for fundamental research.
- CVD is ideal for electronics and industrial applications.
- Liquid-phase exfoliation and GO reduction are suitable for applications like composites and coatings.
-
Emerging Techniques
-
Modified CVD for Single Crystal Graphene:
- Techniques like annealing under hydrogen or using single-crystal substrates improve the quality of CVD-grown graphene.
- Advantages: Produces high-quality, large-area single-crystal graphene.
- Disadvantages: Requires precise control over growth conditions and substrate preparation.
-
Electrochemical Exfoliation:
- A newer method where graphite is exfoliated using electrochemical processes.
- Advantages: Scalable, environmentally friendly, and produces graphene with fewer defects compared to chemical oxidation.
- Disadvantages: Still under development, with challenges in controlling graphene thickness and quality.
-
-
Choosing the Right Method
- For research and fundamental studies, mechanical exfoliation is preferred due to its high-quality output.
- For industrial applications, CVD is the most promising due to its scalability and ability to produce high-quality graphene.
- For cost-sensitive applications, GO reduction and liquid-phase exfoliation are more suitable, despite their limitations in graphene quality.
In conclusion, the choice of graphene synthesis method depends on the specific requirements of the application, balancing factors like quality, scalability, and cost. Each method has its strengths and weaknesses, and ongoing research continues to improve these techniques for better performance and broader applicability.
Summary Table:
Method | Type | Advantages | Disadvantages | Best For |
---|---|---|---|---|
Mechanical Exfoliation | Top-Down | High-quality graphene, minimal defects | Not scalable, low yield | Fundamental research |
GO Reduction | Top-Down | Scalable, cost-effective | Defects and impurities | Composites, coatings |
Liquid-Phase Exfoliation | Top-Down | Mass production, solution-based processing | Lower quality, aggregation issues | Composites, coatings |
Chemical Vapor Deposition (CVD) | Bottom-Up | Large-area, high-quality graphene, excellent electrical properties | High temperature, specialized equipment, post-processing | Electronics, industrial applications |
Epitaxial Growth on SiC | Bottom-Up | High-quality graphene on insulating substrate | Expensive, high-temperature processing | Electronic applications |
Arc Discharge/Laser Ablation | Bottom-Up | Unique properties, tailored edge structures | Limited scalability, high energy consumption | Specialized applications |
Need help choosing the right graphene synthesis method for your application? Contact our experts today!