Sintering is a critical process in metallurgy and materials science that involves heating powdered materials below their melting point to form a solid, dense structure. This process enhances the mechanical properties of materials, such as strength, hardness, and wear resistance, by bonding particles and reducing porosity. Sintering can be achieved through methods like transient and permanent liquid phase sintering, which involve the addition of materials like copper or carbide to facilitate bonding. The process is energy-efficient and environmentally friendly compared to melting, and it allows for precise control over material properties by influencing grain size, pore size, and grain boundary distribution. Key raw materials for sintering include iron-containing materials, melting agents, and fuel, each with specific requirements to ensure optimal results.
Key Points Explained:
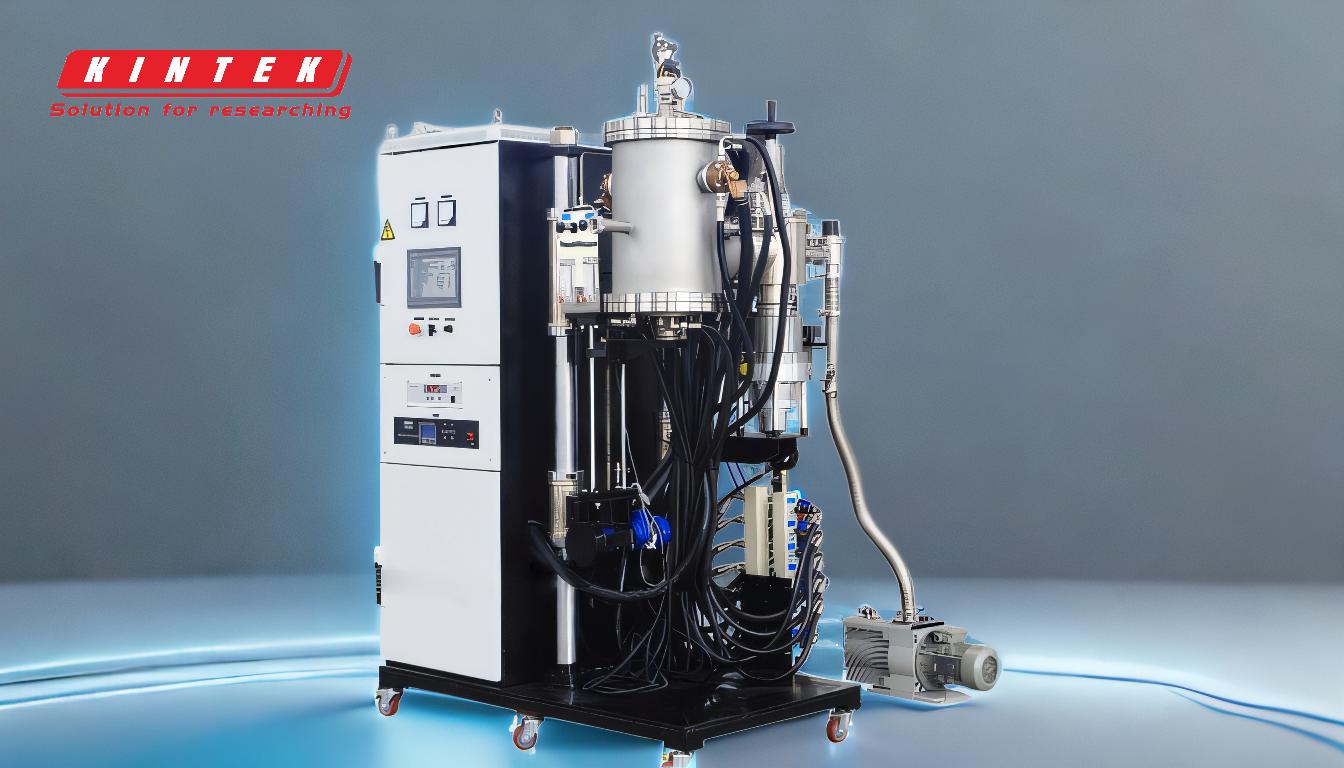
-
Definition and Purpose of Sintering:
- Sintering is a heat treatment process where powdered materials are heated below their melting point to form a dense, solid structure.
- The primary purpose is to enhance material properties such as strength, durability, and wear resistance by reducing porosity and bonding particles.
-
Mechanical Property Enhancement:
- Sintering improves mechanical properties like strength, hardness, and wear resistance.
- The process involves particle bonding and densification, leading to a cohesive and dense structure.
- Controlled heating and diffusion mechanisms contribute to the development of a robust material microstructure.
-
Types of Sintering Methods:
- Transient Liquid Phase Sintering: Involves adding a material like copper to iron powder. The copper melts at sintering temperatures, fusing with the iron and hardening the material.
- Permanent Liquid Phase Sintering: Involves adding liquid materials like carbide, which flow into openings and cracks, further bonding the materials.
-
Raw Materials for Sintering:
- Iron-containing Raw Materials: Include high iron content ore powder, iron concentrate, blast furnace dust, rolled steel, and steel residue.
- Melting Agents: Require high valid CaO content, low impurities, stable ingredients, and specific water content and particle size.
- Fuel: Mainly includes coke powder and smokeless coal, with requirements for high fixed carbon content, low ash, low volatile matter, low sulfur content, stable ingredients, and specific water content and particle size.
-
Energy Efficiency and Environmental Benefits:
- Sintering requires less energy than melting the same metal, making it an environmentally friendly option.
- The process allows for greater control over the manufacturing process, resulting in more consistent and high-quality products.
-
Microstructural Changes:
- Sintering affects grain size, pore size, and grain boundary shape and distribution in the material's microstructure.
- These changes influence the material's properties, such as its strength and durability.
-
Physical and Chemical Changes During Sintering:
- Evaporation or Removal of Water/Organic Matter: This step ensures the material is free from impurities that could affect the sintering process.
- Removal of Adsorbed Gases: Helps in achieving a denser and more cohesive structure.
- Stress Relief: Reduces internal stresses within the material.
- Reduction of Surface Oxides: Ensures better bonding between particles.
- Material Migration, Recrystallization, and Grain Growth: These processes contribute to the development of a dense and cohesive structure, enhancing the overall mechanical integrity of the component.
By understanding these key points, one can appreciate the complexity and importance of the sintering process in producing high-performance materials with enhanced mechanical properties.
Summary Table:
Aspect | Details |
---|---|
Definition | Heating powdered materials below melting point to form a dense, solid structure. |
Purpose | Enhances strength, hardness, and wear resistance by reducing porosity. |
Methods | Transient and permanent liquid phase sintering using materials like copper or carbide. |
Raw Materials | Iron-containing materials, melting agents, and fuel with specific requirements. |
Benefits | Energy-efficient, environmentally friendly, and precise control over material properties. |
Microstructural Changes | Influences grain size, pore size, and grain boundary distribution. |
Learn how sintering can transform your materials—contact our experts today for more insights!