Heat treatment is a critical process in manufacturing and materials engineering, offering numerous advantages such as altering physical properties, improving strength, flexibility, and wear resistance, and enhancing machinability. However, it also has drawbacks, including potential material distortion, increased costs, and limitations in application for certain materials. Understanding the pros and cons of heat treatment is essential for making informed decisions in material selection and manufacturing processes.
Key Points Explained:
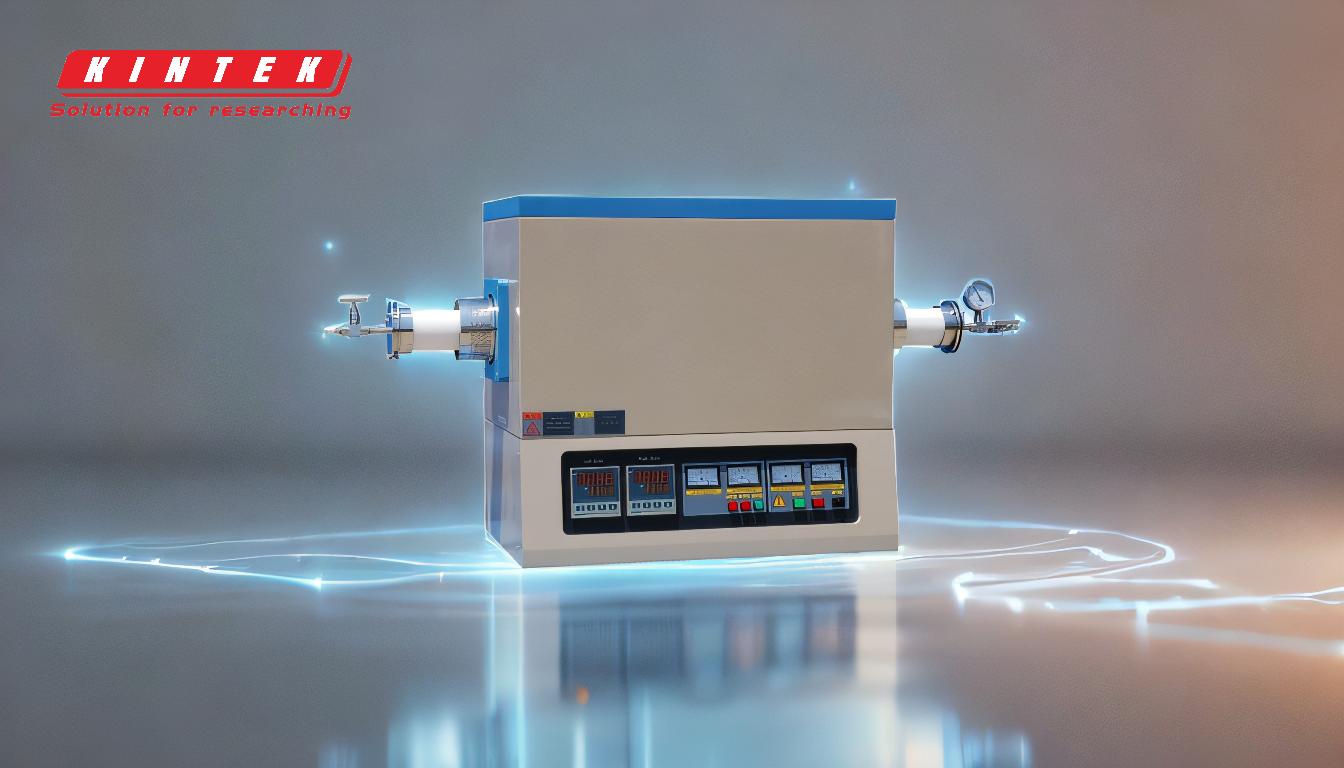
-
Advantages of Heat Treatment:
- Altering Physical Properties: Heat treatment can significantly change a material's physical properties, such as hardness, strength, and flexibility. This makes it possible to tailor materials to specific applications, enhancing their performance and durability.
- Stress Relief: The process helps in relieving internal stresses in materials, making them easier to machine or weld. This is particularly beneficial after welding or hot forming processes.
- Enhanced Mechanical Properties: By controlling the rate of cooling and diffusion within the metal's microstructure, heat treatment can improve properties like toughness, ductility, and elasticity.
- Wear Resistance: Introducing wear-resistant characteristics through heat treatment extends the lifespan of components, especially in high-friction environments.
- Improved Brittleness: Heat treatment can reduce brittleness, making materials less prone to cracking or breaking under stress.
- Electrical and Magnetic Properties: Certain heat treatments can enhance electrical conductivity and magnetic properties, which are crucial for specific industrial applications.
-
Disadvantages of Heat Treatment:
- Material Distortion: One of the primary drawbacks is the potential for material distortion or warping due to uneven heating and cooling. This can affect the dimensional accuracy of parts.
- Increased Costs: Heat treatment processes often require specialized equipment and energy, leading to higher production costs. Additionally, post-treatment machining may be necessary to correct distortions.
- Limitations in Application: Not all materials respond well to heat treatment. For example, some non-ferrous metals and plastics may not benefit from or may even be damaged by the process.
- Complexity and Control: Achieving the desired properties requires precise control over temperature, cooling rates, and other variables. Any deviation can lead to suboptimal results.
- Environmental Concerns: Heat treatment processes can generate emissions and waste, necessitating proper environmental controls and disposal methods.
-
Applications and Considerations:
- Steel Manufacturing: Heat treatment is particularly beneficial for steel, enhancing its properties for use in construction, automotive, and aerospace industries.
- Material Selection: When choosing materials for a project, it's essential to consider whether heat treatment is necessary and whether the material is suitable for the process.
- Cost-Benefit Analysis: Weighing the advantages against the potential costs and drawbacks is crucial for determining the feasibility of heat treatment in a given application.
In summary, while heat treatment offers numerous benefits in improving material properties and performance, it also comes with challenges such as potential distortion, increased costs, and environmental considerations. A thorough understanding of these factors is essential for optimizing manufacturing processes and achieving desired outcomes.
Summary Table:
Aspect | Advantages | Disadvantages |
---|---|---|
Physical Properties | Alters hardness, strength, flexibility | Potential material distortion or warping |
Stress Relief | Reduces internal stresses, improves machinability | Increased costs due to specialized equipment and energy |
Mechanical Properties | Enhances toughness, ductility, and elasticity | Not all materials are suitable for heat treatment |
Wear Resistance | Extends component lifespan in high-friction environments | Requires precise control over temperature and cooling rates |
Brittleness | Reduces brittleness, prevents cracking | Environmental concerns due to emissions and waste |
Electrical/Magnetic | Improves conductivity and magnetic properties for specific applications | Post-treatment machining may be necessary to correct distortions |
Need help optimizing your heat treatment process? Contact our experts today for tailored solutions!