Brazing is a widely used joining method that offers several advantages, such as the ability to join complex parts, reduce thermal distortion, and maintain close tolerances. However, despite its benefits, brazing is not without its challenges. The process involves heating a filler metal to its melting point to form a strong joint between two or more base metals without melting them. While this approach preserves the integrity of the base metals, it introduces specific problems that can affect the quality and reliability of the joint. These issues include controlling the dwell temperature and time, ensuring proper filler metal flow, managing oxidation, and addressing joint design complexities.
Key Points Explained:
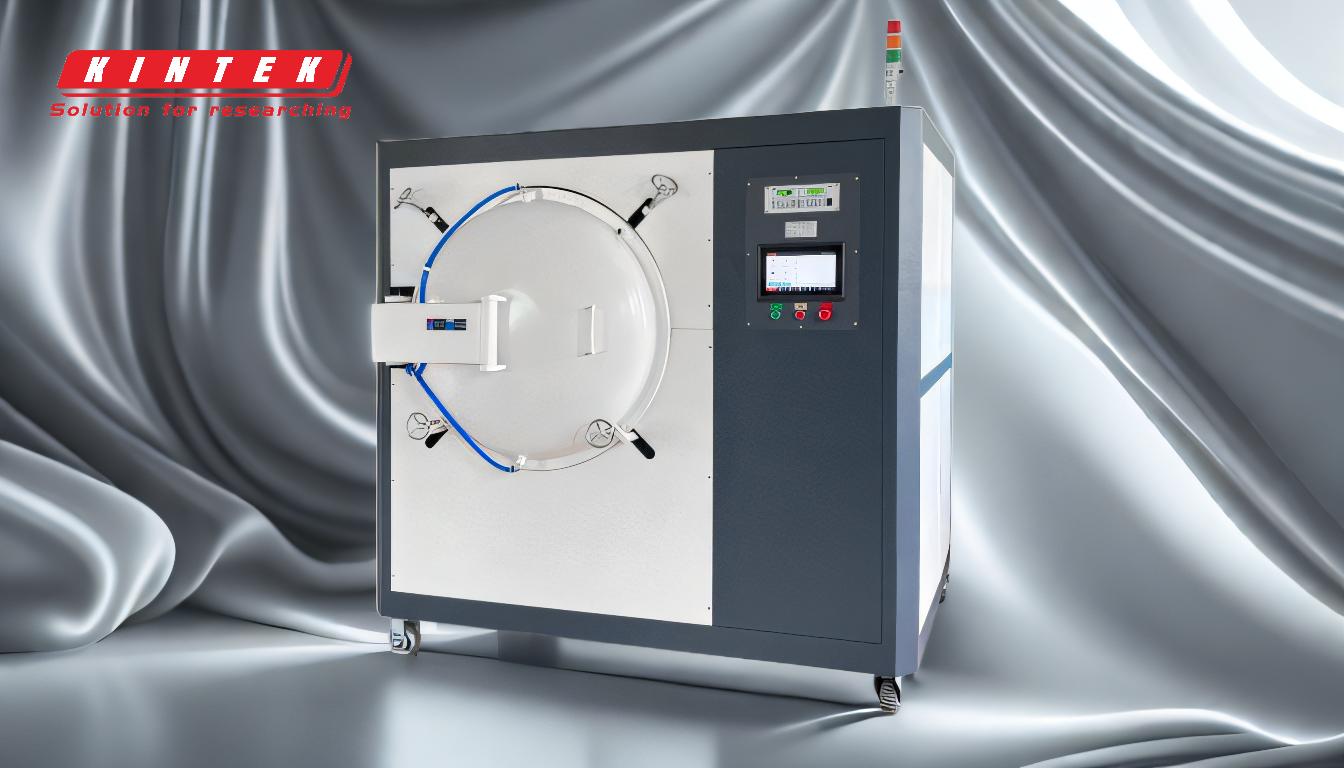
-
Control of Dwell Temperature and Time
- One of the critical parameters in brazing is the dwell temperature, which must be precisely controlled to ensure the filler metal melts and flows properly without overheating the base metals.
- If the temperature is too low, the filler metal may not melt adequately, leading to incomplete joints. Conversely, excessive heat can damage the base metals or cause distortion.
- The dwell time, or the duration the assembly is held at the brazing temperature, must also be optimized. Insufficient time can result in poor wetting and bonding, while excessive time can lead to excessive intermetallic formation or base metal degradation.
-
Filler Metal Flow and Wetting
- Proper flow and wetting of the filler metal are essential for creating a strong, uniform joint. Poor wetting can occur due to surface contamination, improper flux application, or inadequate cleaning of the base metals.
- Surface oxides and contaminants can prevent the filler metal from adhering to the base metals, resulting in weak or incomplete joints.
- The choice of filler metal and flux is critical to ensure compatibility with the base metals and to promote effective wetting and flow.
-
Oxidation and Surface Preparation
- Oxidation is a significant concern in brazing, as the presence of oxides on the surface of the base metals can hinder the bonding process.
- Proper surface preparation, including cleaning and the application of flux, is necessary to remove oxides and contaminants. Fluxes are used to dissolve oxides and protect the surfaces from further oxidation during heating.
- In some cases, a controlled atmosphere or vacuum environment may be required to prevent oxidation and ensure a clean joint.
-
Joint Design and Fit-Up
- The design of the joint plays a crucial role in the success of the brazing process. Joints must be designed to allow proper capillary action, which draws the filler metal into the gap between the base metals.
- A tight fit-up is essential to ensure uniform filler metal distribution and strong bonding. Excessive gaps can lead to weak joints, while insufficient gaps can restrict filler metal flow.
- Complex geometries or dissimilar materials can pose additional challenges, requiring careful consideration of joint design and process parameters.
-
Thermal Management and Distortion
- Although brazing produces less thermal distortion compared to welding, it is not entirely free from thermal effects. Uneven heating or cooling can cause residual stresses or distortion in the assembled parts.
- Proper fixturing and controlled heating/cooling rates are necessary to minimize these effects and ensure dimensional stability.
- In some cases, post-brazing heat treatment may be required to relieve stresses and improve joint properties.
-
Material Compatibility
- Brazing is often used to join dissimilar materials, but differences in thermal expansion coefficients, melting points, and chemical reactivity can complicate the process.
- Selecting compatible filler metals and fluxes is critical to avoid issues such as cracking, brittleness, or poor adhesion.
- Pre-brazing testing and process optimization may be necessary to address material compatibility challenges.
-
Quality Control and Inspection
- Ensuring the quality of brazed joints requires rigorous inspection and testing. Non-destructive testing methods, such as visual inspection, dye penetrant testing, or X-ray imaging, are commonly used to detect defects like voids, cracks, or incomplete joints.
- Process monitoring and control are essential to maintain consistency and reliability in high-volume production environments.
- Post-brazing cleaning may also be required to remove residual flux or oxides, which can affect the appearance and performance of the joint.
In summary, while brazing is a versatile and effective joining method, it requires careful attention to process parameters, material compatibility, and joint design to overcome its inherent challenges. By addressing these issues, manufacturers can achieve strong, reliable, and high-quality brazed joints.
Summary Table:
Challenge | Key Issues | Solutions |
---|---|---|
Dwell Temperature & Time | Incomplete joints or base metal damage due to improper heat control. | Precise temperature control and optimized dwell time. |
Filler Metal Flow & Wetting | Poor wetting due to contamination or improper flux application. | Proper surface cleaning, flux selection, and filler metal compatibility. |
Oxidation | Oxides hinder bonding, requiring controlled environments. | Use of flux, controlled atmospheres, or vacuum environments. |
Joint Design & Fit-Up | Improper capillary action or gaps affect joint strength. | Tight fit-up and well-designed joints for uniform filler distribution. |
Thermal Management | Residual stresses or distortion from uneven heating/cooling. | Controlled heating/cooling rates and proper fixturing. |
Material Compatibility | Cracking or brittleness due to dissimilar material properties. | Pre-brazing testing and optimization of filler metals and fluxes. |
Quality Control | Defects like voids, cracks, or incomplete joints. | Rigorous inspection, testing, and post-brazing cleaning. |
Need help overcoming brazing challenges? Contact our experts today for tailored solutions!