Rotary kilns are essential in various industries, but they come with several operational and maintenance challenges. Common problems include burner-related issues, refractory failure, thermal expansion, dust generation, low thermal efficiency, and non-uniform product quality. Burner components like nozzles, cones, and sensors can fail, requiring upgrades for better efficiency. Refractory linings are prone to cracking due to thermal cycling and chemical incompatibility. Long kilns face challenges with thermal expansion, while large diameters can lead to shell deformation. Poor installation can cause alignment issues, drum damage, and warranty concerns. Addressing these problems requires careful design, installation, and maintenance to ensure optimal performance and longevity.
Key Points Explained:
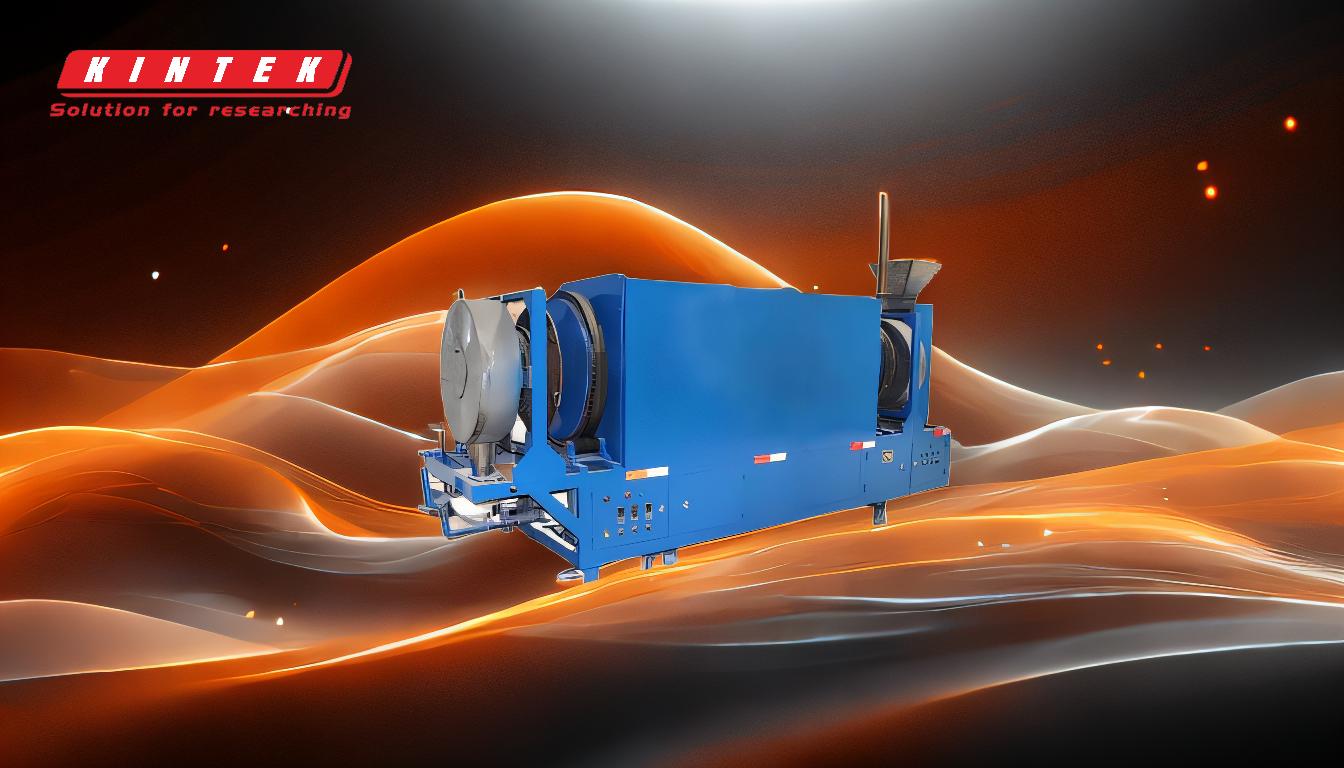
-
Burner-Related Issues:
- Burner Nozzle, Cone, and Sensors: These components are critical for efficient combustion. Wear and tear or improper functioning can lead to inefficient fuel use and reduced material output.
- Upgrading Burners: Older kilns benefit from burner upgrades, which can significantly improve energy efficiency and output quality.
-
Refractory Failure:
- Thermal Cycling: Repeated heating and cooling cycles cause the refractory lining to expand and contract, leading to cracks and eventual failure.
- Chemical Incompatibility: Exposure to certain chemicals, such as chlorides, can accelerate refractory wear and lead to premature failure.
-
Thermal Expansion and Shell Deformation:
- Length Challenges: Very long kilns struggle with thermal expansion and contraction, which can affect the structural integrity and alignment of the kiln.
- Diameter Limitations: Large diameters can cause the shell to deform under its own weight, leading to flexure during rotation and potential operational issues.
-
Operational Challenges:
- Dust Generation: Rotary kilns can produce significant amounts of dust, which can be a health hazard and require effective dust management systems.
- Low Thermal Efficiency: Inefficient heat transfer and insulation can lead to high energy consumption and increased operational costs.
- Non-Uniform Product Quality: Variations in temperature and material flow can result in inconsistent product quality, affecting the final output.
-
Installation Issues:
- Poor Alignment: Improper alignment during installation can cause damage to wheels or tires, leading to operational inefficiencies and increased wear.
- Drum Shell Damage: Mishandling during installation can damage the drum shell, necessitating costly repairs or replacements.
- Warranty Concerns: Missing critical hold points or inspections during installation can void warranties, leading to additional costs and potential legal issues.
Addressing these problems requires a comprehensive approach, including regular maintenance, proper installation practices, and potential upgrades to improve efficiency and product quality. Understanding these challenges helps in making informed decisions for the procurement and operation of rotary kilns.
Summary Table:
Challenge | Key Issues | Solutions |
---|---|---|
Burner-Related Issues | Nozzle, cone, and sensor failures; inefficient fuel use | Upgrade burners for better efficiency and output quality |
Refractory Failure | Cracking due to thermal cycling; chemical incompatibility | Use compatible materials; monitor and repair refractory linings regularly |
Thermal Expansion | Structural integrity issues in long kilns; shell deformation in large diameters | Design for thermal expansion; reinforce shell structure |
Operational Challenges | Dust generation; low thermal efficiency; non-uniform product quality | Implement dust management; improve insulation; optimize temperature control |
Installation Issues | Poor alignment; drum shell damage; warranty concerns | Ensure proper alignment and handling; follow installation guidelines strictly |
Need help optimizing your rotary kiln performance? Contact our experts today for tailored solutions!