Hot forging is a widely used manufacturing process that involves shaping metal at high temperatures. While it offers several advantages, such as improved material properties and reduced production time, it also comes with certain drawbacks. This analysis explores the pros and cons of hot forging, focusing on its impact on material microstructure, production costs, design limitations, and economic feasibility for different production scales.
Key Points Explained:
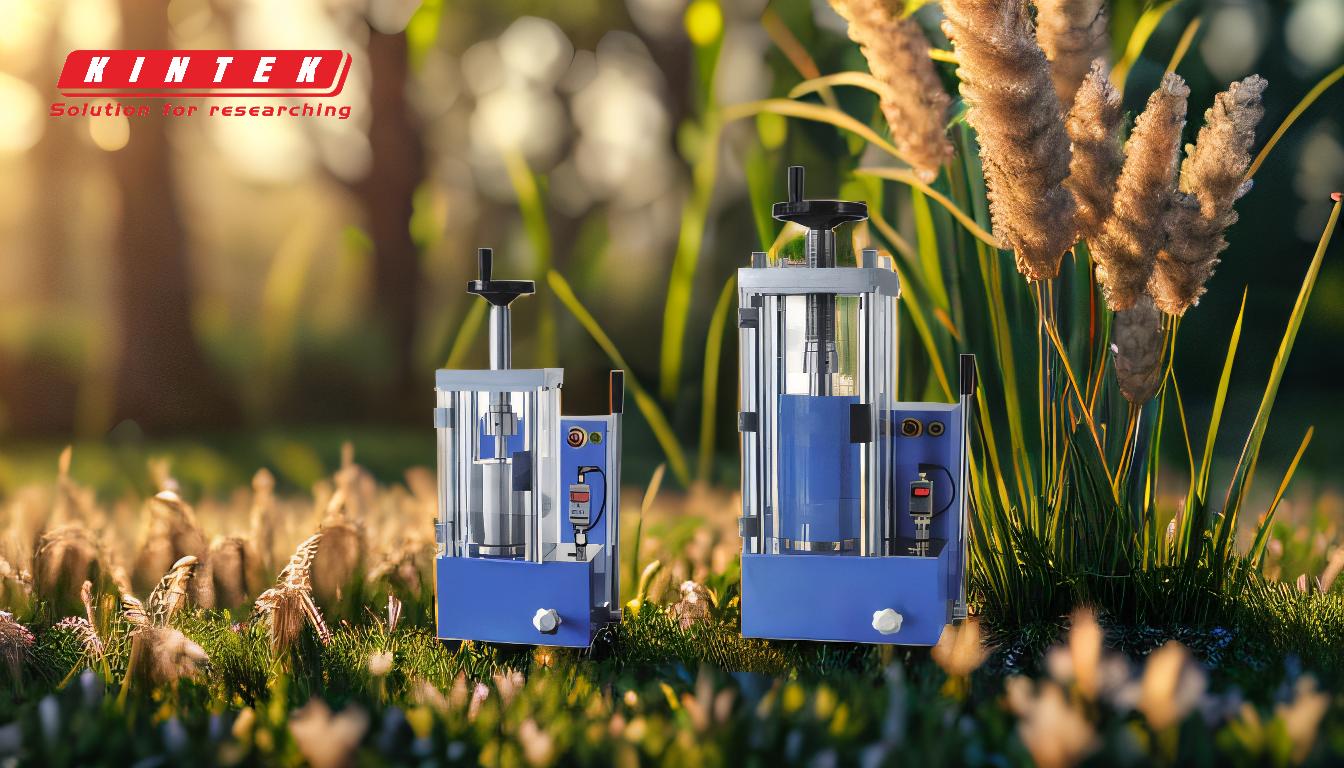
-
Advantages of Hot Forging:
- Improved Material Properties: Hot forging enhances the mechanical properties of metals, such as strength, toughness, and ductility, by refining the grain structure and eliminating internal voids or defects.
- Reduced Production Time: The process allows for faster shaping of metals compared to cold forging, as the material is more malleable at high temperatures.
- Cost-Effective for Large Production Runs: For high-volume production, the initial investment in dies and tooling can be justified, making it economically viable.
-
Disadvantages of Hot Forging:
- Lack of Microstructure Control: One of the primary drawbacks is the limited control over the microstructure of the material. This can lead to inconsistencies in mechanical properties if not properly managed.
- Need for Secondary Machining: Hot forging often requires additional machining to achieve precise dimensions and surface finishes, which increases project costs and lead times.
- Design Limitations: The process is unsuitable for producing small, intricate parts or components with complex geometries without subsequent machining.
- Inability to Produce Certain Materials: Hot forging cannot be used to create porous bearings, sintered carbides, or parts that require a mix of multiple metals.
- High Initial Costs: Die production is expensive, making short production runs economically undesirable. This limits the feasibility of hot forging for low-volume or custom projects.
-
Economic Considerations:
- Cost of Dies and Tooling: The high cost of dies and tooling is a significant factor, particularly for small-scale production. This makes hot forging more suitable for large-scale manufacturing.
- Secondary Processing Costs: The need for additional machining and finishing steps adds to the overall cost, which must be factored into the project budget.
-
Material and Application Constraints:
- Unsuitable for Certain Applications: Hot forging is not ideal for applications requiring porous materials, mixed metals, or highly detailed designs.
- Limited Flexibility: The process is less flexible compared to other manufacturing methods, such as casting or additive manufacturing, which can accommodate a wider range of materials and designs.
-
Comparison with Other Manufacturing Processes:
- Versus Cold Forging: While cold forging offers better dimensional accuracy and surface finish, it requires more force and is less suitable for high-strength materials.
- Versus Casting: Casting can produce more complex shapes and porous structures, but it often results in lower mechanical properties compared to forged parts.
In summary, hot forging is a powerful manufacturing process with significant advantages in terms of material properties and production efficiency. However, its limitations in microstructure control, design flexibility, and economic feasibility for small-scale production must be carefully considered when selecting it for a specific application.
Summary Table:
Aspect | Pros | Cons |
---|---|---|
Material Properties | Improved strength, toughness, and ductility | Limited control over microstructure |
Production Time | Faster shaping compared to cold forging | Requires secondary machining for precision |
Cost Efficiency | Economical for large-scale production | High initial costs for dies and tooling |
Design Flexibility | Suitable for high-strength materials | Limited for small, intricate, or porous designs |
Economic Feasibility | Cost-effective for high-volume runs | Less viable for low-volume or custom projects |
Discover how hot forging can optimize your manufacturing process—contact our experts today!