Pyrolysis reactors are specialized equipment designed to thermally decompose materials in the absence of oxygen, producing valuable products like gases, oils, and char. The choice of reactor type depends on the feedstock, desired products, and operational efficiency. Key reactor types include fixed-bed, fluidized-bed, and wire-mesh reactors, each with unique advantages. Fixed-bed reactors are simple and cost-effective, fluidized-bed reactors offer excellent heat transfer and mixing, and wire-mesh reactors are ideal for rapid heating and tar recovery. Additionally, pyrolysis reactors are constructed from high-temperature-resistant materials like Q245R and Q345R steel to ensure durability and efficiency. The feeding system and heat sources, such as conventional heating and microwave energy, further enhance the process.
Key Points Explained:
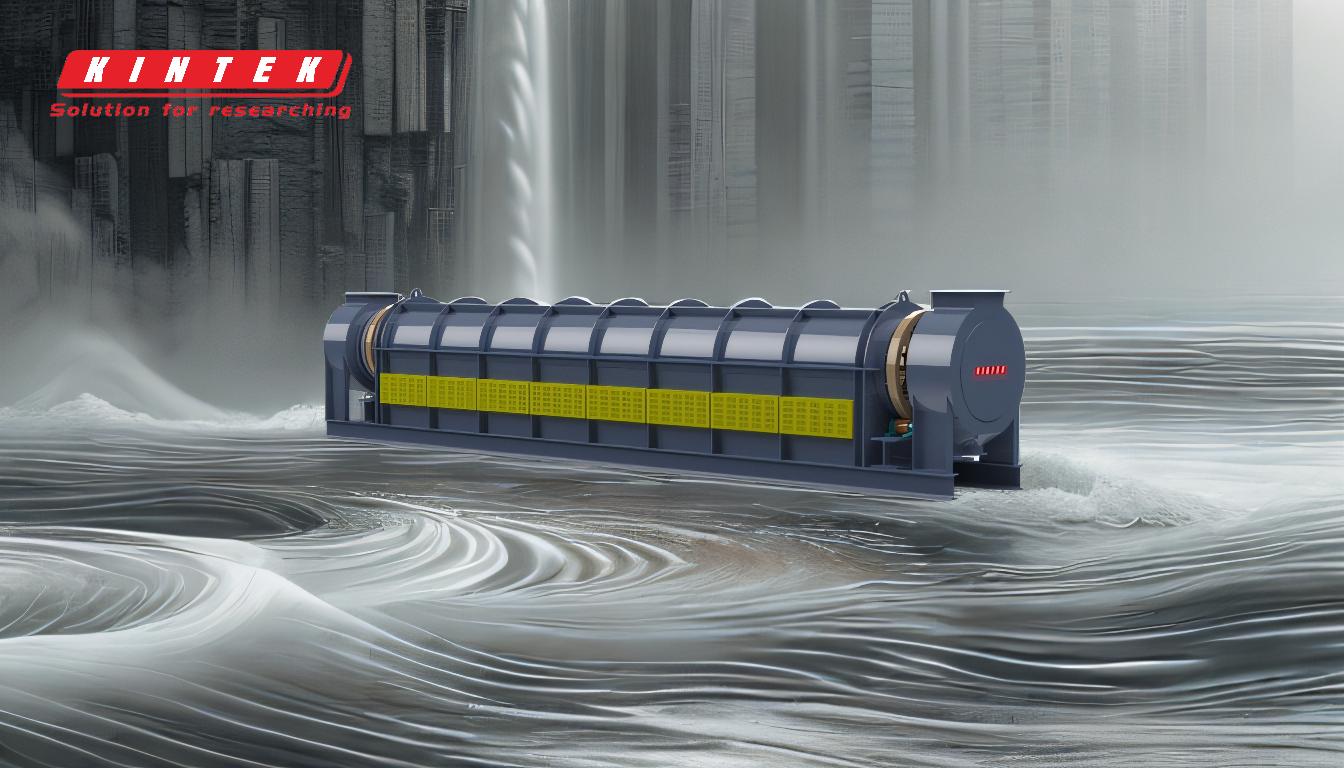
-
Types of Pyrolysis Reactors:
- Fixed-Bed Reactors: These are the simplest and most cost-effective reactors, suitable for small-scale operations. They operate by heating the feedstock in a stationary chamber, making them ideal for batch processing.
- Fluidized-Bed Reactors: These reactors use a bed of inert particles (like sand) that are fluidized by a gas stream. They provide excellent heat transfer and mixing, making them suitable for continuous operations and large-scale industrial applications.
- Wire-Mesh Reactors: These reactors are designed for rapid heating and are particularly useful for studying the kinetics of pyrolysis. The shallow heated reaction section allows volatiles to clear quickly, enabling the recovery of tar samples with minimal structural changes.
-
Construction Materials:
- Pyrolysis reactors are typically made from high-temperature-resistant materials like Q245R and Q345R steel. These materials ensure the reactors can withstand the extreme temperatures involved in pyrolysis, enhancing their service life to 5-8 years. The main reactor body, doors, front and rear headers, and sealing plates are all constructed from these durable materials to ensure heat transfer efficiency and equipment longevity.
-
Feeding Systems:
- The feeding system in a pyrolysis setup is crucial for delivering raw materials to the reactor in a fully sealed and automated manner. Beston, for example, offers several feeding system options tailored to different materials and capacities, ensuring efficient and safe operation. This automation reduces manual intervention and enhances the overall safety and efficiency of the pyrolysis process.
-
Heat Sources:
- Conventional Heat Sources: These include electric heaters, gas burners, and other traditional heating methods. They are widely used due to their reliability and ease of control.
- Microwave Energy: This is an emerging heat source that offers rapid and uniform heating. Microwave-assisted pyrolysis is particularly effective for certain types of feedstocks, providing faster reaction times and potentially higher yields of desired products.
-
Applications of Pyrolysis Reactors:
- Pyrolysis reactors are extensively used in the chemical industry to produce ethylene, various forms of carbon, and other chemicals from petroleum, coal, and wood. They are also employed in converting natural gas into hydrogen gas and solid carbon char. Additionally, pyrolysis has aspirational applications in converting biomass into syngas and biochar, waste plastics into usable oil, and waste into safely disposable substances.
By understanding these key aspects, equipment and consumable purchasers can make informed decisions about the type of pyrolysis reactor that best suits their specific needs, ensuring optimal performance and efficiency in their operations.
Summary Table:
Reactor Type | Key Features | Applications |
---|---|---|
Fixed-Bed Reactors | Simple, cost-effective, ideal for small-scale and batch processing | Small-scale operations, batch processing |
Fluidized-Bed | Excellent heat transfer and mixing, suitable for continuous and large-scale use | Industrial applications, continuous operations |
Wire-Mesh Reactors | Rapid heating, ideal for tar recovery and kinetic studies | Research, tar recovery, rapid heating applications |
Construction | Made from Q245R/Q345R steel for durability and high-temperature resistance | Ensures long service life (5-8 years) and efficient heat transfer |
Heat Sources | Conventional (electric, gas) or microwave energy for rapid, uniform heating | Enhances reaction times and yields of desired products |
Ready to optimize your pyrolysis process? Contact our experts today to find the perfect reactor for your needs!