Carbon nanotubes (CNTs) are primarily grown using methods like laser ablation, arc discharge, and chemical vapor deposition (CVD), with CVD being the most commercially viable. Emerging techniques focus on sustainability, utilizing green or waste feedstocks such as carbon dioxide captured via electrolysis in molten salts and methane pyrolysis. These methods aim to improve efficiency, reduce environmental impact, and expand the applications of CNTs in various industries.
Key Points Explained:
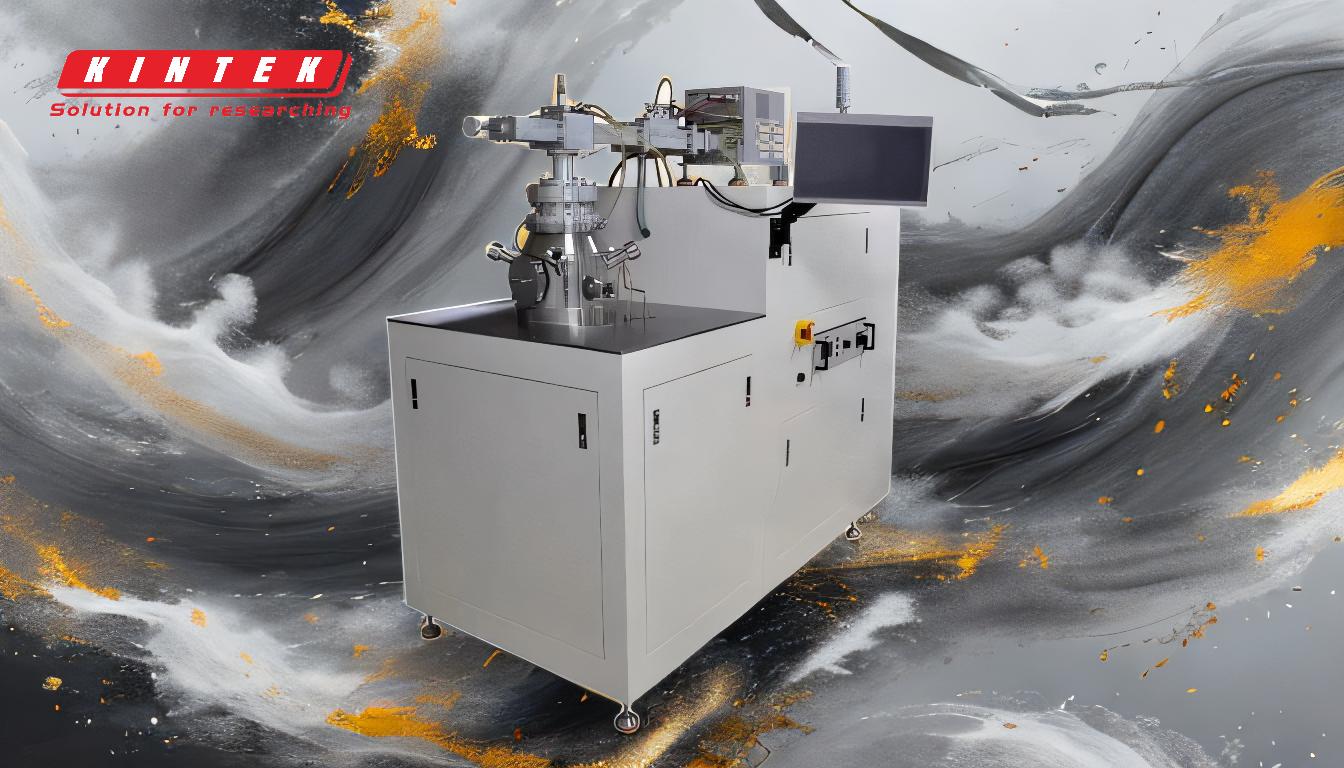
-
Traditional Methods of Nanotube Growth:
- Laser Ablation: This method involves using a high-power laser to vaporize a carbon target in the presence of a catalyst. The vaporized carbon condenses to form nanotubes. While effective, it is energy-intensive and less scalable for commercial production.
- Arc Discharge: In this technique, an electric arc is generated between two carbon electrodes in an inert gas atmosphere. The arc vaporizes the carbon, which then forms nanotubes. This method is relatively simple but produces a mixture of nanotube types and requires extensive purification.
-
Chemical Vapor Deposition (CVD):
- CVD is the most widely used method for commercial nanotube production. It involves decomposing a carbon-containing gas (such as methane or ethylene) on a substrate coated with a metal catalyst (e.g., iron, nickel, or cobalt) at high temperatures.
- The process allows for precise control over nanotube diameter, length, and alignment, making it suitable for large-scale production and specific applications like electronics and composites.
-
Emerging Sustainable Methods:
- Carbon Dioxide Electrolysis in Molten Salts: This innovative approach captures carbon dioxide and converts it into carbon nanotubes using electrolysis in molten salts. It offers a sustainable way to utilize greenhouse gases while producing high-quality nanotubes.
- Methane Pyrolysis: Methane is thermally decomposed in the absence of oxygen to produce hydrogen and solid carbon, which can be processed into nanotubes. This method is gaining attention for its potential to produce clean hydrogen alongside valuable carbon materials.
-
Advantages of Emerging Methods:
- Environmental Benefits: Utilizing waste or green feedstocks reduces reliance on fossil fuels and minimizes carbon emissions.
- Cost Efficiency: These methods can lower production costs by using readily available or waste materials.
- Scalability: Emerging techniques are being optimized for large-scale production, making them viable for industrial applications.
-
Challenges and Future Directions:
- Purity and Quality Control: Ensuring consistent nanotube quality remains a challenge, especially for emerging methods.
- Catalyst Optimization: Developing efficient and reusable catalysts is crucial for improving yield and reducing costs.
- Integration with Existing Processes: Scaling up sustainable methods requires integrating them into current manufacturing workflows without disrupting production.
By combining traditional and emerging methods, the nanotube growth process is evolving to meet the demands of modern industries while addressing environmental concerns.
Summary Table:
Method | Description | Advantages | Challenges |
---|---|---|---|
Laser Ablation | Uses a high-power laser to vaporize carbon in the presence of a catalyst. | Effective for nanotube formation. | Energy-intensive, less scalable for commercial production. |
Arc Discharge | Generates an electric arc between carbon electrodes in an inert gas atmosphere. | Simple process, relatively easy to implement. | Produces mixed nanotube types, requires extensive purification. |
Chemical Vapor Deposition | Decomposes carbon-containing gas on a catalyst-coated substrate at high temps. | Precise control over nanotube properties, scalable for commercial production. | Requires high temperatures and specific catalysts. |
CO2 Electrolysis in Molten Salts | Converts CO2 into nanotubes using electrolysis in molten salts. | Sustainable, utilizes greenhouse gases, produces high-quality nanotubes. | Requires optimization for large-scale production. |
Methane Pyrolysis | Thermally decomposes methane to produce hydrogen and solid carbon for nanotubes. | Produces clean hydrogen and valuable carbon materials, sustainable. | Needs efficient catalysts and integration into existing processes. |
Learn more about nanotube growth methods and their applications—contact our experts today!